Lanzhou Petrochemical: The Terminator of Imported Raw Materials for Polyethylene Ampoules
The transformation journey of ampoules has undergone breakthroughs from hard glass to soft polyethylene, and a shift from black petroleum to white ethylene. Turning the hard into soft, the black into white, and then making the white liquid into granules smaller than a mung bean, each leap forward requires a focused effort to tackle core technological challenges.
Facing an unprecedented situation, the people of Lanzhou Petrochemical once bravely calculated a sum: if they used the tubular method to polymerize ethylene into polyethylene under high pressure, just overcoming the high-pressure barrier would present enormous challenges, and if they failed, it would result in significant losses.
"Standing against the waves, the pioneers are forging ahead. In this place, known as the 'cradle' of the petrochemical industry in New China, the 'sand furnace' spirit of self-improvement was cultivated under conditions of extreme poverty. From the initial establishment of the sand furnace ethylene cracking unit to the current annual ethylene production capacity exceeding one million tons, the cultural confidence of the Lanzhou Petrochemical people drives them to strive for new achievements and quality upgrades, uniting their efforts as they embark on a new journey."
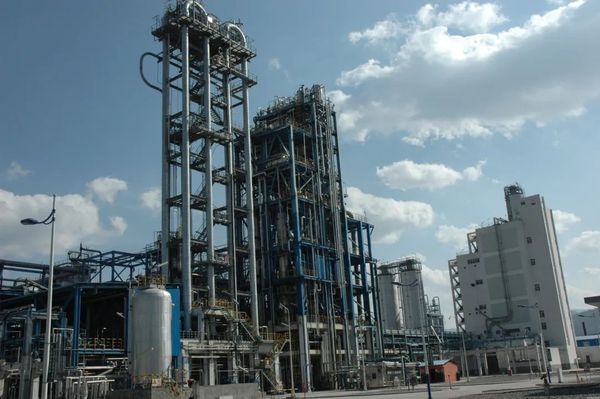
Ethylene plant polypropylene unit (Lanzhou Petrochemical provided the image)
Starting from planning in 2010, Lanzhou Petrochemical Company has undergone 8 years of hard work. Focusing on oil as the foundation and leveraging its strengths in oil, it successfully produced polyethylene LD26D material in 2017, suitable for manufacturing ampoules for injectable solutions. This broke the monopoly of imported materials in China's medical polyolefin market and freed domestic pharmaceutical packaging materials from reliance on imported polyolefin raw materials, ushering in a new era of domestic production for polyethylene ampoules for injection.
Break the pressure "ceiling" in the chemical industry.
What seems ordinary is the most extraordinary; what appears easy is actually difficult.
Breakthroughs in basic research and original innovation require the persistence of holding on tightly to a goal, the determination to sit steadily on the "cold bench," and the resilience to keep striving until the objective is achieved.
The world's earliest polyethylene was first synthesized by the British ICI company in 1922. In 1933, the British company Dunlop discovered that ethylene could polymerize under high pressure to produce polyethylene. This method was industrialized in 1939 and is commonly known as the high-pressure method. Approximately two-thirds of the total polyethylene produced today comes from this method.
Lanzhou Petrochemical Company has overcome the production process of polyethylene LD26D material for injection vial ampoules, mainly using the high-pressure tubular method. At the beginning of 2011, when the production verification of polyethylene LD26D material was just initiated, the development and production team encountered three major difficulties and challenges: high density, low index, and high cleanliness.
Team members found that achieving high density means the production of polyethylene reactors must reach a pressure of 280 megapascals, which is equivalent to 2800 kilograms in simple terms. This pressure is the "ceiling" in the chemical industry, representing the highest pressure for producing chemical products in the world. There have been no such production attempts or precedents in our country.
How great is a pressure of 2800 kilograms? Team member Sun Jianmin carefully calculated: 1 kilogram of pressure is equivalent to 736 millimeters of mercury column, which converts to a water column of 10 meters deep. Therefore, a pressure of 2800 kilograms is equivalent to a pressure from a water depth of 28,000 meters. In comparison, the pressure in a common household pressure cooker is generally only 3 to 4 kilograms.
However, this is not the most challenging pressure. As a chemical production enterprise, safety is the premise of everything. If the 2800-kilogram reactor leaks, it could cause an explosion of seismic proportions.
The team launched a research and development trial with a reactor that produces 2600 kilograms of pressure. As the team expected, the reactor's compressor experienced two leaks in succession. After communicating with the manufacturer, it was found to be a sealing issue. The problem was resolved by modifying the compressor's sealing components.
In addition, the requirements for the polyethylene LD26D medical grade material are strict, and the high pressure in the reactor poses a significant challenge to the operation of the secondary compressor process and the equipment's operation.
During the operation of the equipment, the temperature of the two-stage eight cylinders of the secondary compressor, especially the vibration of the plunger, has very high requirements for the operation of the equipment.
Afterwards, team members found that the oiling parameter equipment manufacturer only provided a rough range, and to obtain precise parameters, further exploration was needed. This opened up a way to master a series of optimal parameters for the equipment under high pressure.
Crossing the gap will inevitably lead to a broad and clear view.
Yao Yi, who is responsible for equipment management and maintenance, has a deeper understanding of this. In his view, during the testing period, it is not easy for a Swiss-imported ultra-high-pressure reciprocating compressor to operate steadily at a pressure of 2800 kilograms. Through years of practical experience, the team has mastered the precise parameters for equipment operation under high pressure, resulting in fewer alarm occurrences and a more composed response.
Medical material smaller than mung bean grains.
The second major characteristic of polyethylene production is its index is low. It is the number of grams of polyethylene passing through a standard diameter in 10 minutes at a certain temperature.
In the tubular method of polyethylene production, molten polyethylene is produced under high temperature and high pressure. Ethylene is then separated out through a high-pressure separator and a low-pressure separator. The material then enters an extruder and pelletizer to form pellets, which are dehydrated and sent to a degassing chamber. A degassing fan cleans the pellets of any ethylene content before they enter the finished product warehouse. After analysis and passing inspection, a quality inspection certificate is issued, and the material can be used as a raw material for medical devices, packaged, and shipped.
Before entering the extruder, the polyethylene in a molten state has a low viscosity for two reasons: first, in the overall reaction, the polyethylene flows in a molten state, and the flowability is poor, which makes it prone to wall sticking and adhesion in the reactor; second, the power and current of the extruder are high, which can cause damage to the entire extruder.
It's just like the power of a lion is great, but it can be very difficult to subdue a mosquito in front of it.
After the precise parameters were determined, team leader Jia Quanyou and his colleagues stared intently at the materials. Each time they mixed, they took a sample to analyze whether it was between 0.24 grams and 0.36 grams.
In the cutting granulation process, team members initially used manual cutting and timed it with a stopwatch. At first, the output was not used; after cutting a few samples, they weighed them to see if they met the standards, recorded the cutting time, and noted the amount produced, then calculated an average value.
It has been calculated that each pure white and transparent polyethylene pellet has a volume of 1 cubic centimeter, weighs between 0.923 grams and 0.929 grams, has an outer diameter of 3 millimeters, and a thickness of 2 millimeters, making it even smaller than a mung bean.
The development and production team of Lanzhou Petrochemical's polyethylene medical materials has higher cleanliness requirements for the polyethylene LD26D medical material. As a raw material for packaging pharmaceutical liquids, its standards are comparable to food-grade.
To avoid the impact of impurities and dust on the materials, the research team conducted a comprehensive inspection of the production line's material reception, desalinated water, air supply for material conveying, and raw material filters during the experimental phase. Both water and air underwent precise filtration, ensuring that the environment for the company's medical packaging products meets the C+D national medical device packaging standards.
In line with the concept of long-term transformation, the team has been implementing continuous optimization measures while parking, including the purification transformation of the conveying system, the desalination water transformation, and the modification of the ethylene filter and peroxide eliminator, all of which are ongoing efforts to refine and improve.
Where exactly is the problem? After investigation, it was found that impurities would fall off at the weld points of the pipeline during the degassing process. Upon discovering the issue, the research team not only felt no discouragement but instead became invigorated.
Due to the initial conditions at that time, He Pinglin and his colleagues used hand-held grinding wheels to grind, polish, and smooth the weld points until there were no protruding welds. After grinding, they also used a vacuum cleaner to remove any impurities.
"We are still not at ease," He Pinglin said. To further improve the cleanliness of the pipelines and eliminate the appearance of polyethylene colored particles, he and his colleagues came up with the most traditional method—using their hands to knead dough and then applying it again, so that the pipelines would be particularly clean.
The unwavering ideals and beliefs of the Lanzhou Petrochemical people, their pioneering spirit of daring to take new paths, their spirit of dedication, and their entrepreneurial spirit of striving for progress have all generated powerful strength in the research and development of polyethylene LD26D medical materials, driving them to overcome challenges and achieve breakthroughs.
In response to the lack of a comprehensive risk assessment method for high-risk pharmaceutical polyolefin packaging materials in China, with the support of the National Medical Products Administration, Lanzhou Petrochemical, in collaboration with experts from the National Medical Products Administration, the Institute of Disease Prevention and Control of the Academy of Military Medical Sciences, the Toxicological Evaluation Research Center, the National Beijing Drug Safety Evaluation Center, and the Chinese Academy of Environmental Sciences, has held multiple technical seminars. They have integrated and developed a safety evaluation system that includes 21 tests in biology, toxicology, and other areas, achieving full coverage of relevant technologies in the pharmacopoeias of the United States, Europe, and Japan.
To ensure the quality certification of injection-grade polyethylene LD26D material, a medical material certification system is being established to form a national standard. Lanzhou Petrochemical has continuously invested hundreds of millions of yuan to carry out safety evaluations, with the quality certification of a single sample requiring an investment of 2 million yuan, equivalent to developing a new drug.
At the end of January 2024, the first batch of LD26D products purchased by China Otsuka Pharmaceutical Co., Ltd. from Lanzhou Petrochemical Company underwent in-house testing and external inspection by its QC department, and officially began mass production on two 10-milliliter sodium chloride injection ampoule production lines in early February. As of February 27, over 30 million domestically produced polyethylene medical ampoule products have been put on the market.
Wang Fushan said with joy that in addition to refueling and energy supply, China Petroleum has also crossed into the medical field. Whether it is ampoule bottles for holding liquid medicines or auxiliary materials like vaccine white oil used in the production of inactivated vaccines, China Petroleum can produce them, pioneering a new era of domestically produced related products.
【Copyright and Disclaimer】The above information is collected and organized by PlastMatch. The copyright belongs to the original author. This article is reprinted for the purpose of providing more information, and it does not imply that PlastMatch endorses the views expressed in the article or guarantees its accuracy. If there are any errors in the source attribution or if your legitimate rights have been infringed, please contact us, and we will promptly correct or remove the content. If other media, websites, or individuals use the aforementioned content, they must clearly indicate the original source and origin of the work and assume legal responsibility on their own.
Most Popular
-
Covestro faces force majeure!
-
Breaking News! Mitsui Chemicals TDI Unit in Japan Experiences Chlorine Gas Leak Accident!
-
Mitsubishi Chemical Exits! Sumitomo Acquires!
-
DuPont plans to sell Nomex and Kevlar brands for $2 billion! Covestro Declares Force Majeure on TDI / oTDA-based / Polyether Polyol; GAC Group Enters UK Market
-
Borealis suspends polyolefin recycling plant in Austria, Hyundai achieves record Q2 revenue, Volkswagen lowers performance expectations