Trends in the Development of New Aviation Materials
Following the previous introduction of new materials in the C919 large aircraft, this article will continue to unveil the cutting-edge development trends of new materials, including advanced alloy materials, shape memory alloys, high-performance composite materials, thermoplastic composites, advanced smart materials, integrated structures materials, and additive manufacturing technology. As these technologies continue to mature, they are expected to play an even more critical role in the future of the aviation industry, ushering in a new era of flight.
Advanced new alloy materials
On the basis of traditional aerospace aluminum alloys, developing advanced new alloy materials with superior performance through composition and process modifications can effectively achieve weight reduction in aircraft structures.
Representative陶铝 new materials are based on aluminum alloy substrates, in which nanoceramic particle reinforcement phases are generated in situ to achieve an optimized combination of the plasticity and toughness of the aluminum alloy substrate with the high strength and high modulus of the reinforcement phase, meeting the requirements of materials in complex application scenarios. Currently, 陶铝 new materials have broad application prospects in the aviation, aerospace, and automotive industries.
Aluminum-magnesium-scandium alloys have become another highly competitive potential material for commercial aircraft applications due to their excellent weldability and corrosion resistance. Compared to 6XXX series aluminum alloys, aluminum-magnesium-scandium alloys offer higher static strength, fatigue and damage fracture performance, superior welding properties, and better corrosion resistance. Currently, medium-to-high-strength aluminum-magnesium-scandium alloys such as AA5024 and AA5028 from Germany's Rhein Aluminum are included in Airbus's material procurement catalog. Airbus-developed Scalmalloy, a high-strength aluminum-magnesium-scandium alloy, has been used in additive manufacturing. In 2016, Airbus 3D-printed a cabin partition using this material, helping the Airbus A320 achieve weight reduction.
Additionally, large-scale primary load-bearing structures in aircraft have a strong demand for high-strength titanium alloys and damage-tolerant titanium alloys. Represented by Ti-1023, high-strength and high-toughness titanium alloys designed for damage tolerance requirements exhibit characteristics such as high specific strength, excellent fracture toughness, good hardenability, low forging temperature, superior fatigue resistance, and strong stress corrosion resistance. These alloys can replace Ti-6Al-4V in primary load-bearing structures like landing gear, achieving a 20% weight reduction benefit. This plays a significant and positive role in improving structural efficiency, reducing fuel consumption, and lowering costs. They have already been applied in aircraft such as the Airbus A320 and Boeing 777.
Shape Memory Alloy
Shape Memory Alloys (SMAs) are a class of intelligent metallic materials that possess the characteristic of integrating sensing and actuation, meaning "the material is the device."
Shape memory alloys possess two major properties: shape memory effect and superelasticity, which make them highly suitable for applications in the aerospace industry. Under the influence of temperature or electric current, shape memory alloys can exhibit self-driven effects, eliminating the need for complex drive mechanisms like motors or actuators. Intelligent actuation devices fabricated from shape memory alloy materials are becoming popular solutions for novel smart structures such as foldable wingtips, variable geometry wings, de-icing leading edges, and noise-reducing nacelles, due to their lightweight, continuous and coordinated deformation, significant relative deformation capability, lack of noise, and ease of control. The characteristics include: simple driving conditions; large output force and displacement, capable of meeting demands for significant deformation and high output force; small spatial requirements, flexible design and layout; high static strength, resistant to damage; no pollution or noise.
Shape memory alloys have great potential for application in future civil aircraft. Boeing and Airbus have already laid out patent strategies for SMA actuators and latch mechanisms. In terms of morphing wings, SMAs also have potential applications. Scholars from Nanjing University of Aeronautics and Astronautics have developed a variable height winglet with a grid structure and a variable tilt angle winglet driven by SMA springs on scaled demonstration aircraft.
The movable surface structure of civil aircraft is an important structure for realizing flight control and lift enhancement. Currently, the actuation of such structures is mainly achieved through various types of actuators, such as hydraulic actuators and electro-hydraulic actuators, which are relatively heavy compared to traditional actuators. In the face of the urgent demands for more economical and environmentally friendly civil aircraft in the future, weight reduction of aircraft needs to be considered from various aspects. In terms of actuators for movable surface structures, research has shown that SMA actuators can achieve weight reduction of over 50% compared to traditional actuators. The "SAW (Spanwise Adaptive Wing)" project, jointly conducted by NASA and Boeing, focuses on SMA actuators and has carried out technical feasibility verification of the application of SMA actuation devices on aircraft, covering materials, processes, structures, and both scaled and full-size platform validation.
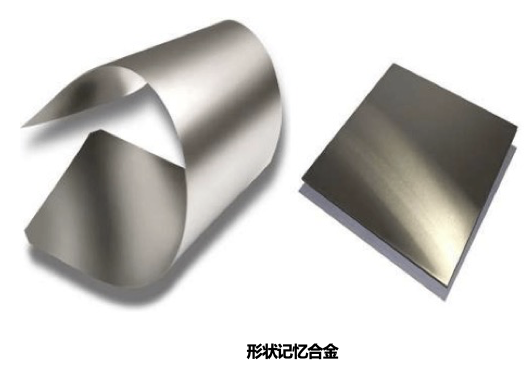
High-performance/high-temperature resistant composite materials
Composite materials, whether fibers or matrix, come in a wide variety, and the combinations of these materials result in even more types of composite materials. Aerospace composite materials require better and more stable performance than general composite materials. Carbon fiber reinforced resin matrix composites have high specific strength and specific modulus, good tailorability of material properties, a variety of molding process options, as well as excellent fatigue resistance and corrosion resistance, and are widely used in the aviation field. Currently, the application of carbon fiber composites has become one of the important indicators of the advancement of civil aircraft. In addition, temperature-resistant composites represented by ceramic matrix composites have also become a potential avenue for achieving structural lightweighting in civil aircraft.
In March 2014, Dongli Company utilized traditional PAN solution spinning technology, precisely controlled the carbonization process, and employed advanced nanotechnology to improve the microstructure of carbon fibers at the nanoscale, significantly enhancing their strength and modulus. This led to the successful development of high-performance carbon fiber at the T1100G level, with a modulus increased to 324 GPa and strength raised to 7.0 GPa. Relevant companies and institutions in Japan and the United States have clearly stated that the application goal for high-performance carbon fibers is the high-end aerospace market, aiming to replace the currently widely used carbon fiber products, enhance the comprehensive performance of aircraft structural components in terms of strength and stiffness, reduce structural thickness, lighten weight, improve flight speed, and greatly enhance maneuverability.
The world's largest tier one aerospace structure manufacturer, Spirit Aerosystems, has launched an innovative composite fuselage wall panel based on T1100, which is expected to reduce production costs for future composite fuselages by 30%. In 2022, Overair announced a collaboration with Toray Composite Materials America to construct the main fuselage components of its "Butterfly" electric vertical takeoff and landing aircraft using the next-generation T1100/3960 high-performance materials. With the rapid development of aviation technology, more extreme environments pose higher demands on aircraft materials, creating an urgent need for the development and application of materials that withstand low-temperature insulation, high-temperature resistance, and radiation resistance. For hypersonic aircraft, both the aircraft's surface and internal power systems are facing increasingly significant high-temperature issues, raising the requirements for materials' high-temperature performance. High-temperature/thermal protection materials include advanced high-temperature alloys and ceramic matrix composites, ultra-high-temperature ceramics, high-temperature insulation materials, refractory materials, and thermal protection coating technologies.
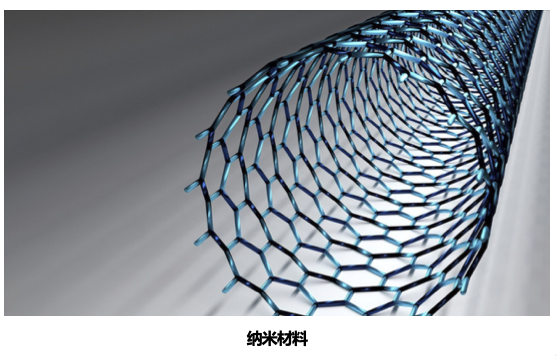
Thermoplastic composites
Fiber-reinforced thermoplastic composites refer to composite materials reinforced with carbon fibers, glass fibers, aramid fibers, etc., and thermoplastic resins.
Compared to thermoset composites, continuous carbon fiber-reinforced thermoplastic composites offer outstanding post-impact compression performance, high fracture toughness, recyclability, lower storage costs, and shorter processing cycles, making them suitable for demanding environments and high-load-bearing applications. Additionally, since thermoplastic composite components can be welded together without drilling or riveting, they significantly reduce structural weight and manufacturing costs while improving structural efficiency. Currently, aerospace-grade thermoplastic composite systems include CF/PPS, CF/PEEK, and CF/PEKK, which are used for functional components and primary/secondary load-bearing structures. Other thermoplastic material systems, such as nylon and PI, are also applied.
Major countries around the world attach great importance to the research of thermoplastic composites. In recent years, under the strong promotion of the EU and aerospace manufacturing companies such as Airbus and Fokker Aerospace, thermoplastic composites have frequently made their mark on civilian aircraft, becoming formidable competitors to thermosetting composites in some components. The most representative applications include the use of thermoplastic composite wing leading edges and keel beam structures in the Airbus A340 and A380 aircraft. The connection between the skin and ribs of the leading edge employs advanced thermoplastic welding technology. Meanwhile, Airbus has applied PEEK advanced composite corner pieces on the A350 aircraft, with as many as 3,000 of them. The Affordable Primary Aircraft Structures Thermoplastic (TAPAC) organization developed thermoplastic composite torque box segments for structures such as parallel tails and thermoplastic composite fuselage panels with stiffened structures in 2011.
In 2024, the Fraunhofer Institute for Manufacturing Technology and Advanced Materials (IFAM) announced that it had completed, in collaboration with partners, a thermoplastic composite fuselage demonstrator measuring 8 meters in length and 4 meters in diameter, which is currently the largest carbon fiber reinforced thermoplastic composite fuselage component in the world. The materials and manufacturing technologies used in this project can reduce structural weight by approximately 10% and lower costs by 10% during high-speed production processes.
Advanced Intelligent Materials
Smart materials and structures integrate sensors, actuators, and control elements with the main body structure, not only possessing the ability to bear loads and transmit motion but also featuring functions such as detection (stress, strain, damage, temperature, pressure, etc.), deformation (altering structural shape and position to achieve optimal aerodynamic characteristics), and modifying structural properties (stress-strain distribution, structural damping, natural frequency, surrounding electromagnetic field distribution). The advent of smart materials enables structures to not only carry loads but also exhibit perception (self-detection capability), decision-making (self-processing capability), and even execution functions (self-healing and adaptive capabilities).
Currently, carbon nanotubes and graphene, among other nanomaterials, have become focal points in the field of smart materials due to their excellent thermal, electrical, and optical properties. Additionally, shape memory alloys, piezoelectric materials, and electrorheological materials are gaining widespread application because of their good integrability for monitoring and feedback. The damage sensitivity of smart composite materials has rapidly improved in recent years with extensive research both domestically and internationally, making their applications in damage monitoring a hot topic of study.
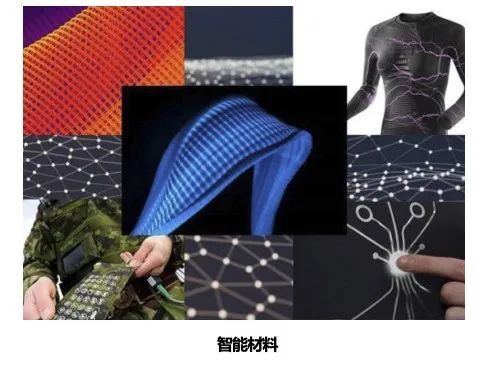
The realization of intelligent composite materials for civil aircraft will rely on three methods:
One is to disperse graphene or carbon nanotube powder in the matrix material, and achieve the monitoring of the matrix material through the change in the structural resistance of the nanomaterial during the deformation process of the composite material.
Second, form a conductive thin-film network structure using nanomaterials through specific methods, and monitor by utilizing changes in the electrical properties of the conductive network structure during the deformation of the material.
The third approach involves coating other fiber materials with nanomaterials to enhance their conductivity, and monitoring structural deformation through changes in the resistance of the conductive fibers during deformation. This material achieves self-sensing, self-detecting, and self-adapting purposes by perceiving microstructural changes and responding to macroscopic parameters.
Focused research and development in this field are expected to achieve further breakthroughs in material preparation and sensing characteristics, playing a significant role in future civil aircraft models. By embedding or attaching smart actuation materials such as shape memory alloys, piezoelectric materials, and electrorheological materials into composite materials, it is possible to control vibration and noise, adjust shapes, and enhance the matrix of composite structures. This can significantly improve the efficiency of composite material usage and meet the special requirements of service environments for composite structures. Smart structures are closely related to cutting-edge disciplines such as materials science, information science, bionics, and life sciences, offering vast application prospects and potentially revolutionizing concepts in structural design, manufacturing, maintenance, and control.
Integrated Structural Materials
With the increasing demand for environmental protection in civil aviation, countries around the world have successively launched Clean Sky projects, aiming to reduce fuel consumption and carbon emissions through collaborative research on new materials, processes, and technologies. Structural-functional integrated composite materials are considered one of the key technologies with significant potential for structural weight reduction in the future. The approach involves integrating the functional requirements of civil aircraft into existing structures, combining load-bearing and functional structures into one.
Current advanced international aircraft models have achieved structural-functional integration in specific areas, such as the electrothermal anti-icing leading edge used in the Boeing 787 and the lightning protection network combining metal strips and structural components in the Airbus A350. Compared to traditional pneumatic anti-icing systems that require extensive piping, the electrothermal anti-icing integrated structure eliminates the need for additional structural installations, saving weight, and its thermal efficiency is more than 1.5 times that of pneumatic methods. By integrating conductive materials with structural design, the electrical conductivity of composite materials can be enhanced, providing effective protection for the aircraft structure and systems. Additionally, load-bearing energy storage composite material technology is a highly researched field, characterized by enabling composite structures to meet load-bearing requirements while possessing certain electrical storage capabilities, thereby effectively reducing aircraft weight. With the development of the low-altitude economy, the relatively heavy battery power systems currently constrain the endurance and effective payload capacity of drones. Carbon fiber-based structural energy storage composite materials are expected to save payload space, reduce system weight, and improve battery energy density, making them a research hotspot for universities and research institutions both domestically and internationally.
In addition to withstanding flight loads, aircraft structures must also meet requirements such as lightning protection, sound insulation and noise reduction, anti-icing and de-icing, and fire resistance. Traditional functional structural designs often lead to increased structural weight, resulting in higher flight costs and reduced economic efficiency. Nanomaterials such as graphene and carbon nanotubes, biomimetic materials, and shape memory alloy materials exhibit excellent performance in optical, electrical, mechanical, and acoustic aspects. Their application in aircraft structures will enable integrated functional structural design, achieving weight reduction and efficiency improvement, with broad prospects. For example, an integrated structure of graphene film and composite wing skin can provide functions such as anti-icing/de-icing and lightning protection for the wing skin, eliminating the need for additional weight from lightning protection copper mesh and bleed air anti-icing pipelines. The engine nozzle of the Boeing 777-300 uses SMA materials to achieve configuration changes that reduce noise. Nanjing University of Aeronautics and Astronautics has developed a prototype aircraft that uses SMA springs to drive variable cant-angle winglets. The development of nanotechnology, biomimetic technology, and new functional materials provides possibilities for integrated structural and functional design in civil aircraft. In summary, integrated structural and functional design and manufacturing are expected to offer new methods and approaches to solving aircraft functional issues, while also enhancing the efficiency, economy, and competitiveness of airframe structures.
Additive manufacturing
Additive Manufacturing, also known as 3D printing, is a forming technology that integrates various fields and disciplines such as materials engineering, mechanical engineering, computer engineering, and laser and electron beam technologies.
It is based on computer three-dimensional digital models, and through software, the models are layered and constructed by printing raw materials such as powder or wire layer by layer, achieving integrated forming of complex structural parts, personalized customization of special structural parts, and rapid response to design requirements.
Compared with traditional manufacturing processes, additive manufacturing can enhance the flexibility and freedom of part design; achieve the one-piece forming of complex parts, improving the overall performance and quality of the parts; increase material utilization and reduce material waste; and facilitate prototype validation and personalized customization of parts. These advantages have led to widespread attention and application of additive manufacturing in various fields such as aerospace, automotive, and medical.
The aforementioned advantages of additive manufacturing align well with the goals and demands of weight reduction, cost savings, and rapid response in civil aircraft, making it a consistently high-profile technology in the field of civil aircraft manufacturing. Companies such as Boeing, Airbus, and COMAC have already achieved the application of additive-manufactured components in aircraft. As the technology matures further, the use of additive manufacturing in the civil aviation industry will continue to expand.
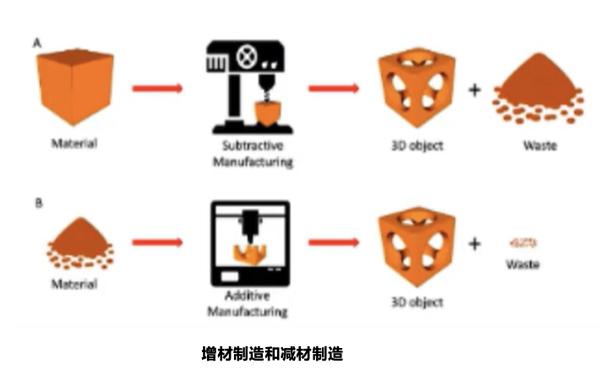
Metal Additive Manufacturing
According to the materials used, additive manufacturing can be divided into metal additive manufacturing and non-metal additive manufacturing.
Metal additive manufacturing uses metal powders/wires as raw materials and high-energy beams (such as lasers, electron beams, arcs, plasma beams, etc.) as the energy source to manufacture high-performance metal components. According to the manufacturing principle, metal additive manufacturing technology can be further divided into Powder Bed Fusion (PBF) technology and Directed Energy Deposition (DED) technology.
Powder bed fusion technology was patented by EOS in 1994. This technology involves supplying a uniform layer of powder onto a deposition plane and directing an energy source to irradiate the powder at specified locations, causing it to melt and solidify. Once a plane is completed, the energy is directed to the next plane, repeating the process until the part is fully formed.
Directed Energy Deposition (DED) technology was first successfully developed by Sandia National Laboratories in the United States in 1995. This process involves feeding metal powder or wire to a substrate and focusing a laser beam, electron beam, or arc energy source onto the powder bed to form multiple small molten pools and continuously deposit material, ultimately achieving integrated forming. Depending on the selected energy source, DED technology can also be categorized into laser metal deposition, electron beam additive manufacturing, wire arc additive manufacturing, and other techniques.
Non-metal additive manufacturing
Similar to metal additive manufacturing technology, non-metal additive manufacturing technology involves the layer-by-layer printing of non-metallic material filaments or powder raw materials to achieve the final shape. The two commonly used non-metal additive manufacturing technologies in the civil aircraft industry are Fused Deposition Modeling (FDM) and Selective Laser Sintering (SLS). Non-metal additive manufactured parts are often used for functional interior components and functional secondary load-bearing components.
Fused Deposition Modeling (FDM) technology was invented in the 1980s by Scott Crump, the founder of American company Stratasys. This technology heats and melts thermoplastic filaments, which are then extruded from a nozzle along the paths determined by slicing software at a certain speed. The extruded filament solidifies on the platform, after which the nozzle is raised to form the next layer.
FDM technology does not involve laser, high temperature and high pressure environments, making the technology relatively simple. The equipment is compact, the operation is straightforward, and both printing and maintenance costs are relatively low. The raw materials do not undergo chemical changes during the entire forming process, and the warpage and deformation of the parts are minimal. A variety of commonly used engineering plastics such as ULTEM 9085, polycarbonate (PC), and nylon (PA) can be selected as raw materials for printing. However, it also has some noticeable drawbacks: the surface roughness is relatively high; support structures are needed during the forming process, and removing the supports after printing can be complicated and may leave marks on the surface; due to the limitations of the printing process, parts manufactured using FDM technology have significantly weaker strength in the vertical forming direction compared to other printing directions, and the issue of anisotropy is prominent. Despite having many disadvantages, FDM technology is mature, easy to operate, and cost-effective, and has been widely used in the manufacturing of non-metal interior parts for aircraft.
Selective Laser Sintering (SLS) technology was invented by Dr. Carl Deckard in 1989. This technology uses a laser to sinter layers of material powder that are spread on a platform. Once the sintering of one layer's cross-section is completed, new powder is evenly spread over the sintered cross-section to sinter the next layer. After all cross-sections have been sintered, the excess powder is removed to obtain a fully formed part. Parts manufactured using SLS technology exhibit better performance and reduced anisotropy, making them highly valuable in the field of civil aviation manufacturing.
Titanium Alloy Additive Manufacturing
Titanium alloy additive manufacturing components have been applied in various models. In 2016, Airbus utilized Ti-6Al-4V additive manufacturing to optimize the design of the A350XWB connection bracket and successfully implemented it in the aircraft. This marked the first time that a metal additive manufacturing component was installed in a model, as shown in the figure. Airbus adopted titanium alloy additive manufacturing technology to optimize the structure of this component, successfully reducing its weight by over 30%, significantly shortening the delivery cycle, and lowering manufacturing costs.
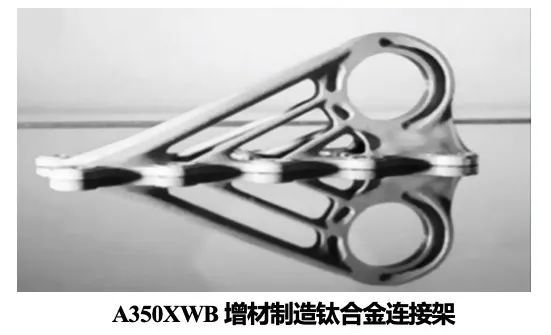
Aluminum alloy additive manufacturing
The vertical tail fin support of the Airbus A350XWB is made using AlSi10Mg through additive manufacturing, integrating 30 parts into one, achieving a weight reduction of up to 30%, and successfully shortening the manufacturing cycle from 70 days to 19 hours, significantly reducing the manufacturing time.
The Airbus A320 lightweight bio-inspired cabin partition structure utilizes the second-generation Al-Mg-Sc alloy Scalmalloy®️ developed by Airbus subsidiary APWORKS, employing Selective Laser Melting (SLM) technology, achieving a 45% weight reduction and a 75% cost reduction, thereby meeting the design requirements for weight and cost reduction in the model.
Additive manufacturing of resin-based composites
For additive manufacturing, the most commonly used composite materials are fiber-reinforced resin matrix composites. Fiber-reinforced resin matrix composites are composed of chopped or continuous fibers and their fabrics reinforcing thermosetting or thermoplastic resin matrices, formed through specific processes. They are widely applied in aerospace, automotive manufacturing, and other fields, characterized by high specific strength and specific modulus, fatigue resistance, corrosion resistance, strong designability, ease of large-area integral forming, and special electromagnetic properties. The extensive use of fiber-reinforced composites in the aerospace field not only reduces structural weight but also enhances equipment performance and quality through integrated structural and functional design.
Currently, commonly used additive manufacturing composite materials typically use PEEK, PEKK, and nylon as the matrix, with carbon fiber or glass fiber to reinforce and enhance the material's various properties. In 2019, the HexPEKK-100 material, based on carbon fiber and PEKK and produced by America's largest carbon fiber manufacturer, completed certification. It was used to manufacture pipeline components and other parts for the Boeing 777X using Selective Laser Sintering (SLS) technology, reducing the weight by about 50% compared to the original aluminum alloy parts. The figure below shows some of the composite material pipeline components of the Boeing 777X.
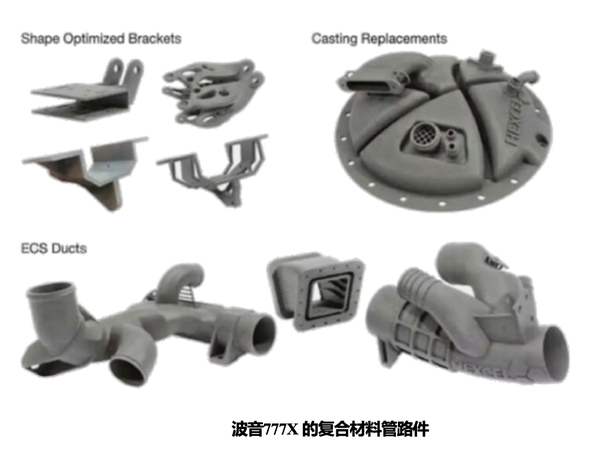
The Challenges of Additive Manufacturing
In the civil aircraft industry, companies including Boeing, Airbus, and COMAC are actively promoting the application of additive manufacturing and have implemented additive-manufactured parts in multiple aircraft models. The civil aircraft industry imposes extremely high demands on material performance and reliability, meaning materials suitable for traditional manufacturing techniques may not necessarily be suitable for additive manufacturing. Therefore, developing high-performance materials tailored for additive manufacturing and establishing a rigorous, comprehensive quality control and certification system is particularly critical.
【Copyright and Disclaimer】The above information is collected and organized by PlastMatch. The copyright belongs to the original author. This article is reprinted for the purpose of providing more information, and it does not imply that PlastMatch endorses the views expressed in the article or guarantees its accuracy. If there are any errors in the source attribution or if your legitimate rights have been infringed, please contact us, and we will promptly correct or remove the content. If other media, websites, or individuals use the aforementioned content, they must clearly indicate the original source and origin of the work and assume legal responsibility on their own.
Most Popular
-
Covestro faces force majeure!
-
Breaking News! Mitsui Chemicals TDI Unit in Japan Experiences Chlorine Gas Leak Accident!
-
DuPont plans to sell Nomex and Kevlar brands for $2 billion! Covestro Declares Force Majeure on TDI / oTDA-based / Polyether Polyol; GAC Group Enters UK Market
-
Mitsubishi Chemical Exits! Sumitomo Acquires!
-
Borealis suspends polyolefin recycling plant in Austria, Hyundai achieves record Q2 revenue, Volkswagen lowers performance expectations