Investigation on the Influence of Different Designs of Twin-Screw Extruder Screw Elements on the Mixing Effect of High-Viscosity Polymers
This paper uses finite element software to study the flow field characteristics of high-viscosity polymers in three types of screw elements: conventional screw threads, slotted screw threads, and kneading blocks, and analyzes the impact of different fluid parameters on the mixing performance of these three types of screw elements.
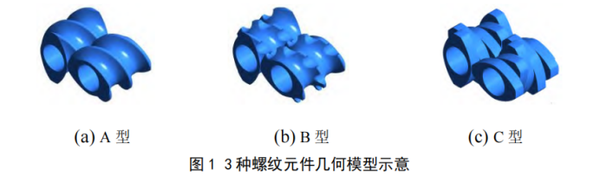
For ease of calculation, the simulation conditions are simplified as follows:
The density of the polymer melt remains unchanged during the mixing process.
2) Neglect the turbulent flow of the melt and only consider laminar flow;
3) Ignore volume forces such as gravity and inertial forces;
The melt is in a completely filled state in the flow channel.
Finite element model: The pre-processing software is used to mesh the flow field and threaded components respectively, as shown in Figure 2 and Figure 3.
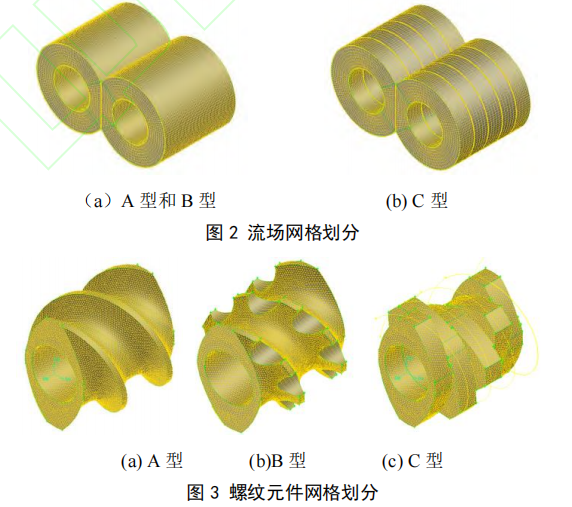
Polymer flow field boundary conditions: both the inlet and outlet of the flow field are in a natural flow state (fn=fs=0). The rotation speed of both the left and right screws is 300 r/min, and there is no relative motion between the inner surface of the barrel.
01
Flow field pressure of threaded components
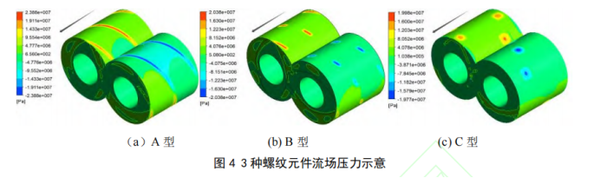
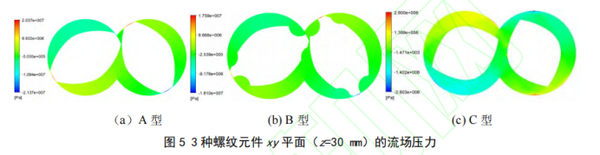
From Figure 4, it can be seen that:
Along the rotation direction of the twin-screw extruder, the pressure near the outlet side of the flow field is relatively high, and the highest pressure in the entire flow field is located in the meshing region between the screw elements. Since the polymer is a non-Newtonian power-law fluid, the melt pressure suddenly increases due to the advancing action of the screw flights. After leaving the screw flights, the pressure gradually decreases. The overall trend is that the pressure gradually increases from the inlet to the outlet. This is because, during the extrusion process, the melt is subjected to a greater propelling force at the screw flights, and the extrusion pressure decreases when leaving the screw flights, but the flow field pressure gradually increases as the melt is continuously mixed and compacted.
In addition, the outlet pressure of the three types of threaded components is greater than the inlet pressure, and the pressure gradient changes significantly, indicating that all three types of threaded components have the ability to build pressure. Type B has eight evenly distributed helical grooves designed on its outer wall, which results in a significant occurrence of leakage and mixing of materials as they pass through the internal cavity. Therefore, the pressure field variation in Type B is relatively small, while the velocity field variation is large, and the local shear rate variation is small.
Peak pressure of the flow field: Type A > Type B > Type C.
02
Local shear rate of threaded elements
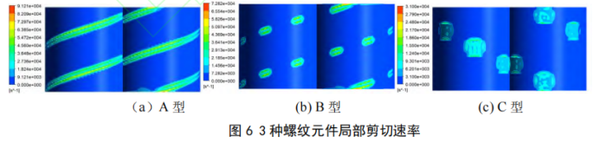
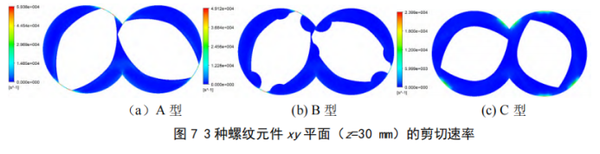
As can be seen from Figures 6 and 7:
High shear stress is mainly concentrated in the meshing area of the two threaded components and between the threaded components and the inner wall of the cylinder.
Along the extrusion direction, the peak local shear rate of type A is the highest, followed by type B, and type C has the lowest.
03
Melt velocity on the thread element plane
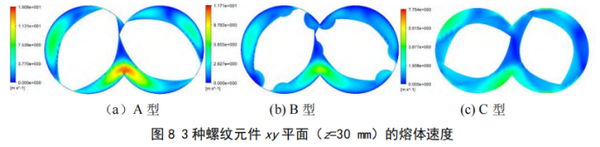
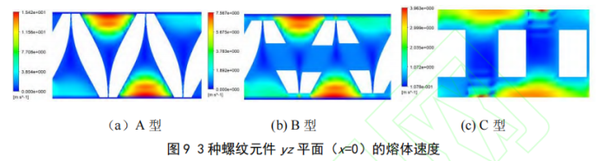
As can be seen from Figures 8 and 9:
The speeds near the flight of all three types of screw elements are relatively high, and the melt velocity suddenly increases in the meshing zone. Near the center of the barrel, the melt exhibits obvious backflow, which facilitates thorough mixing of the melt.
Melt velocity performance: Type A > Type B > Type C.
04
The Effect of Rheological Parameters on Mixing Performance
Select a typical Type A, and analyze the effect of different rheological parameters on the mixing performance. Figure 10 shows the sampling points for the Type A model, where the arrow indicates the extrusion direction, and points A and B are the sampling points. Figure 11 presents the parameter analysis for Type A.
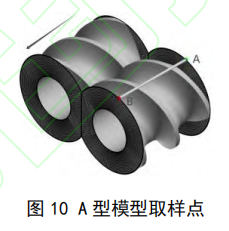
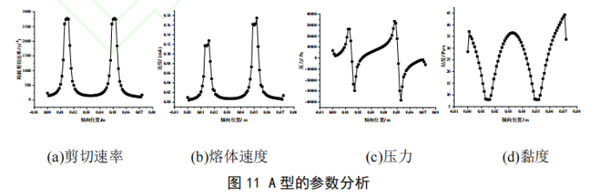
From Figure 11(a), it can be observed that the local shear rate continuously varies with the position of the screw flight and its supporting surface, increasing sharply near the screw flight, while the local shear rate is the smallest at the inlet and outlet of the entire flow field. The local shear rate at the first screw flight supporting surface exceeds 2,750 s⁻¹, and it reaches its minimum value (approaching 0) at the groove position (axial position of 3 cm).
As can be seen from Figure 11(b): When the screw conveys the material to the inlet side, the melt velocity is relatively low. As mixing progresses, the melt velocity gradually increases, exceeding 0.12 m/s at the first screw flight (z=0.015 m). After passing the first screw flight, it rapidly decreases. This is because the material is continuously conveyed forward in a spiral motion inside the twin-screw extruder, experiencing friction between the two screws, which causes the melt velocity to drop sharply. When it approaches zero, it stabilizes. When the material reaches the second screw flight (z=0.05 m), the melt velocity quickly rises to 0.17 m/s, then rapidly declines again and stabilizes.
As shown in Figure 11(c): The pressure change characteristics during the extrusion process have been described above. The trend of pressure change is similar to that of local shear rate and melt velocity, meaning the three are positively correlated. That is, when pressure increases, both the shear rate and melt velocity show an increasing trend.
The shear stress increases with an increase in shear rate, while the viscosity is inversely proportional to both shear stress and shear rate. As can be seen from Figure 11(d), the trend of shear rate is opposite to that of viscosity. When the shear rate decreases, the viscosity tends to increase, and vice versa.
Experimental verification
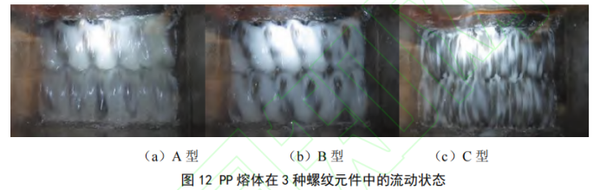
Figure 12 shows the flow state of PP melt in three types of screw elements, with a screw speed of 300 r/min. As can be seen from Figure 12, the PP melt achieves plug flow in all three screw elements, and there is essentially no large material adhesion on the inner wall of the barrel or the screw elements, indicating that all three screw elements have good self-cleaning performance, demonstrating good mixing and shearing effects. Type A has the best shearing capability, followed by Type B, and Type C is the weakest.
In the early stage of the experiment, the designed screw combination only included threaded elements and meshing blocks. Although the overall reaction had good mixing performance and the melt had a high degree of filling inside the barrel, the back-mixing capability was weak.
Through subsequent simulation analysis, the position of the threaded element was adjusted, and a slotted threaded element was added on the side of the engagement block near the feed end, resulting in improved back-mixing capability of the entire flow field.
At the same time, the pressure-bearing capacity and conveying capacity of the grooved threaded element are weak, and the filling degree of materials in the internal flow field is high, which will prolong the residence time. The experimental verification results are highly consistent with the simulation results. In addition, the length-to-diameter ratio of the screw has been reduced from 52:1 to 44:1.
【Copyright and Disclaimer】The above information is collected and organized by PlastMatch. The copyright belongs to the original author. This article is reprinted for the purpose of providing more information, and it does not imply that PlastMatch endorses the views expressed in the article or guarantees its accuracy. If there are any errors in the source attribution or if your legitimate rights have been infringed, please contact us, and we will promptly correct or remove the content. If other media, websites, or individuals use the aforementioned content, they must clearly indicate the original source and origin of the work and assume legal responsibility on their own.
Most Popular
-
Covestro faces force majeure!
-
Breaking News! Mitsui Chemicals TDI Unit in Japan Experiences Chlorine Gas Leak Accident!
-
Mitsubishi Chemical Exits! Sumitomo Acquires!
-
DuPont plans to sell Nomex and Kevlar brands for $2 billion! Covestro Declares Force Majeure on TDI / oTDA-based / Polyether Polyol; GAC Group Enters UK Market
-
Borealis suspends polyolefin recycling plant in Austria, Hyundai achieves record Q2 revenue, Volkswagen lowers performance expectations