Koya Dynamics | "Plastic Replacing Steel" Leads the Lightweight Trend, PEEK Material Has Broad Prospects
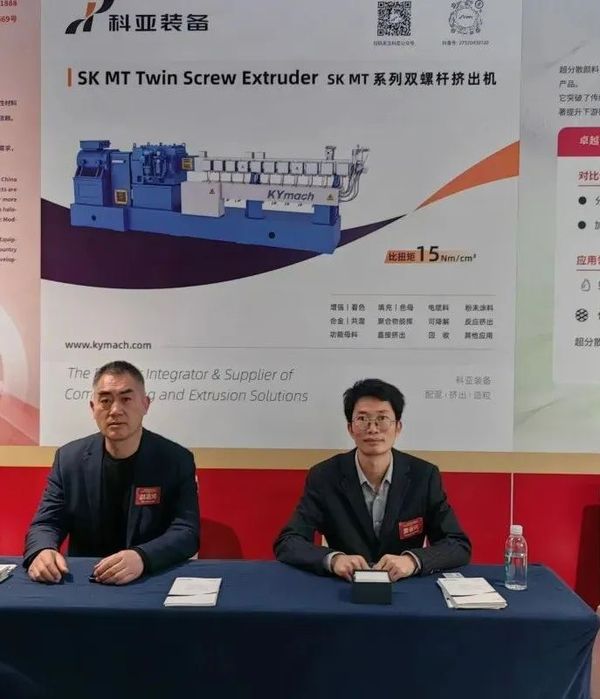
On February 28, 2025, the 10th Second Member Representative Conference and the 10th Expanded Second Council Meeting of Shenzhen Polymer Industry Association were grandly held at the Pullman Hotel in Shenzhen. Zhao Zhiming (left), the COO of Keya Equipment, and Huang Guxing (right), the sales director of the Southern Platform, were invited to attend and discuss the development and future of polymer materials with industry peers.
On February 28, 2025, the 10th Second Member Representative Conference and the 10th Expanded Second Council Meeting of Shenzhen Polymer Industry Association were grandly held at the Pullman Hotel in Shenzhen. Zhao Zhiming (left), the COO of Keya Equipment, and Huang Guxing (right), the sales director of the Southern Platform, were invited to attend and discuss the development and future of polymer materials with industry peers.As the sales head of Koya Equipment's southern platform, Huang Guxing graduated from Beijing University of Chemical Technology and has over 12 years of experience in the twin-screw extruder industry. Based in Guangzhou, Guangdong Province, he has in-depth research and rich practical experience with engineering plastic modification materials such as PEEK and silicone rubber.
As the sales head of Koya Equipment's southern platform, Huang Guxing graduated from Beijing University of Chemical Technology and has over 12 years of experience in the twin-screw extruder industry. Based in Guangzhou, Guangdong Province, he has in-depth research and rich practical experience with engineering plastic modification materials such as PEEK and silicone rubber.
As the sales head of Koya Equipment's southern platform, Huang Guxing graduated from Beijing University of Chemical Technology and has over 12 years of experience in the twin-screw extruder industry. Based in Guangzhou, Guangdong Province, he has in-depth research and rich practical experience with engineering plastic modification materials such as PEEK and silicone rubber.
As the sales head of Koya Equipment's southern platform, Huang Guxing graduated from Beijing University of Chemical Technology and has over 12 years of experience in the twin-screw extruder industry. Based in Guangzhou, Guangdong Province, he has in-depth research and rich practical experience with engineering plastic modification materials such as PEEK and silicone rubber.
As the sales head of Koya Equipment's southern platform, Huang Guxing graduated from Beijing University of Chemical Technology and has over 12 years of experience in the twin-screw extruder industry. Based in Guangzhou, Guangdong Province, he has in-depth research and rich practical experience with engineering plastic modification materials such as PEEK and silicone rubber.PEEK Material: The Leader in High-Performance Engineering Plastics
PEEK Material: The Leader in High-Performance Engineering Plastics
PEEK Material: The Leader in High-Performance Engineering Plastics
PEEK Material: The Leader in High-Performance Engineering Plastics
PEEK Material: The Leader in High-Performance Engineering PlasticsPEEK Material: The Leader in High-Performance Engineering PlasticsPolyetheretherketone (PEEK for short) is a special type of engineering plastic. Its molecular structure contains side chains of methyl methacrylate and terephthalic anhydride, featuring a wide molecular weight distribution, high reactivity of side chain groups, and strong conjugation effects. These characteristics enable it to maintain excellent mechanical properties and chemical stability in environments with high temperature, high humidity, and corrosiveness.
Polyetheretherketone (PEEK for short) is a special type of engineering plastic. Its molecular structure contains side chains of methyl methacrylate and terephthalic anhydride, featuring a wide molecular weight distribution, high reactivity of side chain groups, and strong conjugation effects. These characteristics enable it to maintain excellent mechanical properties and chemical stability in environments with high temperature, high humidity, and corrosiveness.
Polyetheretherketone (PEEK for short) is a special type of engineering plastic. Its molecular structure contains side chains of methyl methacrylate and terephthalic anhydride, featuring a wide molecular weight distribution, high reactivity of side chain groups, and strong conjugation effects. These characteristics enable it to maintain excellent mechanical properties and chemical stability in environments with high temperature, high humidity, and corrosiveness.The upstream industry chain of PEEK material involves the chemical raw materials and chemical fiber manufacturing industries, while downstream it is widely applied in fields such as transportation, aerospace, electronic information, energy and industry, and healthcare. Particularly in the robotics field, with the increasing demand for weight reduction in humanoid robots, PEEK material, thanks to its excellent lightweight characteristics, demonstrates significant application potential. Through structural optimization design, selection of lightweight materials, and advanced manufacturing processes, PEEK material can significantly reduce the weight of robotic components while ensuring the advancement, stability, and safety of the robot's functions.
The upstream industry chain of PEEK material involves the chemical raw materials and chemical fiber manufacturing industries, while downstream it is widely applied in fields such as transportation, aerospace, electronic information, energy and industry, and healthcare. Particularly in the robotics field, with the increasing demand for weight reduction in humanoid robots, PEEK material, thanks to its excellent lightweight characteristics, demonstrates significant application potential. Through structural optimization design, selection of lightweight materials, and advanced manufacturing processes, PEEK material can significantly reduce the weight of robotic components while ensuring the advancement, stability, and safety of the robot's functions.
The upstream industry chain of PEEK material involves the chemical raw materials and chemical fiber manufacturing industries, while downstream it is widely applied in fields such as transportation, aerospace, electronic information, energy and industry, and healthcare. Particularly in the robotics field, with the increasing demand for weight reduction in humanoid robots, PEEK material, thanks to its excellent lightweight characteristics, demonstrates significant application potential. Through structural optimization design, selection of lightweight materials, and advanced manufacturing processes, PEEK material can significantly reduce the weight of robotic components while ensuring the advancement, stability, and safety of the robot's functions.Keya Equipment: Technological Innovation Boosts PEEK Material Development
Koya Equipment: Technological Innovation Boosts PEEK Material Development
Koya Equipment: Technological Innovation Boosts PEEK Material Development
Koya Equipment: Technological Innovation Boosts PEEK Material Development
Koya Equipment: Technological Innovation Boosts PEEK Material DevelopmentKoya Equipment: Technological Innovation Boosts PEEK Material DevelopmentThe HKV polymer reaction type deep groove twin-screw extruder produced by Keya Equipment, based on a screw Do/Di=1.8 design, has increased the free volume by 35% compared to conventional models, and the residence time of materials in the equipment has been increased by 40%. This design provides a wider operating window for polymerization reactions and devolatilization processes, enabling efficient devolatilization of volatiles in the range of 1% to 80%.
The HKV polymer reaction type deep groove twin-screw extruder produced by Keya Equipment, based on a screw Do/Di=1.8 design, has increased the free volume by 35% compared to conventional models, and the residence time of materials in the equipment has been increased by 40%. This design provides a wider operating window for polymerization reactions and devolatilization processes, enabling efficient devolatilization of volatiles in the range of 1% to 80%.
The HKV polymer reaction type deep groove twin-screw extruder produced by Keya Equipment, based on a screw Do/Di=1.8 design, has increased the free volume by 35% compared to conventional models, and the residence time of materials in the equipment has been increased by 40%. This design provides a wider operating window for polymerization reactions and devolatilization processes, enabling efficient devolatilization of volatiles in the range of 1% to 80%.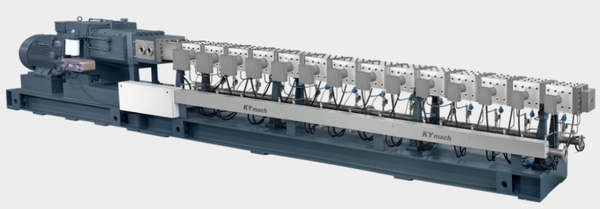
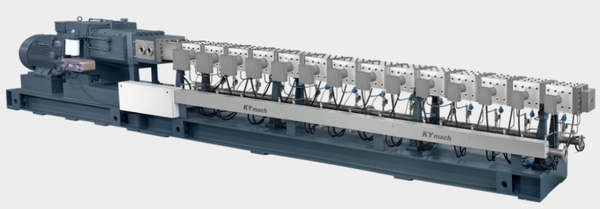
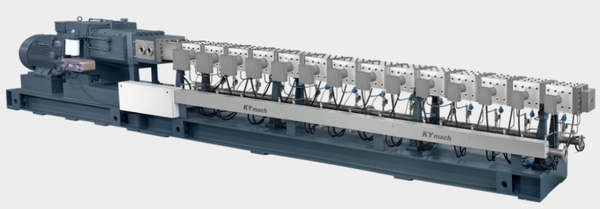
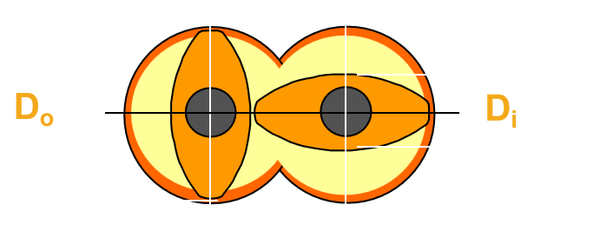
Do / Di = Major diameter of the screw sleeve / Minor diameter of the screw sleeve
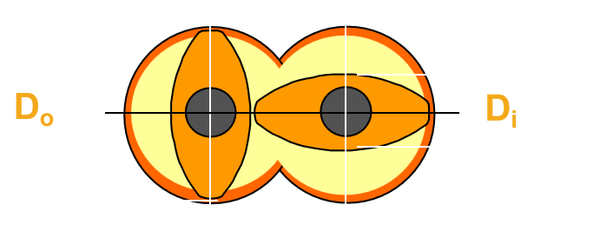
Do / Di = Major diameter of the insert / Minor diameter of the insert
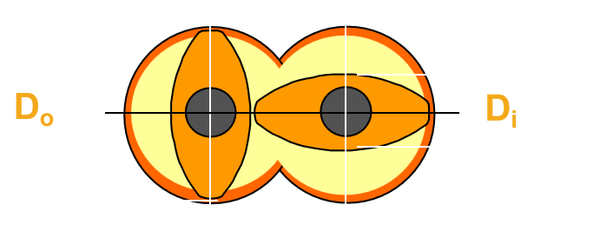
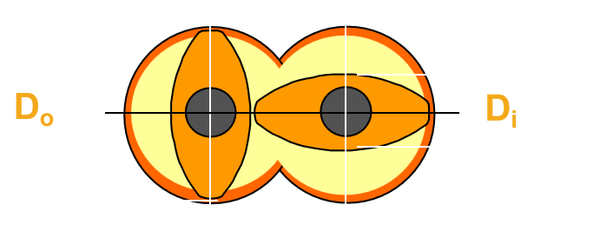
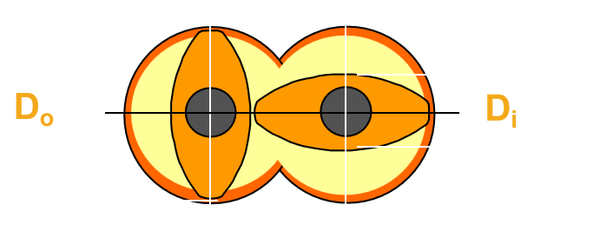
Do / Di = Major diameter of the insert / Minor diameter of the insert
Do / Di = Major diameter of the insert / Minor diameter of the insert
Do / Di = Major diameter of the insert / Minor diameter of the insertIn the extruder process, a higher torque factor is not necessarily better. Through in-depth research, Koah Equipment found that although extruders with high torque factors have higher screw fill rates and production capacity, as well as lower specific mechanical energy, they may also have adverse effects on mixing quality and devolatilization efficiency. Therefore, in equipment design, Koah Equipment focuses on balancing the torque factor with process requirements to ensure that products can still maintain excellent mixing quality and devolatilization efficiency under conditions of low shear rate and low-temperature melting.
In the extruder process, a higher torque factor is not necessarily better. Through in-depth research, Koah Equipment found that although extruders with high torque factors have higher screw fill rates and production capacity, as well as lower specific mechanical energy, they may also have adverse effects on mixing quality and devolatilization efficiency. Therefore, in equipment design, Koah Equipment focuses on balancing the torque factor with process requirements to ensure that products can still maintain excellent mixing quality and devolatilization efficiency under conditions of low shear rate and low-temperature melting.
In the extruder process, a higher torque factor is not necessarily better. Through in-depth research, Koah Equipment found that although extruders with high torque factors have higher screw fill rates and production capacity, as well as lower specific mechanical energy, they may also have adverse effects on mixing quality and devolatilization efficiency. Therefore, in equipment design, Koah Equipment focuses on balancing the torque factor with process requirements to ensure that products can still maintain excellent mixing quality and devolatilization efficiency under conditions of low shear rate and low-temperature melting.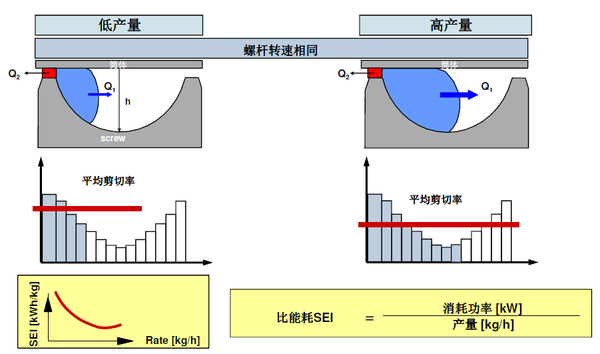
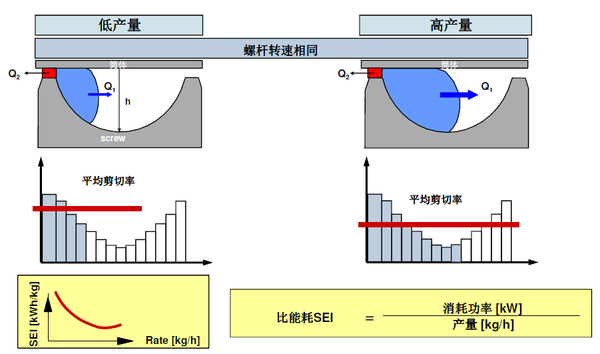
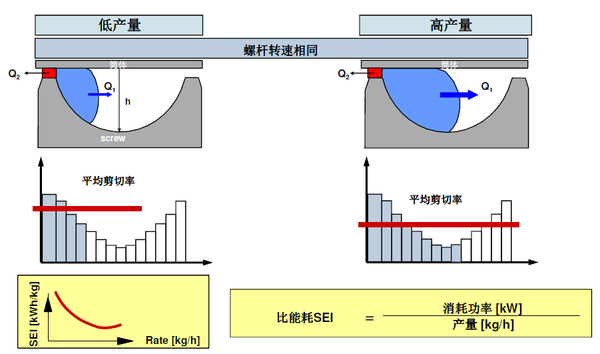
As the trend of "replacing steel with plastic" continues to advance, the position of PEEK material in the field of high-performance engineering plastics will become increasingly important. Koya Equipment will continue to rely on technological innovation and industry experience to provide customers with efficient and reliable solutions, promoting the widespread application of PEEK materials in the field of lightweighting and driving industry development.
As the trend of "replacing steel with plastic" continues to advance, the position of PEEK material in the field of high-performance engineering plastics will become increasingly important. Koya Equipment will continue to rely on technological innovation and industry experience to provide customers with efficient and reliable solutions, promoting the widespread application of PEEK materials in the field of lightweighting and driving industry development.
As the trend of "replacing steel with plastic" continues to advance, the position of PEEK material in the field of high-performance engineering plastics will become increasingly important. Koya Equipment will continue to rely on technological innovation and industry experience to provide customers with efficient and reliable solutions, promoting the widespread application of PEEK materials in the field of lightweighting and driving industry development.【Copyright and Disclaimer】The above information is collected and organized by PlastMatch. The copyright belongs to the original author. This article is reprinted for the purpose of providing more information, and it does not imply that PlastMatch endorses the views expressed in the article or guarantees its accuracy. If there are any errors in the source attribution or if your legitimate rights have been infringed, please contact us, and we will promptly correct or remove the content. If other media, websites, or individuals use the aforementioned content, they must clearly indicate the original source and origin of the work and assume legal responsibility on their own.
Most Popular
-
Covestro faces force majeure!
-
Breaking News! Mitsui Chemicals TDI Unit in Japan Experiences Chlorine Gas Leak Accident!
-
Mitsubishi Chemical Exits! Sumitomo Acquires!
-
DuPont plans to sell Nomex and Kevlar brands for $2 billion! Covestro Declares Force Majeure on TDI / oTDA-based / Polyether Polyol; GAC Group Enters UK Market
-
Borealis suspends polyolefin recycling plant in Austria, Hyundai achieves record Q2 revenue, Volkswagen lowers performance expectations