Research Progress and Challenges of Fluorinated Polyimide Engineering Plastics at China University of Geology
Polyimide (PI) engineering plastics have found extensive applications in modern industrial fields due to their excellent high and low-temperature resistance, environmental stability, as well as mechanical and electrical properties. According to processing characteristics, PI engineering plastics can be divided into thermoplastic and thermosetting types; according to crystallization characteristics, they can be categorized into amorphous and (semi) crystalline types; based on synthesis processes, they can be classified as "monomer reactant in situ polymerization (PMR)" types; according to reaction principles, they can be divided into condensation and addition types; based on molding processes, they can be classified into compression molding, injection molding, extrusion molding, additive manufacturing (3D printing), and resin transfer molding (RTM) types; according to chemical composition, they can be categorized into pyromellitic dianhydride (PMDA) type (referred to as "PMDA type"), 3,3',4,4'-biphenyltetracarboxylic dianhydride (sBPDA) type (referred to as "biphenyl dianhydride type"), 2,3,3',4'-biphenyltetracarboxylic dianhydride (aBPDA) type (referred to as "isomeric biphenyl dianhydride type"), 3,3',4,4'-benzophenone tetracarboxylic dianhydride (BTDA) type (referred to as "ketone dianhydride type"), 3,3',4,4'-benzophenone ether tetracarboxylic dianhydride (ODPA) type (referred to as "ether dianhydride type"), and 4,4'-(hexafluoroisopropyl) diphenyl tetracarboxylic dianhydride (6FDA) type (referred to as "fluorinated type"); according to different end groups, they can be classified into nadic anhydride type (referred to as "NA type") and phenylethyne-terminated anhydride type (referred to as "PETI").
Among various types of polyimide (PI) engineering plastics, fluorinated polyimide (FPI) stands out due to its unique high-temperature resistance and thermal oxidative stability, gaining widespread attention in specialized fields such as aerospace and civil high-tech sectors like optoelectronics. Table 1 lists the types of common fluorinated PI engineering plastics along with their typical chemical structures. Fluorination enhances the optical, dielectric, and processing properties of PI materials, making them favored by numerous researchers. Generally speaking, fluorination achieves the following functions: (1) changes in surface characteristics and moisture absorption rates. Fluorination can reduce the surface free energy of PI engineering plastics, enhancing their hydrophobicity and lowering moisture absorption. (2) changes in electrical properties. Fluorination can lower the dielectric constant of PI engineering plastics, especially in high-frequency environments. (3) changes in optical properties. Fluorination can reduce the absorption of PI engineering plastics in the visible and infrared regions, thereby improving their optical transparency and reducing haze. Furthermore, the substitution of C—H bonds with C—F bonds in the molecular structure of PI materials significantly reduces absorption in the infrared communication bands (1.3 μm and 1.55 μm). Fluorination also lowers the refractive index of PI engineering plastics. (4) changes in processing properties. Generally, fluorination can improve the solubility of PI resin in organic solvents, thus endowing it with good processing characteristics. Figure 1 compares the properties of fluorinated PI (FPI) engineering plastic Avimid® (FPI-1, see Table 1) with conventional PI engineering plastics. It is evident that fluorination provides FPI engineering plastics with excellent solubility. The outstanding comprehensive performance has led to the rapid development of FPI engineering plastics in recent years, making them one of the most important members of the specialty engineering plastics family.
Table 1 Typical FPI engineering plastics and their chemical structures
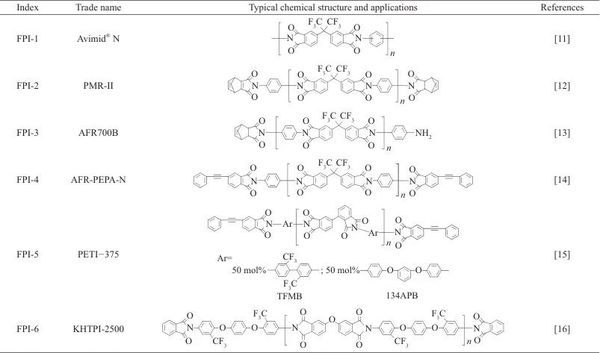
Tab. 2 Formulations of different PMR PI resins

Note:BTDE is ester of BTDA and methanol。
In recent years, there has been a growing call internationally to restrict the use of PFAS substances. In addition to small-molecule compounds such as perfluorooctanoic acid (PFOA) and perfluorooctanesulfonic acid (PFOS), PFAS substances also include high-molecular-weight compounds such as polytetrafluoroethylene (PTFE), polyvinylidene fluoride (PVDF), and FPI. Due to the excellent comprehensive properties of C-F bonds (high bond energy, high electronegativity, low molar polarizability, low molar refraction, good hydrophobicity, etc.), fluorination can often endow polymer materials with many unique properties. However, fluorinated products, especially those containing PFAS compounds, have high environmental persistence. Some types possess bioaccumulative and toxic characteristics, which can have far-reaching impacts on water environments, soil, and even human health. Dammel et al. from EMD Electronics, a business unit of Merck Group in North America, reviewed the status of PFAS in the semiconductor photolithography field. Common fluorinated chemicals used in the semiconductor photolithography field, including trifluromethanesulfonic acid, perfluorobutane sulfonic acid, fluorine-containing photosensitive polyimide (PSPI), and fluorine-containing photosensitive benzoxazole (PSPBO), are all classified as PFAS substances.
FPI engineering plastics have broad application prospects in national defense modernization and civilian high-tech fields. Currently, the FPI engineering plastics used in the defense sector are unlikely to be affected by the PFAS restrictions in the short term. However, FPI engineering plastics used in civilian high-tech sectors, such as low-dielectric engineering plastics for 5G base station construction, low-dielectric antenna components for smartphones, and various smart modules for infrared transmission, may be impacted by the PFAS restriction order. At present, many uses of materials containing PFAS do not have known substitutes. Furthermore, even if substitute materials are developed, they must undergo rigorous process validation before entering mass production stages, eventually becoming viable alternatives. In some cases, after years of research, it might be found that substitutes without PFAS cannot provide the required chemical functions. Nevertheless, the development of alternative materials for FPI-type engineering plastics in civilian applications should receive close attention from both academia and industry.
FPI engineering plastics generally combine the excellent comprehensive properties of PI materials and fluoroplastics, thus after years of development, they have become an important member of the special engineering plastics family. In addition to the increasing application demands in special fields such as aviation, aerospace, and weaponry, many civilian high-tech sectors like telecommunications, optoelectronics, and energy are also increasingly using FPI engineering plastics for their critical components. The future development trends of FPI engineering plastics mainly focus on the following aspects: (1) Integration of structure and function. Fluorination typically endows PI engineering plastics with superior heat and oxidation stability, high insulation, low dielectric constant, and low hygroscopicity. Future research should concentrate on how to design molecular structures to imbue FPI engineering plastics with unique functionalities and how to develop organic-inorganic composite FPI engineering plastics through compositional design. (2) Cost reduction. The fluorine-containing monomers used in preparing FPI engineering plastics often come at a high cost; hence, optimizing the synthesis and purification processes of these monomers to increase their yield and purity is an important research topic for reducing the overall cost of FPI engineering plastics. (3) Environmental friendliness. Although current PFAS restrictions have not yet impacted FPI engineering plastics, it is advisable to start seeking PFAS-free solutions, especially for civilian applications, as a precautionary measure.
【Copyright and Disclaimer】The above information is collected and organized by PlastMatch. The copyright belongs to the original author. This article is reprinted for the purpose of providing more information, and it does not imply that PlastMatch endorses the views expressed in the article or guarantees its accuracy. If there are any errors in the source attribution or if your legitimate rights have been infringed, please contact us, and we will promptly correct or remove the content. If other media, websites, or individuals use the aforementioned content, they must clearly indicate the original source and origin of the work and assume legal responsibility on their own.
Most Popular
-
Covestro faces force majeure!
-
Breaking News! Mitsui Chemicals TDI Unit in Japan Experiences Chlorine Gas Leak Accident!
-
Mitsubishi Chemical Exits! Sumitomo Acquires!
-
DuPont plans to sell Nomex and Kevlar brands for $2 billion! Covestro Declares Force Majeure on TDI / oTDA-based / Polyether Polyol; GAC Group Enters UK Market
-
Borealis suspends polyolefin recycling plant in Austria, Hyundai achieves record Q2 revenue, Volkswagen lowers performance expectations