Investing 5 billion, with a capacity of 500,000 tons, and with a 38% increase in procurement, the regenerative polyester project seizes a market opportunity.
In April 2024, the regeneration polyester new material project with a total investment of 5 billion yuan and an annual production capacity of 500,000 tons officially landed in Huaian Hongze District, Jiangsu Province. This marks a new phase of large-scale application for China's high-value recycling technology for waste textiles. As the world's largest user of fabric scraps, Tiancheng Textile is driving the regeneration fiber industry to new heights through "technology + scale."
The project is divided into two phases, with an investment of 1.1 billion yuan in the first phase, aiming to achieve a production capacity of 100,000 tons by June 2026. The second phase will involve an additional investment of 3.9 billion yuan, ultimately reaching a production capacity of 500,000 tons per year for recycled polyester. Once completed, the project is expected to generate an annual sales revenue of 6 billion yuan and tax revenue of 180 million yuan, contributing to Hongze's goal of establishing a national-level recycled polyester new materials base.
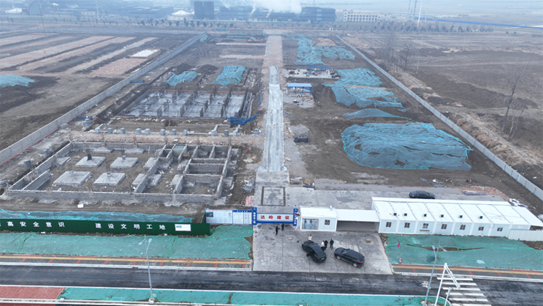
Core Technology Innovation:
Global unique chemical process: Adopting the "chemical semi-degradation PET technology," through processes such as alcoholysis and liquid phase viscosity enhancement, it efficiently regenerates waste textiles while retaining the original fiber color and characteristics, breaking the limitations of traditional physical methods which can only be downcycled.
Full-chain low-carbon advantages: Compared to traditional processes, energy consumption is reduced by 30%, carbon emissions are decreased by 40%, and the fiber's original color is retained without dyeing, significantly reducing water usage and chemical consumption.
Multi-material Collaborative Recycling: Relying on the scientific research team of the national "863 Program," the challenges of multi-fabric separation and multi-material recycling have been overcome, capable of processing waste textiles containing a mixture of cotton, chemical fibers, and other materials.
As the core carrier of Tiancheng Textile's branding strategy, the "Green Silk Can Lay" plan has established a complete closed loop from recycling → sorting → opening → spinning → finished garments.
Front-end layout: A new 178-acre sorting workshop will be built in Hongze, utilizing AI sorting and manual detailed dismantling to process over 200,000 tons of waste textiles annually.
Mid-range efficiency improvement: Adopt intelligent equipment such as German drum dryers and Japanese spinning machines to ensure that the strength of recycled polyester POY filaments reaches over 95% of that of virgin fibers.
Backend application: DTY filaments can be directly used in the production of sportswear and outdoor equipment for partner brands such as Adidas and Uniqlo, forming a value chain upgrade of "waste textiles → regeneration → high-end products."
In February 2024, the supply chain team of a European luxury goods group conducted a special visit to Tiancheng Textile, where they highly praised its physical cotton spinning machinery recycling line and chemical recycling polyester pilot workshop. The group clearly stated that its materials strategy for 2030 requires 40% to use traditional recycled fibers and 25% to use next-generation new materials, while "Green Silk Ke Lai's" chemically recycled polyester fiber, due to its high color restoration and stable physical properties, has become a key cooperation partner.
According to the Textile Exchange 2023 report, the procurement of regenerated materials by global fashion brands is growing at an annual rate of 38%. Tiancheng Textile, with its dual technical matrix of "physical and chemical methods," has established stable supply relationships with over 30 international brands, with regenerated fiber orders scheduled until the end of 2025.
The project is backed by strong scientific research support.
National-level team: Led by core members of the original national "863 Program" regenerated fiber research group, equipped with more than 20 doctoral researchers.
Industry-Academia-Research Collaboration: Establish an academician workstation in partnership with the Chinese Academy of Sciences, focusing on key technologies such as the detection of components in waste textiles and the improvement of catalyst efficiency.
Standard setters: Participated in drafting industry standards such as "Recycled Polyester Filament" and promoted the inclusion of chemically recycled fibers in the international brand procurement whitelist.
It is estimated that China generates over 20 million tons of waste textiles annually, but the recycling rate is less than 20%. With the EU's Waste Directive mandating a 100% recycling rate for textiles by 2030, the landing of Tiancheng Textile's 500,000-ton capacity not only fills the gap in high-end recycled fiber domestically but also drives a trillion-level circular economy market.
Conclusion
From scraps of cloth to high-end recycled polyester, from traditional textiles to green technology, Tiancheng Textile's 500,000-ton project is not just an expansion in capacity but also a technological revolution in the circular economy. As the "dual carbon" goals drive industrial upgrading, this Chinese company's answer proves that sustainability is not a cost, but a competitiveness; waste is not the endpoint, but the starting point of rebirth.
【Copyright and Disclaimer】The above information is collected and organized by PlastMatch. The copyright belongs to the original author. This article is reprinted for the purpose of providing more information, and it does not imply that PlastMatch endorses the views expressed in the article or guarantees its accuracy. If there are any errors in the source attribution or if your legitimate rights have been infringed, please contact us, and we will promptly correct or remove the content. If other media, websites, or individuals use the aforementioned content, they must clearly indicate the original source and origin of the work and assume legal responsibility on their own.
Most Popular
-
Covestro faces force majeure!
-
Breaking News! Mitsui Chemicals TDI Unit in Japan Experiences Chlorine Gas Leak Accident!
-
Mitsubishi Chemical Exits! Sumitomo Acquires!
-
DuPont plans to sell Nomex and Kevlar brands for $2 billion! Covestro Declares Force Majeure on TDI / oTDA-based / Polyether Polyol; GAC Group Enters UK Market
-
Borealis suspends polyolefin recycling plant in Austria, Hyundai achieves record Q2 revenue, Volkswagen lowers performance expectations