Abstract: The melting temperature of the semi-aromatic poly(pentamethylene terephthalamide) (PA5T) homopolymer is close to its thermal decomposition temperature, making it prone to decomposition during melt processing. To address this issue, a copolymer (PA5T-co-56) of PA5T and poly(pentamethylene adipamide) (PA56) was synthesized using pentamethylenediamine, adipic acid, and terephthalic acid through a salt formation and polymerization process. The structure of PA5T-co-56 was analyzed by Fourier transform infrared spectroscopy and nuclear magnetic resonance spectroscopy. Based on this, the thermal properties and crystallization performance of PA5T-co-56 were tested using differential scanning calorimetry, thermogravimetric analysis, and X-ray diffraction, and its solvent resistance was characterized. The results showed that with the increase in the content of the PA56 segment in the copolymer structure, the crystallization temperature and melting temperature of PA5T-co-56 gradually decreased. When the molar ratio of the PA56 segment was 40%, 50%, 60%, and 70%, the melting temperature of the copolymer decreased by 56.42, 74.70, 83.03 °C, and 91.66 °C, respectively, compared to that of PA5T. This is mainly due to the introduction of the PA56 segment, which reduces the proportion of rigid benzene rings in the polymer molecular chain and increases the flexibility of the molecular chain. The introduction of the PA56 segment did not significantly reduce the thermal stability of the polymer, nor did it change the main crystal form of the polymer, which remained primarily γ-form.
Polyamide (PA) resin can be formed by the self-polymerization of lactam molecules or by the condensation polymerization of diamines and dicarboxylic acids. According to their main chain structure, they can be classified into aliphatic PA, semi-aromatic PA, and fully aromatic PA [1-3]. Among them, the most widely used aliphatic PAs, PA6 and PA66, have excellent physical and mechanical properties, wear resistance, self-lubrication, and noise absorption performance, and have been extensively applied in fields such as automobiles, machinery, and electrical appliances [2-6]. With the development of surface mount technology (heat resistance temperature ≥ 270 ℃) and the higher requirements for heat resistance and weather resistance of materials in fields like optics, aerospace, and military, the performance of aliphatic PAs such as PA6 and PA66 has become difficult to meet the usage demands [7-8]. Fully aromatic PAs, with a high density of rigid benzene rings and excellent heat resistance, have a thermal decomposition starting temperature lower than the melting temperature, making it difficult to process through melting, which limits their further application. Semi-aromatic PAs, containing both flexible aliphatic segments and rigid benzene ring segments, combine the good processability of aliphatic PAs with the outstanding heat resistance of fully aromatic PAs [9].
Currently, the semi-aromatic PAs that have been industrialized mainly include copolymers of PA6T, PA9T, and PA10T[10-12]. Compared to PA10T and PA9T, PA6T has better heat resistance, lower cost, and greater market competitiveness. However, the development of petroleum-based product PA6T is limited by China's energy situation characterized by abundant coal, scarce oil, and limited gas, as well as the environmental pressure of carbon peak and carbon neutrality[13]. The structure of pentamethylene diamine is similar to that of hexamethylene diamine, and BioAmber Inc. has already industrialized bio-based pentamethylene diamine[14-16]. Based on the above background, using bio-based pentamethylene diamine and terephthalic acid as the main raw materials, bio-based poly(pentamethylene terephthalamide) (PA5T) was prepared. On this basis, aliphatic poly(pentamethylene adipamide) segments (PA56) were introduced into the main chain of PA5T to prepare a copolymer of poly(pentamethylene terephthalamide) and poly(pentamethylene adipamide) (PA5T-co-56) with a wider processing window. The structures of PA5T and PA5T-co-56 were confirmed, and their thermal properties, crystallization performance, and solvent resistance were tested and characterized.
1 Experimental Section
1.1 Main Raw Materials
Pentanediamine: purity >99.5%, Shanghai KaiSai Biotechnology Co., Ltd.;
Terephthalic acid: purity 99%, Shanghai Macklin Biochemical Co., Ltd.;
Adipic acid: purity ≥99%, Shanghai Macklin Biochemical Technology Co., Ltd.;
deionized water: homemade in the lab.
1.2 Main Instruments and Equipment
Magnetic drive reactor: XSF-J, Weihai Hangyu Chemical Machinery Co., Ltd.
Recirculating water multi-purpose vacuum pump: SHZ-95B, Henan YuHua Instrument Co., Ltd.;
vacuum drying oven: DZF-2001, Shanghai Yiheng Scientific Instrument Co., Ltd.;
Fourier Transform Infrared (FTIR) Spectrometer: IS50, Thermo Niolet, USA;
Nuclear Magnetic Resonance Spectrometer: AVANCE Ⅲ HD, Bruker, Germany;
Differential Scanning Calorimetry (DSC) instrument: Q20, TA Instruments, USA;
Thermogravimetric (TG) Analyzer: Q5000, TA Instruments, USA;
X-ray diffraction (XRD) instrument: TD3700, Dandong Tongda Technology Co., Ltd.
1.3 Preparation of PA5T and PA5T-co-56 salt
According to the ratios in Table 1, appropriate amounts of pentamethylenediamine, adipic acid, terephthalic acid, and deionized water at 30% of the mass fraction of the above raw materials are weighed and added to a three-necked flask. The mixture is then gradually heated to 50~60 ℃, where it reacts continuously for 2 h. The pH is adjusted to an appropriate value. After the reaction, the sample is placed in a vacuum drying oven at 80 ℃ for 24 h, yielding PA5T and PA5T-co-56 salts.
Table 1 Molar ratio of raw materials for PA5T and PA5T-co-56
1.4 Preparation of PA5T and PA5T-co-56
The salts from the different formulations and an appropriate amount of deionized water are added to a high-temperature, high-pressure polymerization reactor. The reactor is purged with nitrogen for 5 min. Then, the reaction system is gradually heated to 220~230 ℃ over 2 h, maintaining the pressure inside the reactor at 2.0 MPa. After reacting for 1 h, the pressure is gradually released to atmospheric pressure, while the temperature is increased to 240~260 ℃. The vacuum is then drawn down to -0.09 MPa, and the reaction continues for 1~3 h under these temperature and pressure conditions. The sample is then removed, yielding PA5T and PA5T-co-56 polymers.
1.5 Testing and Characterization
FTIR measurement: A small amount of the sample is mixed and ground with potassium bromide, then pressed into a tablet for testing in transmission mode.
Nuclear magnetic resonance hydrogen spectroscopy characterization: dissolve a small amount of sample in deuterated trifluoroacetic acid solvent, followed by testing and confirmation of the polymer structure.
XRD test: Place each formulation polymer sample into the XRD instrument for testing, set the scanning range to 5°~80°, and the scanning speed to 5°/min.
DSC test: Weigh 3~10 mg of the sample and place it in a crucible, heat at a rate of 40 ℃/min to above the melting temperature of the sample, hold at this temperature for 5 min to eliminate thermal history, then cool at a rate of 20 ℃/min to 30 ℃, hold at this temperature for 5 min, and then heat again at a rate of 20 ℃/min to above the melting temperature of the sample. Record the DSC cooling curve and the second heating curve.
TG test: Place an appropriate amount of sample in the crucible, under a nitrogen atmosphere, and gradually increase the temperature to 700 ℃ at a rate of 10 ℃/min, recording the TG curve.
Solvent resistance test: Place an appropriate amount of sample in solvents such as tetrahydrofuran, dimethylformamide, dimethyl sulfoxide, benzene, methanol, and concentrated sulfuric acid. Under a temperature condition of 25 ℃, turn on the stirring, and after placing for 24 h, test whether the mass has changed, determine if it has dissolved, and record the test results.
2.1 FTIR Analysis of PA5T and PA5T-co-56
The FTIR curves of PA5T and PA5T-co-56 are shown in Figure 1. In Figure 1, the peak at 3,300~3,500 cm-1 corresponds to the N—H stretching vibration absorption peak of the amino group; the peak at 1,635 cm-1 is the amide I band (C=O stretching vibration peak); the peak at 1,547 cm-1 is the amide II band (C—N stretching vibration peak and N—H in-plane bending vibration peak); the peak at 1,496 cm-1 is the amide III band (C—N stretching vibration peak and C—H in-plane bending vibration peak); the peak at 1,285 cm-1 corresponds to the amide IV band (C—C=O stretching vibration absorption peak). The CH2 wagging vibration peak is at 720 cm-1, and the N—H out-of-plane bending vibration peak is at 680 cm-1 [17]. The combined frequency and double frequency absorption peaks of NH3+ for the PA5T-co-56 salt also did not appear around 2,130 cm-1, confirming that PA5T and PA5T-co-56 resins were indeed synthesized.
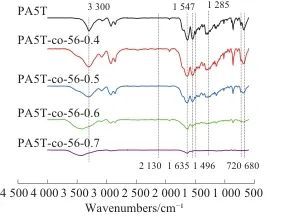
Fig. 1 FTIR spectra of PA5T and PA5T-co-56
2.2 Nuclear Magnetic Resonance Hydrogen Spectrum Analysis
Figure 2 shows the nuclear magnetic resonance hydrogen spectra of PA5T and PA5T-co-56-0.6. Position 1 in Figure 2 corresponds to the hydrogen atoms on the benzene ring of PA5T and PA5T-co-56 polymers, position 2 corresponds to the hydrogen atoms on the first carbon atom after the amide group, position 3 corresponds to the hydrogen atoms on the second carbon atom after the amide group, and position 4 corresponds to the hydrogen atoms on the third carbon atom after the amide group. It can also be observed from Figure 2 that, compared to PA5T, there is a significant additional peak at position 5 in the curve of PA5T-co-56, which corresponds to the hydrogen atoms on the first methylene group connected to the amide group in the adipic acid structure. The peak positions mentioned above are consistent with the theoretical peak positions of the polymer, further confirming the structures of PA5T and PA5T-co-56 resins.
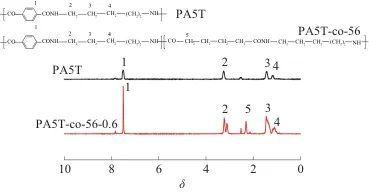
Fig. 2 Hydrogen nuclear magnetic resonance spectroscopy of PA5T and PA5T-co-56-0.6
Figure 3 and Figure 4 are the crystallization curves and secondary heating melting curves of PA5T and PA5T-co-56, respectively. The crystallization temperature and melting temperature values of each formulation are listed in Table 2. From Figure 3, it can be seen that after introducing the PA56 segment into the polymer molecular chain, there is no significant change in the width of the crystallization peak, which may be due to the length of the four methylene groups in adipic acid being 0.508 nm. At the same time, the length of the benzene ring of terephthalic acid in the 35° chain direction is 0.510 nm, and the chain lengths of adipic acid and terephthalic acid are similar, so their crystal structures are alike [18]. From Table 2, it can be found that as the content of the PA56 segment increases, both the crystallization temperature and melting temperature of the polymer show a decreasing trend, which may be because the molecular chains of PA5T contain rigid benzene rings, while the PA56 segments are prepared from aliphatic diamine and diacid reactions, resulting in greater molecular chain flexibility. As the content of the PA56 segment increases, the rigidity of the copolymer's molecular chain gradually decreases, leading to a gradual decrease in the crystallization temperature and melting temperature.
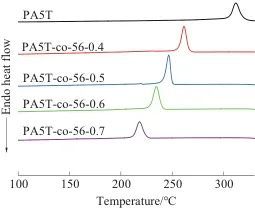
Fig. 3 Crystallization curves of PA5T and PA5T-co-56
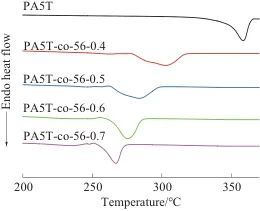
Fig. 4 Melting curves of PA5T and PA5T-co-56
Table 2 DSC and TG test data of PA5T and PA5T-co-56 ℃
Figure 5 and Figure 6 are the TG and DTG curves of PA5T and PA5T-co-56, respectively. The 5% thermal decomposition temperature and the maximum thermal degradation rate temperature for different formulations are listed in Table 2. From Table 2, it can be found that introducing PA56 segments into the PA5T molecular chain did not significantly lower the 5% thermal decomposition temperature or the maximum thermal degradation rate temperature. When the molar ratios of added PA56 segments were 40%, 50%, 60%, and 70%, the melting temperatures of the copolymers decreased by 56.42, 74.70, 83.03 ℃, and 91.66 ℃, respectively, compared to the melting temperature of PA5T. The introduction of PA56 segments can significantly reduce the melting temperature of the polymer. Therefore, PA5T-co-56 has a wider processing window than PA5T. It is also found that the melting temperature and thermal decomposition temperature of PA5T-co-56-0.4 are close to those of PA6T/66, showing comparable heat resistance to PA6T/66, and can be used as a substitute for PA6T/66 [19].
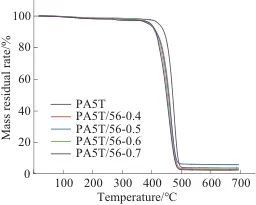
Fig. 5 TG curves of PA5T and PA5T-co-56
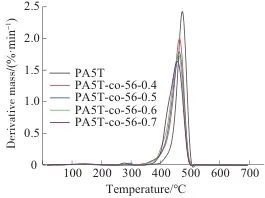
Figure 6 DTG curves of PA5T and PA5T-co-56
The XRD curves of PA5T and PA5T-co-56 are shown in Figure 7. From Figure 7, it can be found that the curves of PA5T and PA5T-co-56 both show diffraction peaks near 6.53° and 21.00°, where the peak at 6.53° is the projection of the (001) plane after the ordered arrangement of saturated alkane chains [20]. The stronger diffraction peak at 21.00°, in terms of peak height and width, did not change significantly with the increase in the content of the PA56 segment. By calculation, the main crystal sizes of PA5T and PA5T-co-56 are listed in Table 3. From Table 3, it can be seen that PA5T and PA5T-co-56 have similar grain sizes. The introduction of the PA56 segment did not significantly affect the main crystal form and crystal size of PA5T, and the crystal form was mainly γ-type, which is consistent with the analysis results of the above crystallization curves [21-22].
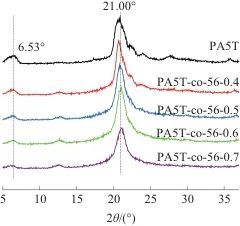
Fig. 7 XRD patterns of PA5T and PA5T-co-56
Table 3 Grain size of PA5T and PA5T-co-56
2.5 Solvent Resistance Analysis
Table 4 shows the solvent resistance test results of PA5T and PA5T-co-56. After placing PA5T and PA5T-co-56 at 25 ℃ for 24 h, the mass of the test samples did not change in organic solvents such as methanol, benzene, tetrahydrofuran, dimethylformamide, and dimethyl sulfoxide, and they only completely dissolved in concentrated sulfuric acid. All the formula samples exhibited good solvent resistance, which is due to the strong hydrogen bonding between PA molecular chains and the large intermolecular forces. Good solvent resistance allows PA5T and PA5T-co-56 to be used in most corrosion-resistant working conditions.
Table 4 Solvent resistance test results of PA5T and PA5T-co-56
Notes:+ means dissolution;- means non-dissolution.
3 Conclusion
Using pentamethylene diamine, terephthalic acid, and adipic acid as raw materials, PA5T and PA5T-co-56 were synthesized respectively, and the polymer structure, thermal properties, crystallization properties, and solvent resistance were characterized and analyzed. The results showed that with the increase in the proportion of PA56 segments, the crystallization temperature and melting temperature of the polymer both showed a decreasing trend, which is due to the introduction of PA56 segments reducing the molecular weight rigidity of the polymer; the introduction of PA56 segments did not cause a significant decrease in the thermal stability of the polymer, nor did it change the main crystal form of PA5T, with the crystal form being γ-type; PA5T and PA5T-co-56 have good thermal stability and solvent resistance, when the content of PA56 segments reaches 50%, the melting temperature of the copolymer is still greater than 280 ℃, at the same time, PA5T-co-56 has a wider processing window, and has broad application prospects in the fields of electronics, LED, and automobiles.
【Copyright and Disclaimer】The above information is collected and organized by PlastMatch. The copyright belongs to the original author. This article is reprinted for the purpose of providing more information, and it does not imply that PlastMatch endorses the views expressed in the article or guarantees its accuracy. If there are any errors in the source attribution or if your legitimate rights have been infringed, please contact us, and we will promptly correct or remove the content. If other media, websites, or individuals use the aforementioned content, they must clearly indicate the original source and origin of the work and assume legal responsibility on their own.