How to Adjust Additive Selection for Modified PP to Enhance Its Performance on Car Bumpers
Polypropylene (PP) is lightweight, has excellent performance, is corrosion-resistant, and easy to process and mold. Its application proportion in automotive materials continues to increase, especially in automotive bumpers, where the primary raw material is modified PP material.
However, the injection molding cycle of existing automotive bumpers is often relatively long. As a semi-crystalline polymer material, PP has certain issues related to cooling crystallization rate and demolding shrinkage rate.
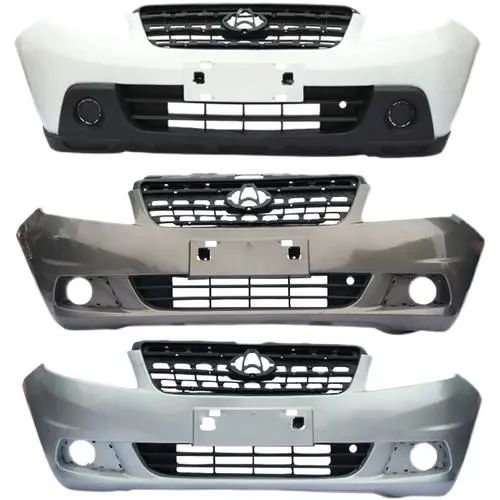
This paper focuses on the effects of various components in modified PP on the crystallization behavior, mechanical properties, rheological behavior, injection molding flow length, and injection molding cycle of modified PP. By studying these influencing factors, it seeks a modified PP solution that facilitates the reduction of the injection molding cycle for bumpers, in order to meet the automotive manufacturing industry's demand for efficient production.
1. The impact of different elastomers.
After blending four types of POE with PP at a mass ratio of 20:80, the mixture was extruded and then injection-molded into specimens. After brittle fracture at low temperature, the fractured surfaces were gold-sputtered and the dispersion state of the elastomer in the blend system was observed, as shown in Figure 1.
The four types of POE are as follows:
POE-1, with a melt flow rate of 0.5 g/10 min (190°C, 2.16 kg), is an ethylene-octene copolymer (EOR) produced by Dow Chemical (Shanghai) Co., Ltd.
POE-2, melt flow rate (190 ℃, 2.16 kg) is 1.2 g/(10 min), structure type EOR, Dow Chemical (Shanghai) Co., Ltd.
POE-3, melt flow rate (190℃, 2.16 kg) is 15 g/10 min, structure type EOR, Dow Chemical (Shanghai) Co., Ltd.
POE4, melt flow rate (190℃, 2.16 kg) is 1.2 (10 min), structural type is ethylene-butene copolymer (EBR), Dow Chemical (Shanghai) Co., Ltd.
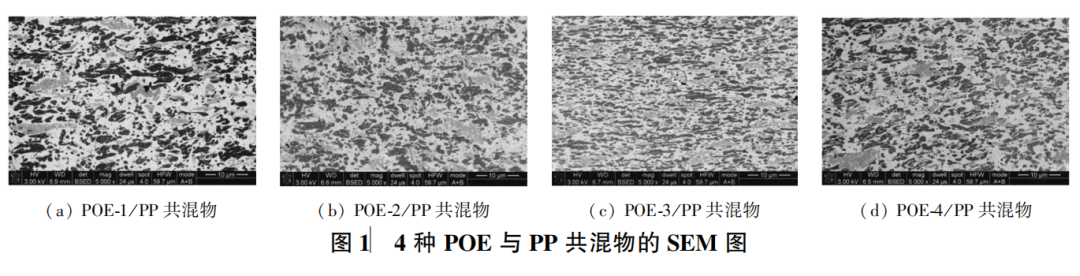
From Figures 1(a), (b), and (c), it can be observed that for the same EOR structure, the higher the melt index of POE, the smaller the particle size of the dispersed phase, and the better the dispersion effect.
From Figures 1 (b) and (d), it can be seen that the POE materials with the same melt index but different structures have similar dispersed phase particle sizes. This indicates that the main factor affecting the dispersed phase particle size of POE is its melt index, while the structural type is a secondary factor.
The effects of different POEs on the melt crystallization behavior and mechanical properties of modified PP are shown in Table 1.
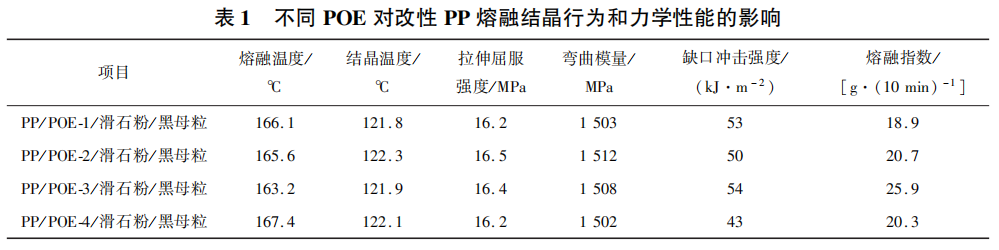
Among them, the mass ratio of PP: POE: talc powder: black masterbatch is 50:20:20:1.
The modified resin containing POE-2 with an EOR structure has a lower melting temperature and higher notched impact strength compared to POE-4 with an EBR structure. This is because POE-2 with an EOR structure has longer side chains, which more easily weaken the crystalline regions of the POE ethylene chains and the crystalline behavior of the PP resin, forming more elastic amorphous regions.
POE-3 containing EOR structure has a higher melt index, resulting in smaller dispersed phase particle size and better dispersion effect in modified resins. This can more effectively prevent the formation of PP spherulites, leading to a lower melting temperature of the modified resin while maintaining excellent toughness.
The reduction of the melting temperature of modified PP resin can lower the injection molding temperature, thereby indirectly reducing the cooling time; meanwhile, after modification with POE-3, the resin has a higher melt flow index, which is also beneficial for shortening the injection molding cycle.
Figures 2 and 3 show the injection molding flow length and shear viscosity of different POE-modified PP, respectively.
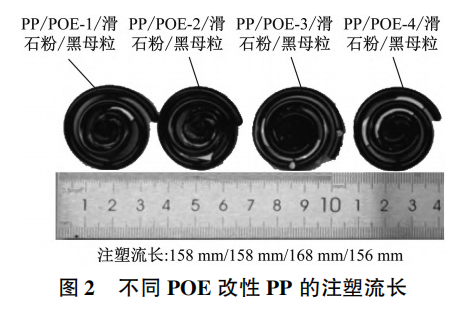
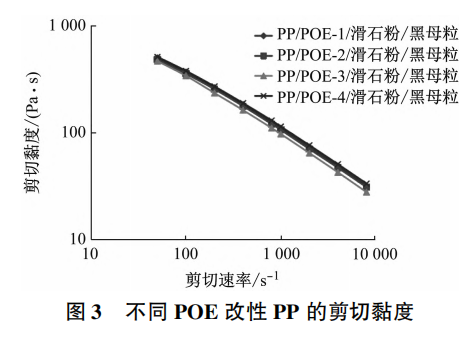
From Figure 2, it can be observed that the flow behavior of modified PP during the injection molding of bumpers is as follows: POE-3 modified PP has a higher melt flow index, and its injection flow length is also the longest (168mm).
From Figure 3, it can be observed that in the capillary rheological behavior, with the increase of shear rate, the shear viscosity of POE-3 modified PP is significantly lower than that of other POE modified PP. This indicates that POE-3 modified PP is more conducive to shortening the injection molding cycle of bumpers.
2. The impact of different additives
The effects of different additives on the melting crystallization behavior and mechanical properties of modified PP are shown in Table 2.
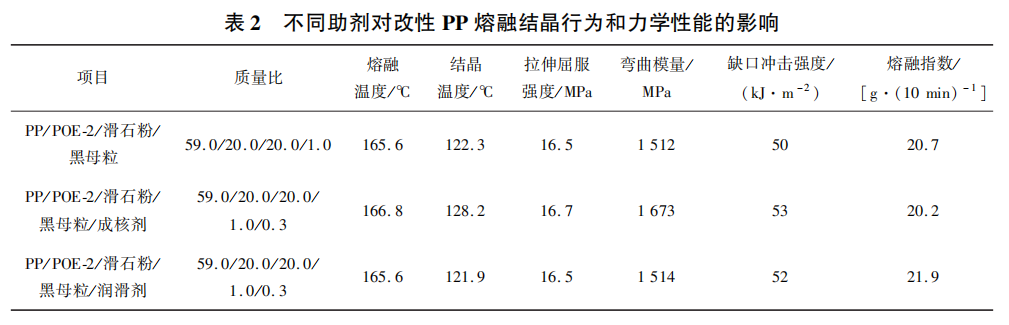
As shown in Table 2, the melting temperature and crystallization temperature of nucleating agent-modified PP are higher than those of other modified PPs. The presence of the nucleating agent promotes the formation of nuclei during the cooling and molding process of PP resin and improves the crystallization rate, resulting in a higher crystallization temperature. This is beneficial for shortening the cooling and molding cycle during injection molding.
In terms of mechanical properties, the flexural modulus of nucleating agent-modified PP is higher, and the notched impact strength of the toughness for the three modified PPs is also consistent. The melt index of lubricant-modified PP is relatively higher, which is beneficial for the injection molding process.
Figures 4 and 5 respectively show the injection molding flow length and shear viscosity of PP modified with different additives. From Figures 4 and 5, it can be seen that PP modified with a lubricant has a greater injection molding flow length (166mm) and slightly lower shear viscosity. This is because the lubricant zinc stearate acts as an external lubricant, which is more conducive to the lubrication between the molten PP resin and the die, thereby improving its flow behavior.

3. Fast-paced bumper made of modified PP material
The melting and crystallization behavior and mechanical properties of modified PP before and after optimization are shown in Table 3. The DSC curves of modified PP resin before and after optimization are shown in Figure 6.
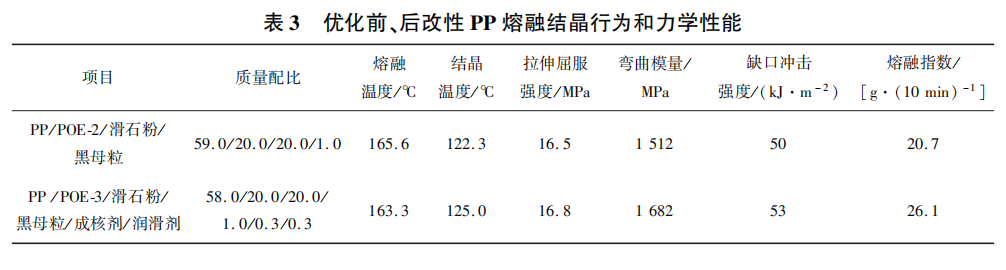
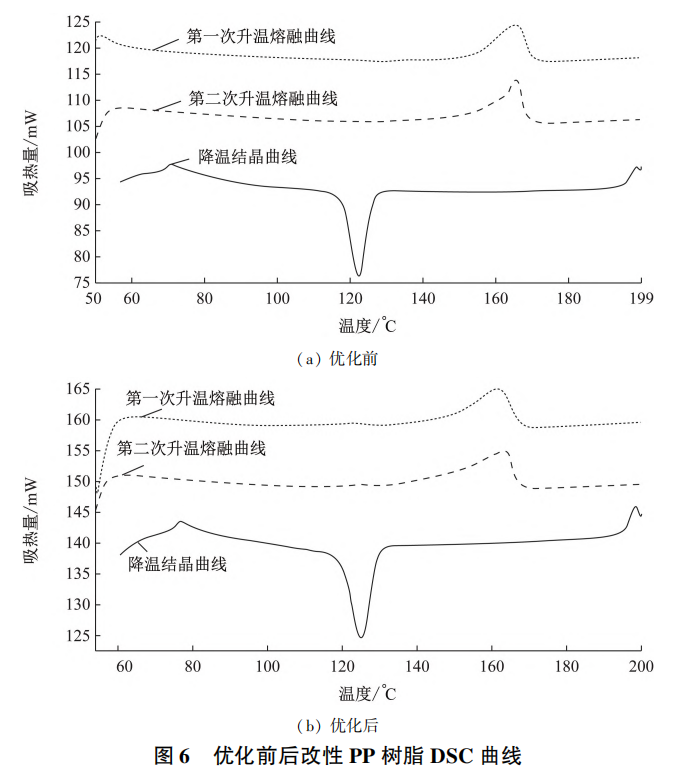
The optimization plan uses high melt flow index PP, high melt flow index POE-3, and lubricants to improve the material's flowability. The high melt flow index EOR structure POE can reduce the material's melting temperature, while the compounded nucleating agent can enhance its crystallization temperature and mechanical properties. The comprehensive performance of the modified PP material for bumpers is improved through multifaceted compounding.
The modified PP material after optimization has a lower melting temperature (163.3°C) while possessing a higher crystallization temperature (125.0°C). This is beneficial for shortening the material's plasticizing time during the injection molding process and can also increase the crystallization rate of the material, thereby reducing the holding and cooling time.
The injection flow length and shear viscosity of modified PP before and after optimization are shown in Figures 7 and 8, respectively.
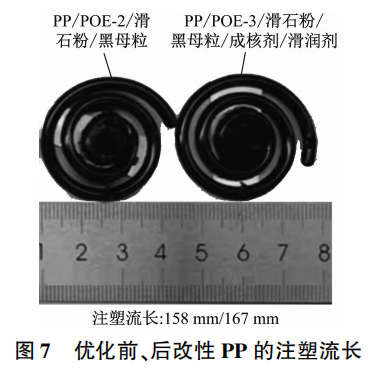
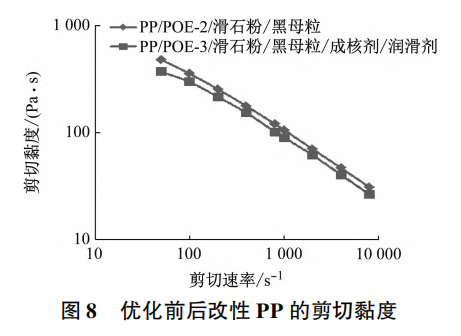
From Figures 7 and 8, it can be seen that the optimized modified PP has a greater injection molding flow length (167 mm) and a lower shear viscosity under the same shear rate conditions.
This is because the optimized scheme uses high melt index POE-3 to replace low melt index POE-2, improving the dispersion of the rubber phase in the resin, ensuring the toughness of the material, and enhancing the melt index to optimize its melt flow behavior. The compounding nucleating agent further improves the mechanical properties of the material and increases its crystallization temperature. Additionally, the addition of a lubricant further optimizes the melt flow behavior of the material.
Table 4 compares the process parameters of the original injection molding process 1 and the optimized injection molding process 2 for a sample with dimensions of 355mm x 100mm x 3.2mm.

According to Table 4, injection molding process 2 has a lower injection temperature, higher injection speed, and shorter holding and cooling times. The molding cycle of injection molding process 2 is 47 seconds, which is 13 seconds shorter than the original injection molding process 1.
Figure 9 shows the samples made from modified PP through Injection Molding Process 2 before and after optimization.
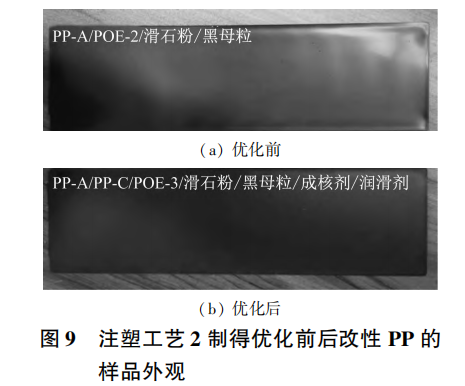
From Figure 9, it can be seen that under the conditions of Injection Molding Process 2, the modified PP injection-molded sample with optimized conditions exhibits a good appearance, whereas before optimization, the modified PP had a poor appearance with noticeable tiger stripe patterns and significant localized sink marks. This indicates that under the conditions of Injection Molding Process 2, using the optimized modified PP can effectively reduce the injection molding cycle while maintaining good appearance results, improving processing efficiency by 21.7% compared to the original injection molding process.
After the application of optimized modified PP aimed at shortening the injection molding cycle in the bumper project, the comparison of bumper injection molding process parameters before and after optimization is shown in Table 5.
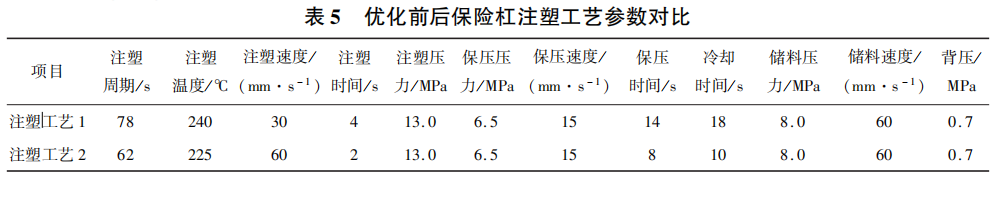
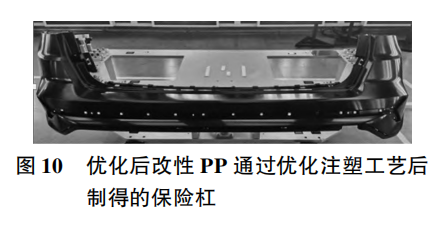
The bumper made from optimized modified PP through optimized injection molding process is shown in Figure 10. As can be seen from Table 5, the injection molding cycle of the bumper before optimization was 78 seconds. By using the optimized modified PP, the injection molding cycle can be shortened to 62 seconds, reducing the cycle by 16 seconds and improving processing efficiency by 20.51%. Its appearance is good, and the dimensions remain consistent with the original design.
Conclusion
The 1.EOR structure high melt index POE can improve the dispersion of the rubber phase in modified PP, ensure the toughness of the material, increase the melt index of the material, and reduce its melting temperature and shear viscosity.
Nucleating agents can optimize the mechanical properties of modified PP and increase its crystallization temperature. Lubricant additives can further improve the flow behavior of modified PP and increase its injection molding flow length.
To improve the flowability of materials, high melt flow index PP, high melt flow index POE, and lubricants are used. The EOR-structured high melt flow index POE can reduce the melting temperature of modified PP, while compounded nucleating agents can enhance its crystallization temperature and mechanical properties. By integrating multiple aspects, the comprehensive performance of modified PP materials for bumpers is enhanced, resulting in modified PP for bumpers that can shorten the injection molding cycle, with an increase of approximately 20% in injection molding efficiency.
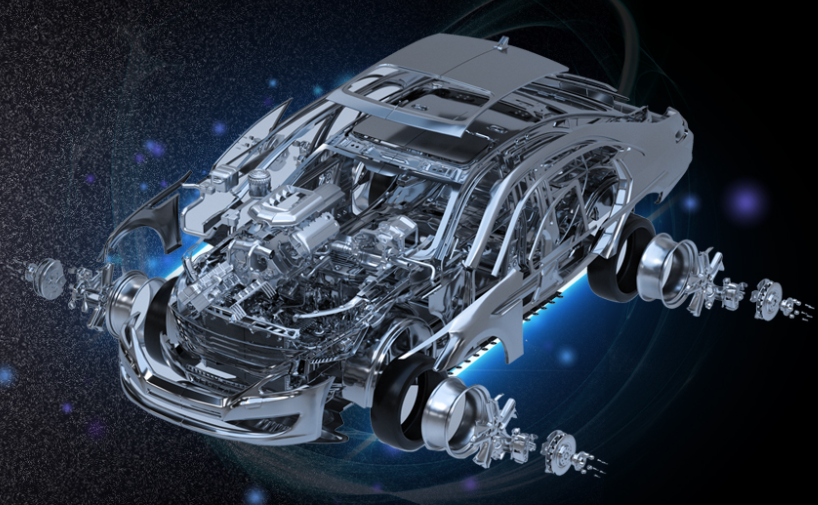
【Copyright and Disclaimer】The above information is collected and organized by PlastMatch. The copyright belongs to the original author. This article is reprinted for the purpose of providing more information, and it does not imply that PlastMatch endorses the views expressed in the article or guarantees its accuracy. If there are any errors in the source attribution or if your legitimate rights have been infringed, please contact us, and we will promptly correct or remove the content. If other media, websites, or individuals use the aforementioned content, they must clearly indicate the original source and origin of the work and assume legal responsibility on their own.
Most Popular
-
Covestro faces force majeure!
-
DuPont plans to sell Nomex and Kevlar brands for $2 billion! Covestro Declares Force Majeure on TDI / oTDA-based / Polyether Polyol; GAC Group Enters UK Market
-
Overseas Highlights: PPG Establishes New Aerospace Coatings Plant in the US, Yizumi Turkey Company Officially Opens! Pepsi Adjusts Plastic Packaging Goals
-
Tdi prices soar! an overview of global tdi capacity distribution and opportunities for chinese enterprises
-
Dongyue's 25% production capacity suspended: Capacity Contraction Meets Sudden Incident, Will the Silicone Market Experience the "Craziest" Trend?