Wearable Medical New Era: How Ultrasonic Technology Achieves 0.05mm Precision Welding
In the medical device manufacturing industry, sterilization and precision are core requirements. The ultrasonic welding technology based on non-touch processing, cleanroom compatibility and non-particle contamination properties make it an ideal choice for manufacturing critical products such as medical tubing, filters, and masks.
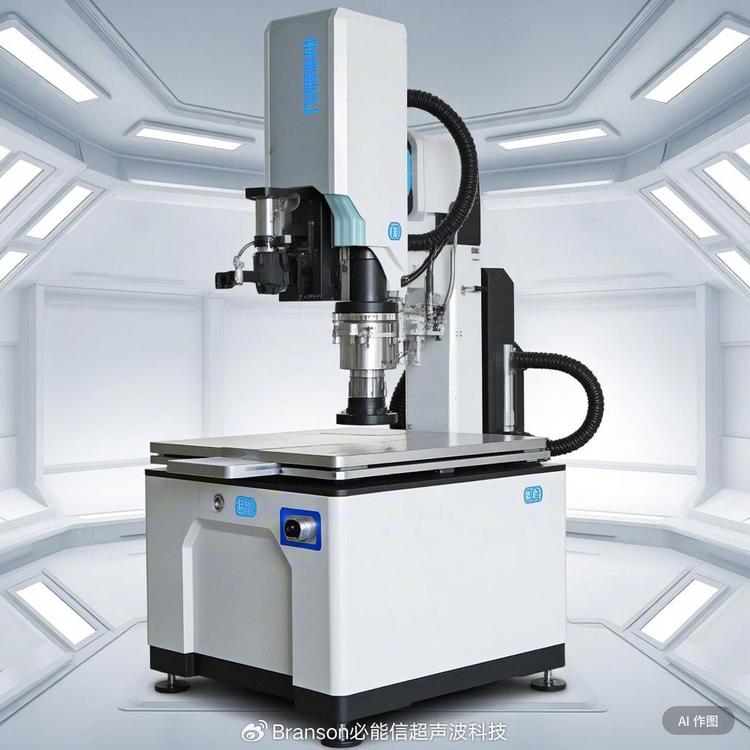
Core Application Areas
Medical Catheters and Interventional DevicesThe Binexin ultrasonic welding machine achieves molecular-level fusion of thermoplastic materials through high-frequency vibrations (15-40kHz), making it suitable for applications such as catheter interface sealing and multi-chamber tube composite welding. Its precise energy control (with selectable modes for time, power, distance, etc.) prevents material overheating and degradation, ensuring a smooth, burr-free inner wall of the catheter, thus meeting the biocompatibility requirements for blood-contacting devices. For example, precision welding of blood transfusion needles and threaded openings of flexible containers has widely adopted this technology.
Medical filters and separation devicesFor critical components such as filter end caps and biofilters, Branson equipment utilizes dynamic triggering and amplitude step control to achieve leak-free sealing of medical-grade polymers like PP and PES. Furthermore, laboratory-grade ultrasonic sonochemical equipment can promote uniform filter membrane structure, enhancing filtration efficiency.
Production of Masks and Protective EquipmentIn N95 mask and surgical mask earband welding, ultrasonic technology can complete non-woven layering and cutting in 0.1-0.5 seconds without the need for adhesives or heat sources, avoiding chemical residues. An all-automatic earband mask machine integrates this technology, with a single machine daily output capacity exceeding 100,000 pieces, and weld strength nearly matching the original material properties.
II. Cleanroom Compatibility and Contamination Control
No additive weldingUltrasonic welding technology melts materials directly through friction, eliminating the need for adhesives, solvents, or other contaminants, and meets the ISO 13485 standard for medical device manufacturing.
Low-Particle Release DesignThe equipment uses a closed vibration system with a titanium alloy horn, producing no metal debris during operation; digital amplitude control (±2% accuracy) reduces material carbonization caused by energy overload, lowering the risk of micro particles.
Clean Room AdaptabilityThe E-Plus series and other compact devices of the Capable Clean series support Class 100-1000 clean environments, with pneumatic systems featuring HEPA filter interfaces to avoid oil mist contamination. The dynamic tracking function can maintain the welding nozzle pressure stable in real time, preventing vibration-induced air disturbances.
III. Technological Upgrade and Quality Control
- Supervisory Monitoring SystemFeaturing peak power detection, automatic frequency tracking (±10% voltage fluctuation compensation), and color chart printing for full traceability of welding parameters.
· Security protection mechanisms Five-level generator protection (temperature/current/power abnormalities, etc.) and password permission management to ensure the process stability of key medical production lines.
· Material compatibility expansion Supports welding of medical plastics such as PP, PC, and PETG, as well as high-performance engineering plastics like PEEK, meeting the requirements of complex medical devices.
Conclusion
Advanced ultrasonic welding technology, with its precise energy control, cleanroom optimization design and zero-pollution process, provides a complete solution chain from laboratory to mass production for the medical industry. As the trend of miniaturization and functional integration of medical devices deepens, this technology will continue to drive innovation breakthroughs in areas such as catheter interventional devices and wearable medical equipment.
【Copyright and Disclaimer】The above information is collected and organized by PlastMatch. The copyright belongs to the original author. This article is reprinted for the purpose of providing more information, and it does not imply that PlastMatch endorses the views expressed in the article or guarantees its accuracy. If there are any errors in the source attribution or if your legitimate rights have been infringed, please contact us, and we will promptly correct or remove the content. If other media, websites, or individuals use the aforementioned content, they must clearly indicate the original source and origin of the work and assume legal responsibility on their own.
Most Popular
-
Covestro faces force majeure!
-
Breaking News! Mitsui Chemicals TDI Unit in Japan Experiences Chlorine Gas Leak Accident!
-
DuPont plans to sell Nomex and Kevlar brands for $2 billion! Covestro Declares Force Majeure on TDI / oTDA-based / Polyether Polyol; GAC Group Enters UK Market
-
Mitsubishi Chemical Exits! Sumitomo Acquires!
-
Borealis suspends polyolefin recycling plant in Austria, Hyundai achieves record Q2 revenue, Volkswagen lowers performance expectations