The Battle for High-End Chemical Materials: What Key Challenges Does Our Country Still Face?
"The Counterattack of the 'Plastic War'"
More than a decade ago, the dilemma of domestic engineering plastics was "relying on imports for high-end products and looking to Europe and America for prices."
In the past two years with new energy vehicles,5Gtechnology, domestically produced large aircraft, low-altitude small aircraft, intelligent robots, and other high-end fields have risen, and domestically produced engineering plastics have gradually come to dominate this plastic war.
But the revolution is not yet successful, and there are still three mountains to be conquered.---core technology, high-end market, green transformation, chemical material professionals still need to make efforts.
One, From "Completely at the Mercy of Others" to "Partial Victory"
Five major engineering plastics: mid-to-low end dominate the market, high end yet to be fully covered
Engineering plastics are indispensable basic raw materials in modern industry, widely used in many fields such as aerospace, automotive, electrical and electronic, and daily necessities.
Our country is the world's largest consumer of engineering plastics, and the domestic substitution process of engineering plastics has attracted significant attention in the industry.
nylon (PA):PA6andPA66general conventional products, have already achieved complete domestic substitution, butPA46、PA9THeat-resistant special nylon is still monopolized by DSM of the Netherlands and Kuraray of Japan.
Special nylon is heat-resistant and pressure-resistant, performing very well in extreme environments, especially with a large market capacity in industries such as aerospace and high-end electronics. However, its production process is complex, and the technical threshold is relatively high.
polycarbonate (PC): regular gradePCdomestic total capacity is the world's first, but opticalPC(almost entirely monopolized by Mitsubishi and SABIC)
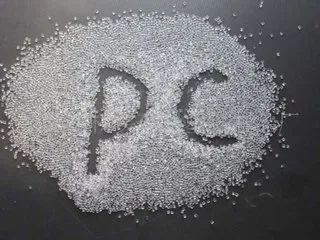
optical gradePCIt has extremely high transparency, refractive index, and other optical properties, with a complex production process and even more complex quality control. Domestic enterprises in the conventionalPCfield has dominated the market, optical gradePCthe high-end market still needs to be explored by various companies.
polyoxymethylene (POM): The localization rate of copolymer products has already exceeded90%, it was just a bit short of overcapacity. And homopolymerPOMthe core technology is still in the hands of DuPont and Asahi Kasei.
homopolymerizationPOMThe mechanical strength and wear resistance are better, which can be widely used in the manufacturing of precision machinery and high-end automotive parts.
copolymer typePOMSuccess has been achieved, and each production enterprise may need to focus on homopolymerizationPOMgot on, early breakthrough in the urban area.
Special engineering plastics: domestic substitution accelerates, but "tough nuts" are hard to crack
Special engineering plastics are key materials for high-end manufacturing, and the previous few articles have already analyzed each of the high-end materials.
PEEKA detailed analysis was conducted in the article a few days ago, so it will not be elaborated here. Domestic companies such as Zhongyan Co., Ltd. have already achieved mid-to-low endPEEKThe mass production of the product, and the production cost is lower than that of foreigners. But in high-end products and main raw materialsDFBP(difluorobenzophenone) capacity matching still faces many challenges. At the same time, the certification cycle for downstream application enterprises is long3-5year, so it's still better to plan early and benefit early.
polyimide (PI):PIThe film is mainly used in specific prospects of the electronic field, such as flexible screens,5Gcommunication, etc. flexible screen usePIThe film has broken the monopoly of foreign companies, but high-temperature resistant adhesives are still monopolized by DuPont.
LCPpossesses excellent high-temperature resistance, chemical corrosion resistance, and electrical insulation properties, in5Gantenna material domestication rate exceeds50%, but thermal conductivity/The conductive modified material technology is controlled by Japan's Polyplastics and the US's Celanese.
Fluoroplastics and Polysulfone: Electronic-grade Products as the Last Bastion
The performance and quality of fluoroplastics and polysulfones directly affect the highest level of technology in China's electronics industry.
lithium battery usePVDFandPTFElong been capable of domestic production, but semiconductor-gradePFAresin purity is insufficient90%Imported from Daikin, Japan.
PPSUexcellent high-temperature resistance, chemical corrosion resistance, and biocompatibility, for use in hemodialysis membranesPPSUSubject to Solvay of Belgium, the production equipment for film grade still needs100%import.
II. The Four "Achilles' Heels" of the Materials Industry
core raw material "supply disruption anxiety"
adiponitrile isPA66the key raw material, once caused an industry earthquake due to the supply cut by American Invista, the production process of adiponitrile is complex, with a high investment threshold, and has long been monopolized by a few international giants. Although domestic enterprises have made some breakthroughs in the production of adiponitrile, there is still much room for improvement.
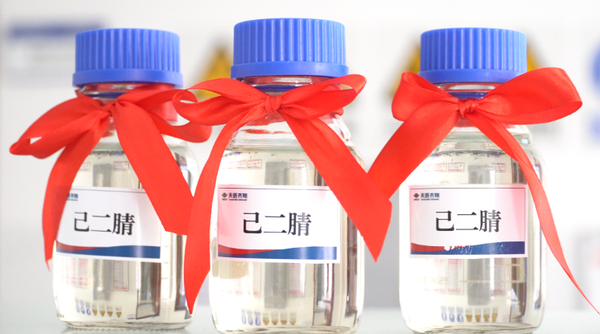
4,4-difluorobenzophenonePEEKthe core monomer, synthesis process is "patent-locked" by UK's Victrex. There are domestic enterprises with considerable production capacity, but they mainly focus on mid-to-low end products, and rely on imports for high-end products.
production equipment "generation gap"
film-grade equipment:LCPandPPSUFilm production equipment is monopolized by Japan Steel Works and Germany's Brückner, and the precision of domestically produced equipment still cannot meet the usage requirements.
film gradePSFThe specialized film equipment is almost entirely dependent on imports (rather than resin stretching processes), with extremely high requirements for equipment precision and stability, and has been exclusively supplied by companies such as Solvay and BASF. There are currently no domestic manufacturers of similar equipment.
application authentication "invisible discrimination"
medical field: domesticPEEKartificial joint needs to pass throughFDAcertification, long and difficult certification cycle, average time consumption4year, while European and American materials only need2year
Semiconductor packaging: TSMC, Samsung, and other giants only use Toray'sLCPmaterials, domestic materials are considered to have unstable quality, and their certification standards are extremely strict.
green transformation "dual-front battle"
Bio-based materials: Dow in the US has already started using corn to produce bio-based nylon and has begun mass production, while domestically it is still at the laboratory research stage.
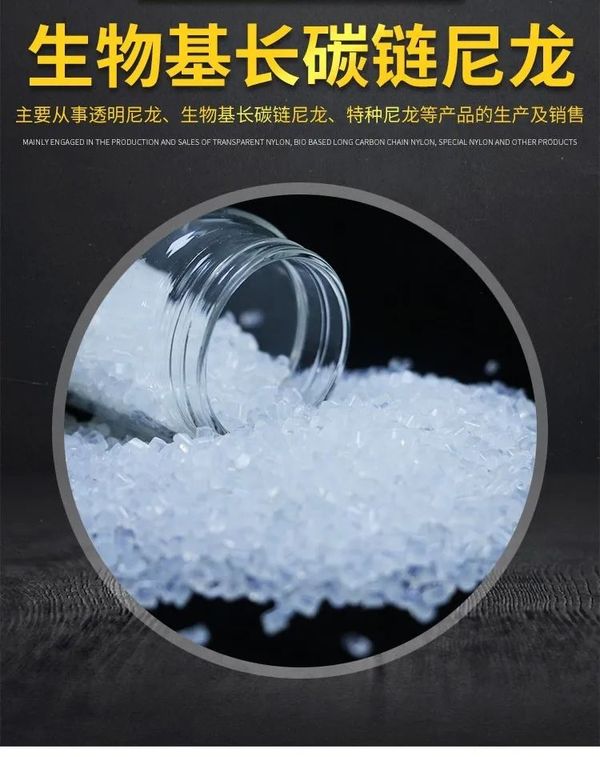
Circular economy: The recycling rate of engineering plastics in Europe has already exceeded40%, China is still insufficient20%, recycled materials are mostly used in low-end manufacturing industries, and domestic companies still need to improve recycling technologies and the value of utilizing recycled materials.
Three Sharp Knives for Breaking the Stalemate
concentrate firepower on technological breakthroughs
National Special Fund: Targeted Support for Semiconductor-LevelPFAhomopolymerizationPOMand other long-term "chokepoint" technologies, drawing on the breakthrough model of lithography machines.
industry-academia-research collaboration: establishing "materials"-equipment-application "consortium" (such as the one led by Shanghai Research Institute of Chemical IndustryPIR&D can greatly shorten the cycle of technology transformation.
From "Single Point Breakthrough" to "Ecosystem Closed Loop"
upstream raw materials: industry giants such as Wanhua and Rongsheng are accelerating the layout of adiponitrileCHDMkey monomers. Integrating industrial chain resources, upstream enterprises can ensure a stable supply of raw materials and also continuously reduce costs through technological innovation.
Downstream certification: It is possible to jointly build a material testing platform with companies such as BYD, CATL, and DJI, using the technical requirements of end products to drive the upgrade of material performance. Deep cooperation between downstream enterprises and material production enterprises can accelerate the certification process in high-end application fields.
seize the carbon neutrality track
biobased plastics: the development, application, and promotion of biobased materials, in line with the country's sustainable development policies.
Recycling technology: Develop along the three main lines of commercializing chemical recycling, innovating green processes, and integrating the industrial chain. Improving the recycling rate of engineering plastics can not only reduce resource waste but also create new economic value, achieving a green and circular development of the industry.
expected to reach by2030year, the global chemical recycling ratio will increase to15%, the penetration rate of recycled plastics in fields such as packaging and automotive exceeds30%。
Strong engineering plastics, strong manufacturing industry
Engineering plastics can be said to be the cornerstone of modern industry, and their development level is directly related to the country's competitiveness in high-end manufacturing.
Over the past decade or so, China's engineering plastics enterprises have risen to the challenge in adversity and have achieved remarkable results in most areas.
However, the competition in the high-end market, the breakthrough in core technologies, and the challenges of green transformation still require us to continue our efforts and strive for an early breakthrough.
I believe that in this "plastic war" our country will surely achieve victory, realizing a great leap from a major material country to a strong material country.
【Copyright and Disclaimer】The above information is collected and organized by PlastMatch. The copyright belongs to the original author. This article is reprinted for the purpose of providing more information, and it does not imply that PlastMatch endorses the views expressed in the article or guarantees its accuracy. If there are any errors in the source attribution or if your legitimate rights have been infringed, please contact us, and we will promptly correct or remove the content. If other media, websites, or individuals use the aforementioned content, they must clearly indicate the original source and origin of the work and assume legal responsibility on their own.
Most Popular
-
DuPont to Spin Off Nomex and Kevlar Brands for $14.4 Billion: Is Aramid Fiber Still Attractive?
-
Covestro faces force majeure!
-
Metal Stamping Supplier Autokiniton to Close Detroit Plant and Lay Off Workers
-
Napan Unveils Thermoplastic Composite Three-in-One Power System Solution, Battery Cover Weight Reduced by 67%
-
2025 Half-Year Performance Summary of 19 Listed Modified Plastics Companies