What are the polymerization processes for Nylon 66?
Nylon 66 (Nylon66) is one of the earliest developed, largest produced, and most widely used nylon products. It is a thermoplastic resin formed by the condensation polymerization of adipic acid and hexamethylenediamine, colorless and transparent, and is a polymorphic semi-crystalline polymer, with its molecular formula as shown in the figure.
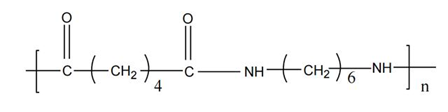
Molecular formula of Nylon 66
The density of Nylon 66 is 1.14g/cm³, and its melting point is around 265℃. Due to the presence of many polar amide bonds on its molecular chain, Nylon 66 easily absorbs water, forming hydrogen bonds within the main chain, which makes it very prone to orientation.
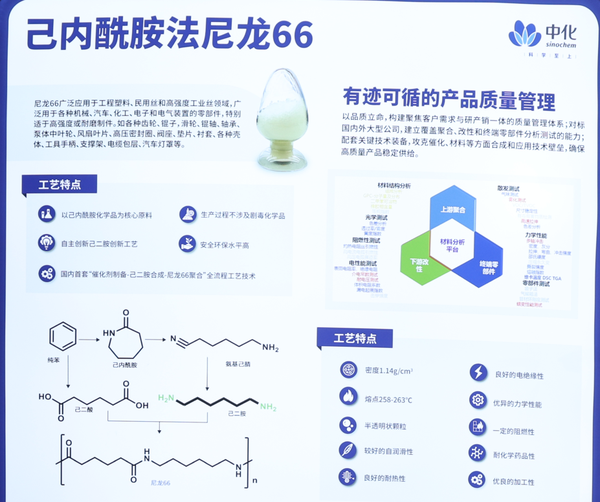
The condensation of nylons is a stepwise polymerization reaction, and the common polymerization methods usually include: melt polycondensation, solution polycondensation, solid-phase polycondensation, interfacial polycondensation, and anionic polymerization.
Melt Polycondensation
Melt polycondensation refers to a synthesis process where monomers undergo polymerization reactions in a molten state under certain temperatures and pressures, resulting in high polymers. Compared with methods such as solution polymerization, this method does not use solvents, thus having a higher concentration of reactants, faster reaction rates, less likelihood of introducing new impurities, leading to purer products that are easier to separate, without the need for additional purification processes.
Therefore, the quality and performance of the products produced are stable, and the operation process is simple, making it easy to achieve continuous production. In melt polycondensation, the condensation reaction occurs above the melting points of the monomers and the polymer, and after the reaction, the product remains in a molten state. The subsequent product can be directly spun into fibers, made into films, or pelletized, not only reducing energy consumption but also shortening the processing flow, improving production efficiency.
However, this method still has many drawbacks, such as the viscosity of the polymer increasing as the reaction progresses, worsening the fluidity of the product, and making heat transfer more difficult. This not only leads to serious sticking phenomena in the reactor, making it difficult to discharge the product, but also easily causes degradation or cross-linking of the product, affecting the
Nylon 66 (Nylon66) is one of the earliest developed, largest produced, and most widely used nylon products. It is a thermoplastic resin formed by the condensation polymerization of adipic acid and hexamethylenediamine, colorless and transparent, being a semi-crystalline polymer with multiple crystal forms, as shown in the molecular formula below.
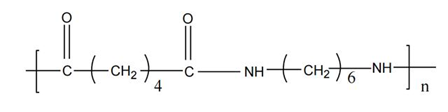
Molecular formula of Nylon 66
The density of Nylon 66 is 1.14g/cm³, and its melting point is around 265°C. Due to the presence of numerous polar amide bonds on its molecular chain, Nylon 66 easily absorbs water, forming hydrogen bonds within the main chain, which makes it very prone to orientation.
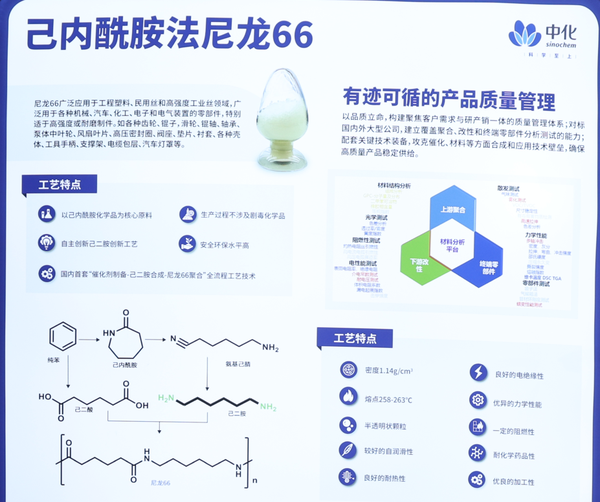
The condensation of nylons is a stepwise polymerization reaction, and the common methods for its polymerization process usually include: melt condensation, solution condensation, solid-phase condensation, interfacial condensation, and anionic polymerization.
Melt Condensation Method
The melt condensation method refers to a synthetic process where monomers undergo polymerization reactions in a molten state under certain temperature and pressure conditions. Compared to methods such as solution polymerization, this method does not use solvents, thus the reactant concentration is high, the reaction rate is fast, and it's less likely to introduce new impurities, making the product purer, easier to separate, and without the need for additional purification processes.
Therefore, the quality and performance of the products produced are stable, and the operation process is simple, facilitating continuous production. In the melt condensation method, the condensation reaction occurs above the melting points of both the monomer and the polymer, and after the reaction, the product remains in a molten state. The subsequent product can be directly spun, formed into films, or pelletized, not only reducing energy consumption but also shortening the processing flow, thereby improving production efficiency.
However, this method still has many drawbacks, such as the viscosity of the polymer increasing as the reaction progresses, leading to poorer fluidity of the product and more difficult heat transfer. This not only results in severe sticking to the reactor, making it hard to discharge the product, but also easily causes degradation or cross-linking of the product, affecting the quality of the product.
Nylon 66 (Nylon66) is one of the earliest developed, largest produced, and most widely used nylon products. It is a thermoplastic resin synthesized by the condensation of adipic acid and hexamethylenediamine, colorless and transparent, being a polycrystalline semi-crystalline polymer, with its molecular formula as shown in the figure.
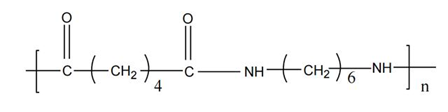
Molecular formula of Nylon 66
The density of Nylon 66 is 1.14g/cm³, and its melting point is around 265°C. Due to the presence of numerous polar amide bonds on its molecular chain, Nylon 66 readily absorbs water, forming hydrogen bonds within the main chain, making it very prone to orientation.
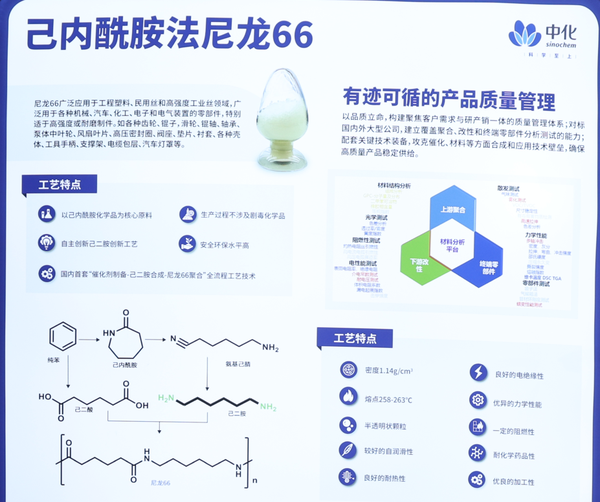
The condensation of nylon is a stepwise polymerization reaction, and its polymerization process methods typically include: melt condensation, solution condensation, solid-phase condensation, interfacial condensation, and anionic polymerization.
Melt Condensation
Melt condensation refers to a synthetic process where monomers undergo a polymerization reaction in a molten state under certain temperatures and pressures, producing high polymers. Compared to solution polymerization and other methods, this method does not use solvents, thus resulting in higher reactant concentrations, faster reaction rates, less introduction of new impurities, purer products, easier separation, and no need for additional product purification processes.
Therefore, the quality and performance of the products are stable, and the operational procedures are simple, making it easy to achieve continuous production. In melt condensation, the condensation reaction occurs above the melting points of the monomer and the polymer, and after the reaction is completed, the product remains in a molten state. Subsequently, the product can be directly spun into fibers, made into films, or pelletized, which not only reduces energy consumption but also shortens the processing steps, improving production efficiency.
However, this method still has many drawbacks. As the reaction progresses, the viscosity of the polymer increases, leading to poorer flowability of the product, more difficult heat transfer, not only causing severe sticking in the reactor, making it difficult to discharge the product, but also easily leading to degradation or cross-linking of the product, affecting the quality of the product.
Because the melt condensation reaction
Nylon 66 (Nylon66) is one of the earliest developed, largest produced, and most widely used nylon products. It is a thermoplastic resin formed by the condensation polymerization of adipic acid and hexamethylenediamine, colorless and transparent, and is a semi-crystalline polymer with multiple crystal forms, as shown in the molecular formula below.
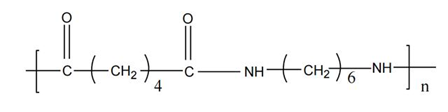
Molecular formula of Nylon 66
The density of Nylon 66 is 1.14g/cm³, with a melting point around 265℃. Due to the presence of numerous polar amide bonds on its molecular chain, Nylon 66 easily absorbs water, forming hydrogen bonds within the main chain, making it very prone to orientation.
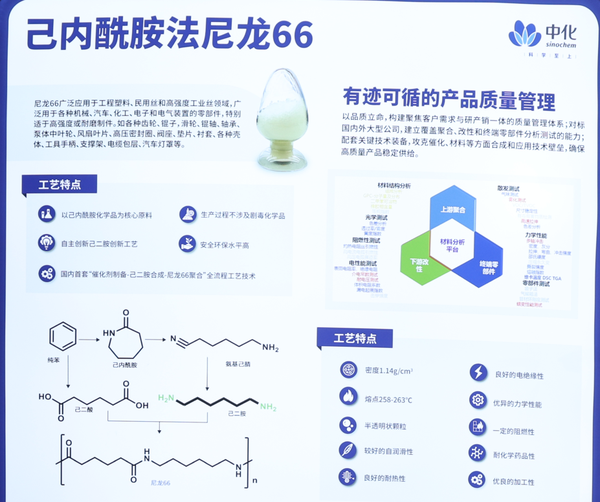
The condensation of nylon is a stepwise polymerization reaction, and its polymerization process methods usually include: melt condensation, solution condensation, solid-phase condensation, interfacial condensation, and anionic polymerization.
Melt Condensation
Melt condensation refers to the synthesis process where monomers undergo a polymerization reaction in a molten state under certain temperatures and pressures, producing high polymers. Compared to methods such as solution polymerization, this method does not use solvents, thus the concentration of reactants is high, the reaction rate is fast, and it is less likely to introduce new impurities, resulting in purer products that are easier to separate, without the need for additional purification processes.
Therefore, the quality and performance of the products produced are stable, and the operation process is simple, making it easy to achieve continuous production. In melt condensation, the condensation reaction occurs above the melting points of the monomer and polymer, and after the reaction, the product remains in a molten state. The subsequent product can be directly processed into fibers, films, or pellets, which not only reduces energy consumption but also shortens the processing flow, improving production efficiency.
However, this method still has many drawbacks. As the reaction proceeds, the viscosity of the polymer increases, the fluidity of the product decreases, and heat transfer becomes more difficult. This not only leads to severe sticking to the reactor, making it hard to discharge the product, but also can cause the product to decompose or crosslink, affecting the quality of the product.
Since the temperature of the melt condensation reaction is above the melting point of both the monomer and the product
Nylon 66 (Nylon66) is one of the earliest developed, highest produced, and most widely used nylon products. It is a thermoplastic resin formed by the condensation of adipic acid and hexamethylenediamine, colorless and transparent, and is a polycrystalline semi-crystalline polymer, with its molecular formula as shown in the figure.
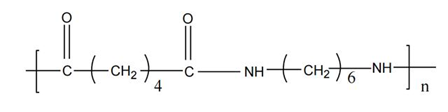
Molecular formula of Nylon 66
The density of Nylon 66 is 1.14g/cm³, with a melting point around 265°C. Due to the presence of numerous polar amide bonds on its molecular chain, Nylon 66 readily absorbs water, forming hydrogen bonds within the main chain, making it very susceptible to orientation.
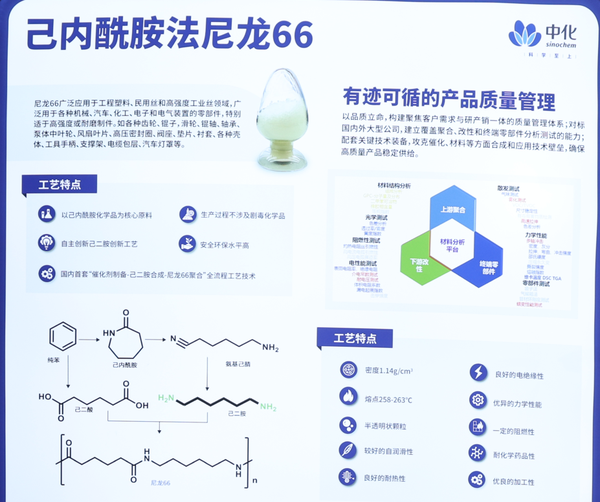
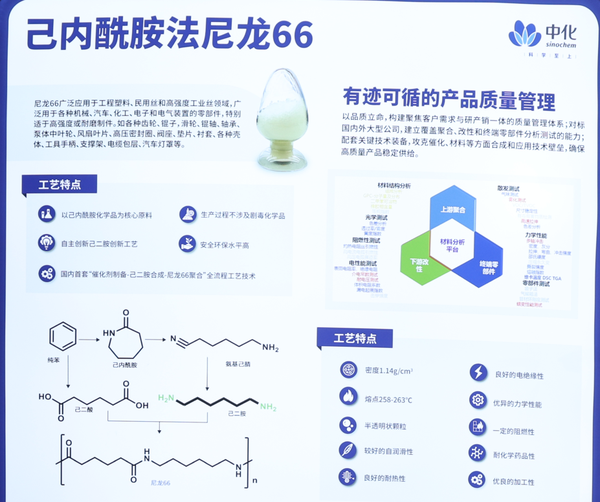
The condensation of nylon is a stepwise polymerization reaction, and its polymerization methods usually include the following: melt polycondensation, solution polycondensation, solid-phase polycondensation, interfacial polycondensation, and anionic polymerization.
Melt Polycondensation
Melt polycondensation refers to the synthesis process where monomers undergo polymerization reactions in a molten state under certain temperatures and pressures, forming polymers. Compared with methods like solution polymerization, this method does not use solvents, resulting in high reactant concentrations, fast reaction rates, and less introduction of new impurities, making the product purer and easier to separate, without requiring additional purification processes for the product.
Therefore, the quality and performance of the produced products are stable, and the operation process is simple, facilitating continuous production. In melt polycondensation, the condensation reaction occurs above the melting points of the monomers and the polymer. After the reaction is completed, the product remains in a molten state. The subsequent product can be directly spun, formed into films, or pelletized, which not only reduces energy consumption but also shortens the processing flow, improving production efficiency.
However, this method still has many drawbacks. As the reaction progresses, the viscosity of the polymer increases, leading to poorer fluidity of the product and more difficult heat transfer. This not only results in severe sticking to the reactor, making it difficult to discharge the product, but also easily causes degradation or cross-linking of the product, affecting the product quality.
Since the temperature of the melt polycondensation reaction is above the melting points of both the monomer and the product, it is necessary to strictly control the process conditions to prevent side reactions such as thermal decomposition of nylon.
In condensation polymerization, the ratio of monomers has a significant impact on the relative molecular weight of the product. A suitable ratio of monomers promotes the forward reaction, resulting in a higher relative molecular weight of the product.
If the reaction temperature is too high, diamines are prone to volatilize, and dicarboxylic acids are likely to undergo side reactions such as decarboxylation, leading to an imbalance in end groups and a decrease in the molecular weight of the product. To avoid this situation, a slight excess of diamine should be added first to prevent the imbalance in the monomer ratio due to the volatilization of diamines, while keeping the reaction system under a certain pressure to reduce the volatilization of diamines.
Alternatively, prepolymers can be generated at lower temperatures first, followed by further reactions to increase the relative molecular weight. In the later stages of condensation polymerization, the content of small molecule water is key to further increasing the degree of reaction. Therefore, in the later stages of the reaction, it is necessary to remove small molecule water through vacuum extraction to achieve further growth in molecular weight.
Solution polycondensation
Solution polycondensation refers to the method where monomers undergo condensation polymerization in an inert solvent. When the monomers do not melt or decompose easily, solution polycondensation is generally used. During the reaction process, the solvent plays roles in stabilizing the reaction conditions and conducting heat. Compared with melt polycondensation, solution polycondensation has fewer side reactions, a more uniform reaction system, convenient mass and heat transfer, and easier temperature control. In industry, solution polycondensation is mainly used for the production of certain types of nylons and some heat-resistant aromatic heterocyclic polymers, such as polyurethanes, polysulfones, and polyimides, etc.
Solution polymerization methods are generally divided into low-temperature solution polycondensation and high-temperature solution polycondensation. The reaction system from low-temperature solution polycondensation can be directly used for spinning after simple treatment, simplifying the production process and improving production efficiency. This method is commonly used in the synthesis process of meta-aromatic nylons.
High-temperature solution polycondensation generally involves dissolving dicarboxylic acid and diamine in a suitable solvent to first form a prepolymer. The temperature is then increased for further reaction, while removing small molecule water from the system to promote the forward reaction, increasing the relative molecular mass of the prepolymer, and ultimately obtaining the target product. Companies such as Amoco in the United States and DSM in the Netherlands use high-temperature solution polycondensation to synthesize semi-aromatic and aromatic nylons.
Solid-phase polycondensation
Nylon has been used in various fields, with its application domain determined by its relative molecular mass. The higher the molecular weight, the better the overall performance of nylon.
When the molecular weight of nylon is between 10,000 and 20,000, it exhibits typical fiber properties. When the molecular weight reaches 30,000, nylon can be used as an engineering plastic.
However, traditional polycondensation methods see a rapid increase in system viscosity during the later stages of the reaction, making stirring difficult, hindering timely heat and mass transfer, and easily leading to localized overheating, causing issues like oxidation degradation and yellowing of the product. Therefore, new methods are needed to improve the relative molecular mass of nylon. Currently, solid-phase polycondensation is a commonly used method.
In the 1930s, American scientist Flory discovered the solid-phase polycondensation reaction. He found that when low-molecular-weight nylon products were reheated to a certain temperature, the nylon would continue to undergo chain growth reactions, further increasing the molecular weight. Since both the raw materials and products are solids during the reaction, it is called a solid-phase polycondensation reaction.
This reaction occurs under an inert atmosphere, with the raw material being within the temperature range above the glass transition temperature (Tg) and below the melting point (Tm). To avoid a series of problems caused by excessive melt viscosity during melt polycondensation, the product obtained from the reaction is usually controlled at a lower viscosity, which is then increased through solid-phase polycondensation.
Interfacial polycondensation
Interfacial polycondensation was first discovered by Morgan and others, referring to a method where two monomers undergo polycondensation at the interface between two immiscible solvents. The monomers for interfacial polycondensation require high reactivity, allowing polycondensation to occur at room temperature, with advantages such as fast reaction rate, low requirements for the purity of the reacting monomers and molar ratio, high molecular weight of the product, simple equipment, and fewer side reactions.
Interfacial polycondensation was first discovered by Morgan and others, referring to a method where two monomers undergo polycondensation at the interface between two immiscible solvents. The monomers for interfacial polycondensation require high reactivity, allowing polycondensation to occur at room temperature, with advantages such as fast reaction rate, low requirements for the purity of the reacting monomers and molar ratio, high molecular weight of the product, simple equipment, and fewer side reactions.
Nylon is formed by dissolving multifunctional acyl chlorides and multifunctional amides in two solvents through interfacial polycondensation, during which a side reaction occurs producing hydrogen chloride (HCl). To prevent HCl from reacting with amines and affecting the reaction process, an appropriate amount of basic substance needs to be added for neutralization. However, excess base can lead to hydrolysis of the diacyl chlorides. Due to the high cost, toxicity, and tendency to cause pollution of acyl chlorides and organic solvents, as well as the complexity of subsequent recovery processes, industrialization is difficult.
Nylon is formed by dissolving multifunctional acyl chlorides and multifunctional amides in two solvents through interfacial polycondensation, during which a side reaction occurs producing hydrogen chloride (HCl). To prevent HCl from reacting with amines and affecting the reaction process, an appropriate amount of basic substance needs to be added for neutralization. However, excess base can lead to hydrolysis of the diacyl chlorides. Due to the high cost, toxicity, and tendency to cause pollution of acyl chlorides and organic solvents, as well as the complexity of subsequent recovery processes, industrialization is difficult.
Anionic polymerization
Anionic polymerization
Anionic polymerization is a method where, under the action of a catalyst and activator, monomers go through chain initiation, activation reaction, and chain growth to ultimately produce high molecular weight nylon products. Compared to other polycondensation methods, this method synthesizes nylon products with relatively higher molecular weight, density, and crystallinity.
Anionic polymerization is a method where, under the action of a catalyst and activator, monomers go through chain initiation, activation reaction, and chain growth to ultimately produce high molecular weight nylon products. Compared to other polycondensation methods, this method synthesizes nylon products with relatively higher molecular weight, density, and crystallinity.
To leverage the strengths and weaknesses of different polymerization methods, several methods are usually combined to synthesize nylon. A common approach is solution-melt polycondensation. First, monomers are dissolved in a solvent at a lower temperature to undergo prepolymerization, generating oligomers. This process effectively prevents the volatilization and loss of diamines during the subsequent temperature increase for polycondensation, avoiding imbalance in the monomer ratio. Then, the temperature is gradually increased above the melting point of nylon, while removing the solvent and water from the system, initiating melt polycondensation. After some time, vacuum extraction is used to further increase the molecular weight of nylon. Additionally, the product after melt polycondensation can still be subjected to solid-phase polycondensation to further enhance its molecular weight, resulting in high viscosity, high-quality nylon.
To leverage the strengths and weaknesses of different polymerization methods, several methods are usually combined to synthesize nylon. A common approach is solution-melt polycondensation. First, monomers are dissolved in a solvent at a lower temperature to undergo prepolymerization, generating oligomers. This process effectively prevents the volatilization and loss of diamines during the subsequent temperature increase for polycondensation, avoiding imbalance in the monomer ratio. Then, the temperature is gradually increased above the melting point of nylon, while removing the solvent and water from the system, initiating melt polycondensation. After some time, vacuum extraction is used to further increase the molecular weight of nylon. Additionally, the product after melt polycondensation can still be subjected to solid-phase polycondensation to further enhance its molecular weight, resulting in high viscosity, high-quality nylon.
The commonly used nylon 66 production processes in industry are mainly divided into two types: batch polycondensation and continuous polycondensation. The laboratory method mainly adopts the batch polycondensation.
The commonly used nylon 66 production processes in industry are mainly divided into two types: batch polycondensation and continuous polycondensation. The laboratory method mainly adopts the batch polycondensation.Batch Polycondensation
Batch PolycondensationThe specific implementation steps of the batch polycondensation method are shown in the figure below.
The specific implementation steps of the batch polycondensation method are shown in the figure below.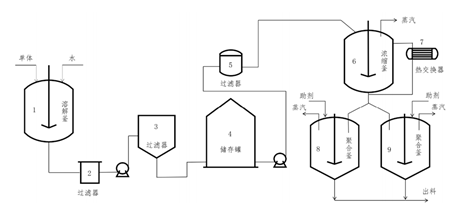
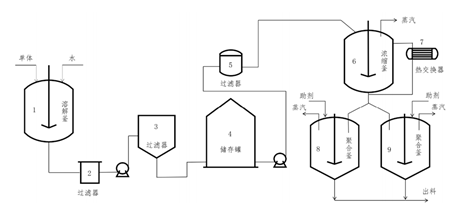
Nylon 66 Batch Polycondensation Process Flow Chart
Nylon 66 Batch Polycondensation Process Flow ChartFirst, dissolve the nylon salt to make a nylon salt solution. Then, according to the requirement, transfer the required amount of nylon salt solution into the concentrator, where the 50wt% salt solution is concentrated to 80wt%. Subsequently, the concentrated salt solution is transferred into the polymerization reactor. First, the temperature of the reactor is raised to near the melting point of the nylon salt for pre-polycondensation reaction. After reacting for some time, it enters the pressure reduction stage, during which the temperature inside the reactor is increased to near the melting point of nylon, while water vapor inside the reactor is expelled. The pressure inside the reactor is slowly reduced to atmospheric pressure in several stages. After reacting for a certain period, it enters the final completion stage. The viscosity of the nylon 66 product can be adjusted by controlling the vacuum level and vacuum extraction time during the completion stage. Finally, the product is extruded, pelletized, and sliced. After drying, it can be used for products such as plastics, films, and industrial filaments.
First, dissolve the nylon salt to make a nylon salt solution. Then, according to the requirement, transfer the required amount of nylon salt solution into the concentrator, where the 50wt% salt solution is concentrated to 80wt%. Subsequently, the concentrated salt solution is transferred into the polymerization reactor. First, the temperature of the reactor is raised to near the melting point of the nylon salt for pre-polycondensation reaction. After reacting for some time, it enters the pressure reduction stage, during which the temperature inside the reactor is increased to near the melting point of nylon, while water vapor inside the reactor is expelled. The pressure inside the reactor is slowly reduced to atmospheric pressure in several stages. After reacting for a certain period, it enters the final completion stage. The viscosity of the nylon 66 product can be adjusted by controlling the vacuum level and vacuum extraction time during the completion stage. Finally, the product is extruded, pelletized, and sliced. After drying, it can be used for products such as plastics, films, and industrial filaments.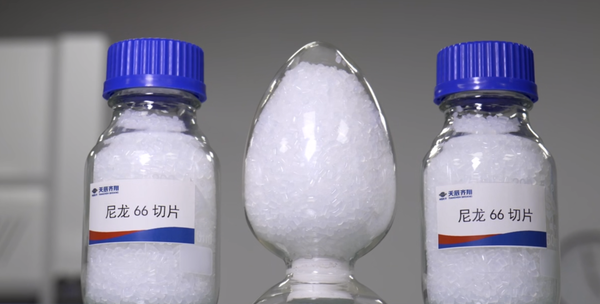
Image source: Tianchen Qixiang
Image source: Tianchen QixiangContinuous polycondensation method
Continuous polycondensation methodThe specific implementation steps of the continuous polycondensation method are shown in the figure.
The specific implementation steps of the continuous polycondensation method are shown in the figure.
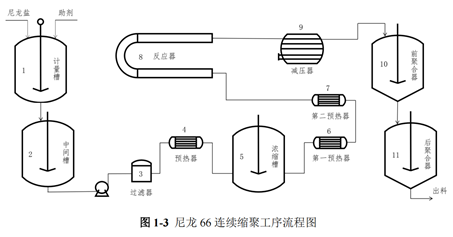
First, 50wt% of the nylon 66 salt solution from the salt storage tank is batched into the metering tank according to the requirement. In the metering tank, the required additives are added based on different product requirements. The uniformly mixed nylon 66 salt solution is then batched into an intermediate tank. It is subsequently pumped through a filter and preheater into a concentrator, where the temperature is raised to concentrate the nylon 66 salt to 70% wt%. After passing through the first and second preheaters, it enters the reactor for pre-polycondensation.
First, the 50wt% nylon 66 salt solution in the salt storage tank is batch-fed into the metering tank according to requirements. In the metering tank, the required additives are added based on different product specifications. The uniformly mixed nylon 66 salt solution is then batch-fed into an intermediate tank. Subsequently, the nylon 66 salt solution is pumped through a filter and preheater into a concentrator, where the temperature is increased to concentrate the nylon 66 salt to 70%wt%. After passing through the first and second preheaters, it enters the reactor for prepolymerization.The resulting prepolymer is transferred to a depressurizer, where the pressure is gradually reduced to atmospheric pressure, promoting the rapid removal of water from the prepolymer. The prepolymer coming out of the depressurizer enters the preliminary polymerizer for further dehydration, facilitating the forward progress of the polymerization reaction. Finally, it enters the final polymerizer, where vacuum is applied to further increase the viscosity of the polymer. When the viscosity of the product meets the requirements, it is extruded and can subsequently be directly pelletized or spun.
The resulting prepolymer is transferred to a depressurizer, where the pressure is gradually reduced to atmospheric pressure, promoting the rapid removal of water from the prepolymers. The prepolymer coming out of the depressurizer enters the preliminary polymerizer for further dehydration, facilitating the forward progress of the polymerization reaction. Finally, it enters the final polymerizer, where vacuum is applied to further increase the viscosity of the polymer. When the viscosity of the product meets the requirements, it is extruded and can subsequently be directly pelletized or spun.Nylon 66 is one of the earliest products to achieve industrialization and is also the most widely used type of nylon. Nylon 66 has many advantages such as high mechanical strength, good toughness, good heat resistance, good wear resistance, good corrosion resistance, and low density, specifically as follows:
Nylon 66 is one of the earliest products to achieve industrialization and is also the most widely used type of nylon. Nylon 66 has many advantages such as high mechanical strength, good toughness, good heat resistance, good wear resistance, good corrosion resistance, and low density, specifically as follows:Nylon 66, as an engineering plastic, has excellent properties such as good mechanical performance, oil resistance, wear resistance, and self-lubrication, and is commonly used in automobiles, electrical and electronic equipment, and packaging materials. Additionally, as a high-performance fiber material, nylon 66 is widely used in airbags, tire cord, clothing, and parachutes, among other applications.
Nylon 66, as an engineering plastic, possesses excellent mechanical properties, oil resistance, wear resistance, and self-lubrication, and is commonly used in automobiles, electronics, electrical appliances, and packaging materials. Additionally, as a high-performance fiber material, Nylon 66 is widely applied in areas such as airbags, tire cord fabrics, clothing, and parachutes.References: Study on the Synthesis of Nylon 66 and Nylon MXD6 and Key Influencing Factors, Liu Yue
参考资料:尼龙 66 及尼龙 MXD6 的合成及关键影响因素研究,刘悦 请注意,在最后的“参考资料”部分,您似乎希望保留原文未翻译。根据您的指示,这部分保持了中文形式。如果有任何进一步的调整需求,请告诉我!【Copyright and Disclaimer】The above information is collected and organized by PlastMatch. The copyright belongs to the original author. This article is reprinted for the purpose of providing more information, and it does not imply that PlastMatch endorses the views expressed in the article or guarantees its accuracy. If there are any errors in the source attribution or if your legitimate rights have been infringed, please contact us, and we will promptly correct or remove the content. If other media, websites, or individuals use the aforementioned content, they must clearly indicate the original source and origin of the work and assume legal responsibility on their own.
Most Popular
-
Covestro faces force majeure!
-
Breaking News! Mitsui Chemicals TDI Unit in Japan Experiences Chlorine Gas Leak Accident!
-
Mitsubishi Chemical Exits! Sumitomo Acquires!
-
DuPont plans to sell Nomex and Kevlar brands for $2 billion! Covestro Declares Force Majeure on TDI / oTDA-based / Polyether Polyol; GAC Group Enters UK Market
-
Borealis suspends polyolefin recycling plant in Austria, Hyundai achieves record Q2 revenue, Volkswagen lowers performance expectations