Professor Wang Chao's 16-Year Quest: Degradable Rubber Achieves Industrial Breakthrough in Guangdong!
The world's first thousand-ton biobased rubber pilot line will go into production by 2025. Wang Chao stated, "We hope that shoes made from our degradable rubber can be worn by consumers this year." Making shoes is not the core competence of scientists, but without these shoes, it would be difficult to break through the bottleneck of industrialization.
On March 25, the Yangcheng Evening News reported that when the Qingshan Science and Technology Award was presented to scientists from Guangdong universities for the first time, Professor Wang Chaozheng from South China University of Technology stood in the pilot workshop of the Huangpu Green Advanced Materials Technology Research Institute. The achievement of bio-based biodegradable rubber embodies nearly 20 years of effort from him and his team: starting from his doctoral period participating in the development of the world's first bio-based elastomer, to the upcoming establishment of the world's first pilot line with a capacity of a thousand tons by 2025, from the soon-to-be mass-produced biodegradable shoe soles to the vision of solving the annual pollution of 6 million tons of tire wear, Wang and his team's research has long since stepped out of the laboratory and into the Bay Area industrial cluster.
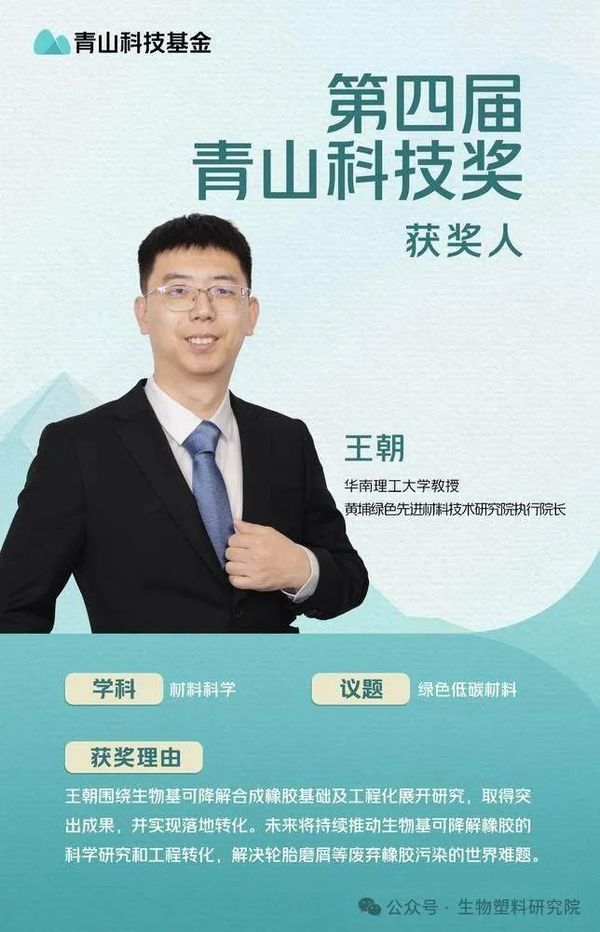
In early March 2025, the list of winners for the fourth Qingshan Technology Award was officially announced, with 10 young scientists in the fields of green and low-carbon technologies, including Wang Chao, being selected. Each winner will receive a post-tax prize of 1 million yuan, to be used at their discretion.
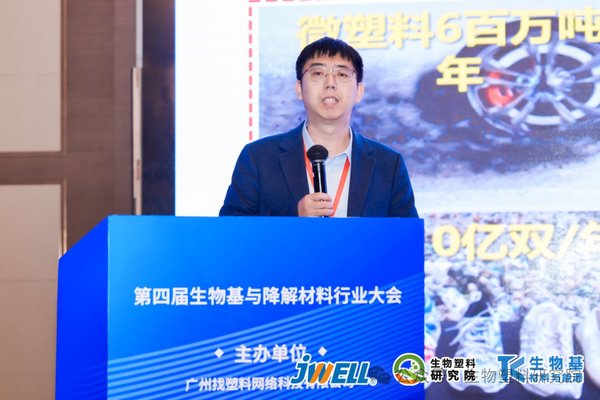
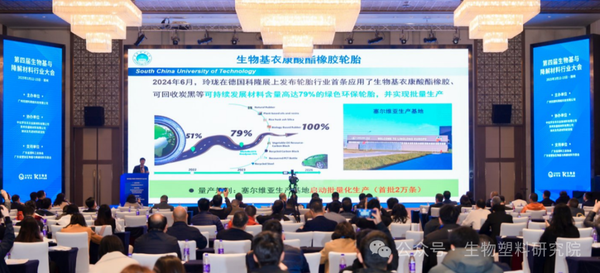
Professor Wang Chao gave a speech at the Fourth Biobased and Degradable Materials Industry Conference.
"Green Long March Starting from the Individual"
On Professor Wang Chao's desk lies a pair of sports shoes produced in 2022. These seemingly ordinary sports shoes are made with biodegradable rubber in their soles, which originally comes from common everyday materials like potatoes and corn. This achievement is the result of nearly 20 years of effort from the research team.
This research direction stems from the pollution caused by wear debris from traditional rubber products such as tires. These particles seep into soil, groundwater, lakes, and seas, and some are even ingested by fish, ultimately entering the human body. Academic articles have reported the presence of microplastics in human placenta and brains. If degradable rubber could be developed, the resulting wear particles would not turn into microplastics that contaminate soil and water sources.
"I have been working in this field for 16 years myself," Wang Chao said. In 2008, Wang Chao's mentor, Zhang Liqun, first proposed the concept of bio-based engineering elastomers on an international level, aiming to develop new bio-rubber materials from sources such as potatoes and corn, which could possess the performance required for engineering applications. "At that time, there was still relatively low attention towards renewable resources in China. After my teacher proposed this idea, we embarked on researching this topic."
At that time, the utilization of biomass feedstocks was still in its infancy in China, with little relevant research and technical accumulation. The first-generation product from Wang Chao's team could only use a very limited number of biomass monomers. Afterward, through continuous adjustments and optimizations of formulas, they developed a wider variety of rubbers. "Our team spent nearly a decade on this work, conducting basic research in the laboratory."
In the process of working diligently in the laboratory, Wang Chao gradually realized the disconnect between basic research and market demands, and began to change his approach to align more closely with market needs. "For example, if there is a market demand for oil-resistant rubber, we would then construct new molecular structures based on this need, figuring out how to make it more oil-resistant and more cold-resistant." However, even after a decade of R&D, the results still have a long way to go before actual production can begin.
"The first gap is in production volume." When mentioning this, Wang Chao couldn't help but laugh. "Our lab can produce 50 grams at a time, while the factory trial production line can produce at least several dozen kilograms at once. Based on our production capacity, it would take us two months to accumulate the amount needed for one trial run at the factory. If the trial fails, we would have to start all over again, and such a cost in time is something we cannot afford."
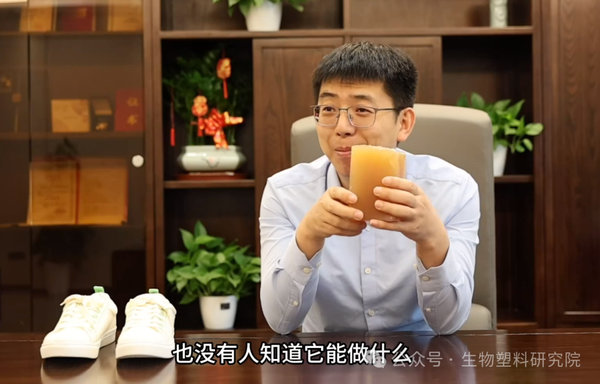
This dilemma arises from the significant gap between laboratory preparation and industrial production. To address this, Wang Chao's team began tackling the technical challenges of scaling up from small-scale tests to pilot production. They redesigned the reaction apparatus to solve issues such as uneven mixing and overheating during the scale-up process, ultimately establishing a pilot plant capable of producing a hundred tons annually. Subsequently, the team took the adjusted rubber to the factory for trial production, identifying issues and then returning to the lab to optimize the formulation. After nearly a hundred such cycles over three years, Wang Chao's team finally brought biodegradable rubber from the lab to consumers' feet.
The Industrial Leap on the Land of Guangdong
In September 2023, with a pair of biodegradable rubber shoes, Professor Wang Chao traveled from Beijing University of Chemical Technology to Guangzhou, joining South China University of Technology as the Executive Director of the Huangpu Green Advanced Materials Technology Research Institute. This pair of shoes, born in a laboratory in Beijing, is not only the most "valuable" item in his suitcase but also a bridge connecting the laboratory and industrialization.
Guangdong's well-developed manufacturing industry is home to leading enterprises in the fields of rubber and new materials, such as Goldmark Technology and Wanli Tire. The decision to move south is driven by the comprehensive industrial ecosystem in Guangdong. It is hoped that by leveraging the advanced manufacturing base and favorable policy environment in Guangdong, connections with downstream manufacturers can be established to accelerate the application of degradable rubber across various industries.
At that time, Guangdong Province released the "Action Plan for the Development of Strategic Emerging Industries Cluster in Cutting-edge New Materials (2023-2025)", which clarified the significant position of the cutting-edge new materials industry and pointed out that it is the high ground for future industrial development. Under the support of this policy, the Huangpu District government and South China University of Technology jointly established the Huangpu Institute of Green Advanced Materials Technology, focusing on "the development of green advanced materials technology" to foster cutting-edge scientific research technologies such as low carbon, environmental protection, and "chokepoint" technologies.
With the establishment of the research institute, the construction of the world's first kiloton-scale bio-based rubber pilot line is rapidly advancing, and it is scheduled to begin production in 2025. This production line represents not only a breakthrough in capacity but also acts as a "translator" bridging the gap between the laboratory and the factory—through it, the dozens of degradable rubber varieties developed by the team can be quickly validated for their production processes, providing customized solutions for downstream enterprises. "I hope that by 2025, shoes made from our degradable rubber will be on consumers' feet," Wang Chao stated. "Making shoes is not the core responsibility of scientists, but without this product, we cannot break through the bottleneck of industrialization." In his view, shoes are the first industry where degradable rubber can be applied on an industrial scale. Apart from shoes, other areas such as oil-resistant seals, children's rubber toys, chewing gum, disposable gloves, and even biomedical materials—all fields that use rubber—are potential areas where degradable rubber can be further explored.
"The current biggest vision is to apply biodegradable rubber to tires," Wang Chao said. During driving, cars produce tire wear particles at the micron level, which are an important component of PM2.5. The smaller the particles, the greater the harm they cause. These micron-sized particles can enter the soil and rivers, eventually making their way into the human body through the food chain. However, if the rubber used for tires is biodegradable, its harmfulness is significantly reduced. "This is the highest level of difficulty because tires have very high performance and safety requirements, and the market validation period is also very long." Once this vision is realized, the issue of tire wear pollution will ultimately be resolved.
Jointly Developing Questions: The Mutual Pursuit of Research and the Market
Research in materials science is never accomplished overnight. From fundamental theoretical research, laboratory synthesis, performance testing, to pilot production and finally industrialization, each stage requires a significant amount of time, effort, and resources, often accompanied by countless failures and repeated experiments. Professor Wang sighed, "The bio-based biodegradable rubber we are working on is a world first; there are no references in the literature, nor are there comparable products in the market, so the time invested is naturally very long."
This lengthy R&D cycle made Wang Chao deeply realize the importance of integrating industry, academia, and research. "There is a natural 'translation gap' between university research and industrial needs." For laboratory results to truly take root, "university teachers should visit enterprises more often, and enterprises should strengthen their cooperation with universities."
Wang Chao quoted his mentor Zhang Liqun to elaborate further: “It is not the enterprises giving topics to universities, nor universities giving topics to enterprises, but both sides jointly proposing and answering the questions.” In this model, enterprises provide timely feedback on process requirements and market demands, allowing universities to optimize their research directions, ultimately achieving "mutual benefits." He used the example of biodegradable rubber research: "Without close cooperation with shoe companies, we might still be researching molecular structures in the laboratory, struggling to solve various issues such as wear resistance, comfort, and slip resistance."
Wang Chao felt very honored to receive the Qingshan Technology Award. "When the first Qingshan Technology Award started accepting applications, some friends encouraged me to apply, but at that time I was busy tackling the industrialization challenges of biodegradable rubber and did not apply for the award." It was only after gaining a deeper understanding that he realized the unique value of this award: "It not only responds to the country's significant needs for carbon neutrality and environmental protection, but also provides valuable support for researchers."
The "Qingshan Science and Technology Award," initiated by Meituan in 2021, is a public welfare award that funds young scientists. In early March 2025, the list of winners for the fourth Qingshan Science and Technology Award was officially announced, including 10 young scientists in the field of green and low-carbon technology, among whom is Wang Chao. Each winner will receive a post-tax prize of 1 million yuan, which they can use at their discretion.
"The support from the QingShan Science and Technology Award allows us to devote more energy to research." Wang Chao said. Now, standing at a new starting point, he is more determined than ever to focus on the transformation of scientific research results, making them serve people's green lifestyle.
【Copyright and Disclaimer】The above information is collected and organized by PlastMatch. The copyright belongs to the original author. This article is reprinted for the purpose of providing more information, and it does not imply that PlastMatch endorses the views expressed in the article or guarantees its accuracy. If there are any errors in the source attribution or if your legitimate rights have been infringed, please contact us, and we will promptly correct or remove the content. If other media, websites, or individuals use the aforementioned content, they must clearly indicate the original source and origin of the work and assume legal responsibility on their own.
Most Popular
-
Covestro faces force majeure!
-
Breaking News! Mitsui Chemicals TDI Unit in Japan Experiences Chlorine Gas Leak Accident!
-
DuPont plans to sell Nomex and Kevlar brands for $2 billion! Covestro Declares Force Majeure on TDI / oTDA-based / Polyether Polyol; GAC Group Enters UK Market
-
Mitsubishi Chemical Exits! Sumitomo Acquires!
-
Borealis suspends polyolefin recycling plant in Austria, Hyundai achieves record Q2 revenue, Volkswagen lowers performance expectations