How are bimetallic cylinders with embedded alloys manufactured? the impact of composition, manufacturing, surface treatment, and transportation on cylinder performance.
For plastic manufacturers, what is the cost of purchasing a bimetallic barrel? Additionally, what is its lifetime usage cost?
The lifespan of a machine barrel can be very short, depending on its manufacturing process, how it was handled before reaching the processor, and how the plastic processor uses it. Even seemingly minor defects on a new barrel can lead to premature wear of the barrel and screw, adversely affecting the quality of the final product, increasing the rejection rate, and even causing production stoppages. Due to these issues, purchasing barrels solely based on price may ultimately result in higher costs than other more expensive alternatives.
Next, let's take a look at the factors that may affect the true cost of the cartridge, starting with its basic components, and then considering potentially overlooked factors such as transportation and handling.
Inlay Combination
In most parts of the Americas and Europe, gun barrels are usually made of bimetal materials—that is, an alloy is lined or embedded on a base metal (or backing) to resist wear or corrosion. In Asia, integrated barrels are still quite common, but the production of bimetal barrels is also increasing to meet local use and export demands.
The process of producing bimetallic barrel liners is called centrifugal casting. This process uses heat to coat alloy powder onto the inner wall of a pre-drilled barrel, and then rotates the barrel to force the molten alloy powder to adhere tightly to the inner wall. The traditional heating method is to use a gas furnace, but many suppliers are now using induction furnaces, which have a shorter lining time, more stable barrel quality, and can produce extra-large barrels.
If special metallurgical techniques are not used, most manufacturers find it difficult to verify the quality of the cylinder linings. However, the composition, uniform thickness, and porosity of the linings are key factors determining the quality and lifespan of the cylinder. Their quality depends on the reliability and repeatability of the centrifugal casting process. The composition of the backing and linings should be supported by traceable metallurgical data records provided by the supplier.
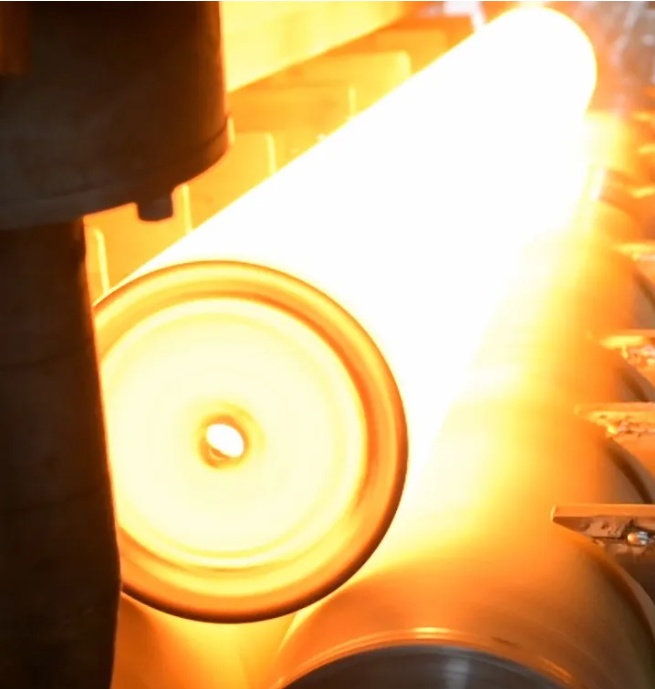
The centrifugal casting process is used to produce the inserts for bimetallic cylinders. This process utilizes heat to apply alloy powder to the interior of a pre-drilled cylinder, and then rotates the cylinder to force the molten alloy against the inner wall of the cylinder.
With the increasing use of highly abrasive fillers (especially glass fiber reinforced materials), embedded materials containing metal carbides have also emerged. These carbides (based on tungsten, titanium, or tantalum) are suspended in a matrix of nickel, cobalt, chromium, boron, or a combination of these corrosion-resistant materials, resulting in embedded products that are more corrosion-resistant than general-purpose cylinders. Note: Choosing the right screw material is crucial; certain hard-faced materials for screws used in combination with carbide-lined cylinders may lead to catastrophic wear.
For corrosive materials such as fluorinated compounds, another type of insert primarily composed of nickel, chromium, boron, and cobalt can be used, which provides chemical resistance but sacrifices some wear resistance. This insert should be used in conjunction with nickel-based substrates or a three-metal combination of nickel-based and carbon-based substrate steel.
The ideal thickness of the inlay is 1.6 millimeters or 0.063 inches. When the thickness exceeds this point, diminishing returns will occur.
Backing components
The control and repeatability of the centrifugal casting process not only affect the quality of the core but also impact the performance of the backing material, as the backing material is also annealed in a high-temperature rotating furnace and then slowly cooled. The quality of the backing is particularly important for the injection-molded barrel, as the pressure at the end of the injection stroke can reach 20,000 psi (138 MPa) or even higher, subjecting the entire plasticizing unit to tension. Poorly manufactured barrels may fracture, leading to damage to the screw, tip, end cap, and feed housing.
In order to cope with this pressure, the cylinder suppliers use high-pressure sleeves made of high-strength heat-treated alloy steel, which are fitted over the centrifugally cast cylinders. Alternatively, special alloy steel can be used to increase the pressure-bearing capacity by 50%, thereby eliminating the need for a sleeve and adopting a one-piece structure.
Transportation and handling
Even well-manufactured barrels may have flaws or damages during transportation. The more times the barrels are handled between the original manufacturer and the extrusion or molding workshop, the greater the likelihood of damage. These intermediate "handlers" may include truck drivers, shippers, dealers, and warehouses.
There is a risk of continuous vibration during maritime transport because the cylinder is placed on the ship's deck. The cylinder itself is made of steel and has significant internal stress; continuous vibration can release this stress, affecting the dimensions and straightness of the cylinder. In addition, due to the corrosive effects of seawater, maritime transport also faces special challenges. The cylinder should be properly protected with rust inhibitors and wrapped in film or paper to prevent corrosion. If the cylinder becomes severely rusted, it will be unusable.
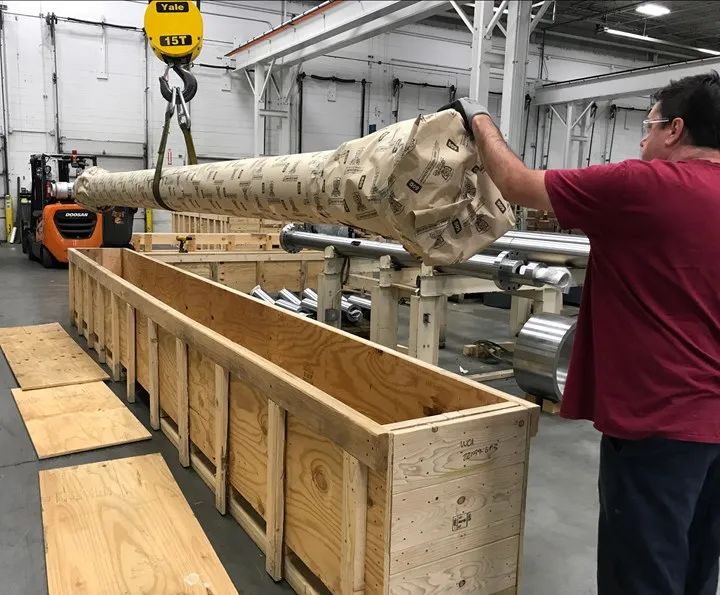
Unless properly supported in sturdy shipping packaging, the cylinder may move internally during transportation and handling, leading to damage.
Improper packaging or handling is another risk. Unless properly supported within sturdy shipping packaging, the drum may move during transportation and handling, causing damage. Even small drums can be heavy enough to damage poorly made shipping containers and may fall out during handling. Examples of potential damage include wear on concrete floors, scratches from forklifts, and cantilevering at lifting points when lifted with chain hoists.
Straightness and concentricity
After-the-fact correction of linearity deviations in new machine cylinders is very difficult, and the workshop's temporary solutions can only be said to do more harm than good. However, severe deviations can make it difficult to install the cylinder onto the machine, let alone screw it into the screw rod. Even seemingly insignificant deviations can adversely affect performance and the quality of the final product, and may even lead to catastrophic failures.
Consider the critical gap between the screw and the barrel. For an 80mm (3.15 inches) barrel, the gap on both sides of the screw needs to be maintained within the range of 0.076 to 0.102mm (0.003 to 0.004 inches). If this gap exceeds the tolerance range, the friction between the screw and the barrel can not only cause wear on both components but also generate metal particles, contaminating the final product—this is a serious issue in high-spec applications such as medical devices, cable coatings, and others.
The heat generated by friction can also affect the polymer, causing it to degrade and leading to wear, and in the worst case, it can result in the failure of the plasticizing system.
The longer the barrel, the wider the tolerance range for straightness. Since the inner and outer diameters of the barrel are usually out of alignment, it is difficult to determine its straightness in the extrusion or forming workshop without specialized equipment. Laser systems can provide the highest precision, but in most cases, processors need to seek qualified external services.
Surface treatment and process
The barrel should be smoothly polished, including the inner diameter, outer surface, and fastening areas. Aesthetics are not the key; a smooth and uniform surface is crucial for effective performance.
For example, the contact with the heating ring must be tight and uniform. Manual polishing to remove rust or defects that cause surface waves on the cylinder will hinder effective heat transfer.
Surface uniformity is also crucial for metal-to-metal seals, such as the flanges connecting the material cylinder and end cap or nozzle joints in injection molding, as well as the flanges connecting the machine barrel to the feed inlet and die head joints during extrusion. Surface irregularities can lead to polymer leakage and may cause metal corrosion, while poor surface quality of counterbores can also result in leaks. Repairing these issues requires disassembly and reprocessing, or it may be necessary to send the barrel back to the supplier for reworking.
Poor drilling quality also requires reprocessing, such as holes for installing components or thermocouples. The holes may not be drilled deep enough, or there may be burrs.
【Copyright and Disclaimer】The above information is collected and organized by PlastMatch. The copyright belongs to the original author. This article is reprinted for the purpose of providing more information, and it does not imply that PlastMatch endorses the views expressed in the article or guarantees its accuracy. If there are any errors in the source attribution or if your legitimate rights have been infringed, please contact us, and we will promptly correct or remove the content. If other media, websites, or individuals use the aforementioned content, they must clearly indicate the original source and origin of the work and assume legal responsibility on their own.
Most Popular
-
Covestro faces force majeure!
-
U.S. Proposes 50% Tariff on Indian Goods! Wood Group to Build Turkey's Largest Polypropylene Plant
-
Involving €11.9 Million! EU Launches Strict Investigation into Greece's Plastic Recycling Projects; Coperion and Brückner Deepen Cooperation
-
Metal Stamping Supplier Autokiniton to Close Detroit Plant and Lay Off Workers
-
DuPont to Spin Off Nomex and Kevlar Brands for $14.4 Billion: Is Aramid Fiber Still Attractive?