The "Golden Triangle" formula for air bags in container loading
1. Material and Structure
1. Material Properties
Inflatable bags for containers are typically made from high-strength, flexible polyethylene (PE) or polypropylene (PP) materials. Some high-end products may incorporate nylon layers or composite film structures to enhance puncture resistance and durability. The material must have excellent airtightness to maintain pressure for a long time after inflation, while also possessing wear-resistant and tear-resistant properties to withstand the complex environments encountered during long-distance transportation.
2. Structural Design
Multi-layer composite structure: Commonly consists of a wear-resistant outer layer + a middle cushioning layer + an inner gas barrier layer. For example, the outer layer uses nylon fabric to enhance tensile strength, the middle layer is made of expanded polyethylene (EPE) for cushioning, and the inner layer is polyethylene film to prevent air leakage.
Inflatable valve design: Equipped with a quick inflation valve, supporting manual or pump inflation. Some products use one-way valve technology to prevent gas backflow.
The core logic of co-extruded film formula design
The co-extruded film structure consisting of 50% nylon (PA), 30% metallocene polyethylene (mPE), and 20% linear low-density polyethylene (LLDPE) achieves the goals of "high strength, high sealing, and high adaptability" for inflatable bags through complementary material properties.
1. Nylon (PA): Provides high mechanical strength and gas barrier properties, puncture resistance, and impact resistance, while inhibiting the permeation of oxygen and water vapor, extending the lifespan of inner bags. High strength puncture resistance: Nylon (PA) offers structural support, metallocene polyethylene (mPE) enhances tear resistance, and linear low-density polyethylene (LLDPE) improves flexibility, with the three working together to achieve a 30%-50% increase in compressive strength.
2. Metallocene Polyethylene (mPE): Enhances the flexibility and ductility of films, reduces low-temperature brittleness, allowing inflatable bags to maintain elasticity in environments ranging from -40℃ to 80℃, adapting to extreme transportation conditions.
3. Linear low-density polyethylene (LLDPE): As a heat sealing layer, it ensures that the film seals quickly at high temperatures, preventing gas leakage after inflation, while also enhancing resistance to environmental stress cracking.
Core Advantages of Applying to Container Airbags
error
2. Puncture Resistance and Environmental Durability
3. Environmental Protection and Economy
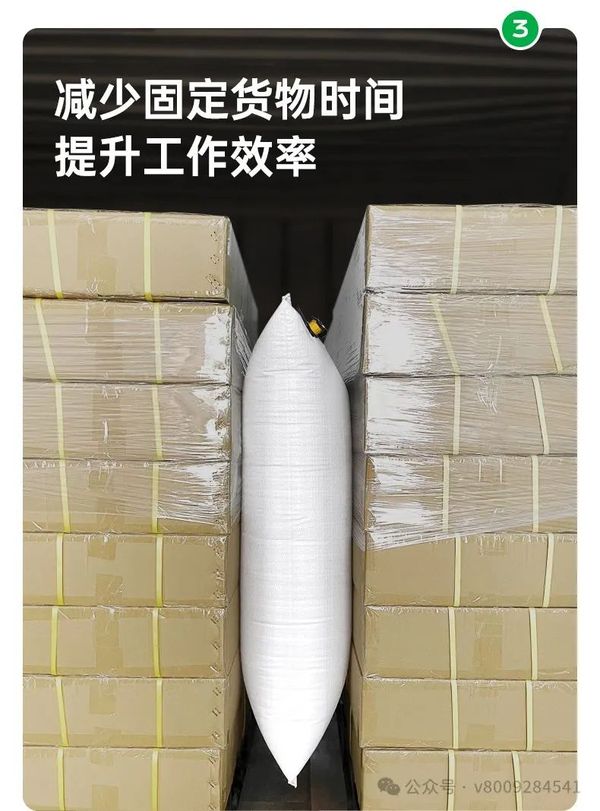
III. Practical Application Scenarios
Precision instrument transportation, such as medical equipment and aviation components, utilizes its shock resistance to prevent damage from vibrations.
Hazardous materials protection: chemical raw materials, lithium batteries, etc., prevent leakage risks through high barrier properties.
Cold chain logistics: Maintain flexibility in low-temperature environments to prevent packaging from breaking due to temperature changes.
Four Major Advantages of Air Bags Used in Containers
1. Pressure and explosion resistance: Can withstand cargo compression strength ≥ 2 tons/㎡, preventing damage during transportation due to uneven pressure.
2. Lightweight and energy-saving: Optimized material density, reducing the weight of the inflatable bag by 20%, which decreases transportation energy consumption.
High reuse rate: The wear-resistant layer (nylon outer layer) is designed for a reuse cycle of ≥200 times, with costs only 60% of those of traditional PE inflatable bags.
4. Rapid heat sealing compatibility: Linear high-pressure layer has a low melting point (110-130℃), supporting high-speed automated production, with sealing strength ≥25N/15mm.
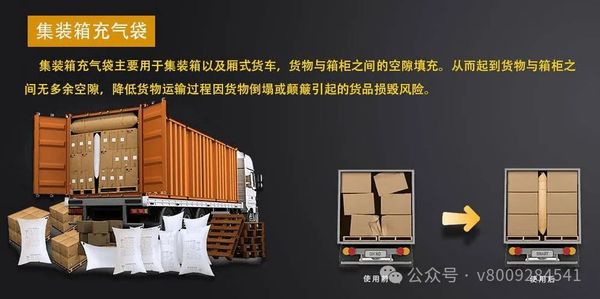
Data support:
Electronic Product Transportation: A multinational logistics company uses multi-layer composite air bags to secure high-value electronic components, reducing the damage rate by 90%.
Cold chain transportation of food: In seafood containers, air bags are used to secure the container and isolate condensation, preventing damage and contamination to the packaging.
Case: After adopting this structure of inflatable bags, a certain international logistics company saw the damage rate of sea-transported electronic components drop from 5% to 0.3%, and the annual packaging cost savings per container exceeded ten thousand yuan.
IV. Industry Trends and Future Directions
Material upgrade: Adding a nano-coating (such as silica) to further enhance barrier properties, or introducing biodegradable resins (such as PBAT) to achieve full eco-friendliness.
Intelligent Design: Integrating pressure sensors to monitor the status of the inflatable bag in real time, preventing overinflation or leakage.
Summary
A co-extruded film consisting of 50% nylon, 30% metallocene, and 20% linear high-pressure, redefines the performance boundaries of container inflation bags through its "tough yet flexible" material combination. Its breakthroughs in logistics cost control, cargo safety protection, and environmental sustainability are driving the transportation packaging industry into a new era of "efficiency, safety, and greenness."
Container air bags, with their scientifically formulated material composition, multifunctional structural design, and efficient protective properties, have become an essential packaging solution in modern logistics. In the future, as material technology advances, their environmental friendliness and intelligent features (such as pressure-sensitive inflation) will further improve, leading to more extensive applications.
【Copyright and Disclaimer】The above information is collected and organized by PlastMatch. The copyright belongs to the original author. This article is reprinted for the purpose of providing more information, and it does not imply that PlastMatch endorses the views expressed in the article or guarantees its accuracy. If there are any errors in the source attribution or if your legitimate rights have been infringed, please contact us, and we will promptly correct or remove the content. If other media, websites, or individuals use the aforementioned content, they must clearly indicate the original source and origin of the work and assume legal responsibility on their own.
Most Popular
-
Covestro faces force majeure!
-
Breaking News! Mitsui Chemicals TDI Unit in Japan Experiences Chlorine Gas Leak Accident!
-
Mitsubishi Chemical Exits! Sumitomo Acquires!
-
DuPont plans to sell Nomex and Kevlar brands for $2 billion! Covestro Declares Force Majeure on TDI / oTDA-based / Polyether Polyol; GAC Group Enters UK Market
-
Borealis suspends polyolefin recycling plant in Austria, Hyundai achieves record Q2 revenue, Volkswagen lowers performance expectations