Gasification Process! Annual Production of Recycled Carbon Fiber Reaches 160 Tons
Hera Group, based in Bologna, Italy, is a comprehensive utility company engaged in the distribution of natural gas, water, energy, and waste management. Its FIB3R plant, located in Imola, Italy, has been completed and is dedicated to the industrial-scale recycling and regeneration of carbon fiber composite materials. Currently, FIB3R is expected to produce 160 tons of recycled carbon fiber (rCF) annually, saving 75% of the energy compared to virgin fibers.
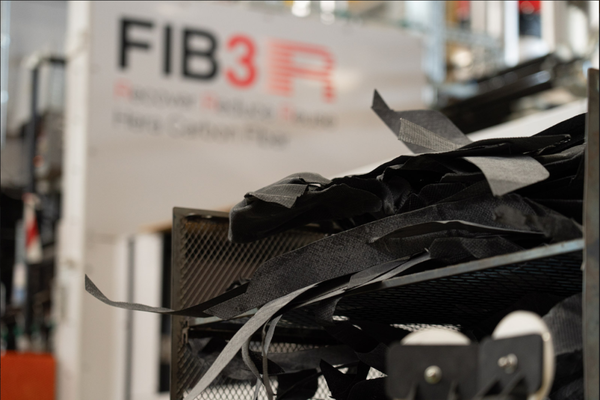
Iacono claims Hella Group owns over 100 advanced factories and five under construction facilities to strengthen its position in the European materials processing and recycling sector. "Our business plan confirms this strategy, 20 billion euros of investment will be made over the 2024-2028 period to create value for all stakeholders."
Herambiente is a subsidiary of the Italian company Group S.p.A. Herambiente is a waste collection and processing operating company, with years of experience in carbon fiber recycling.
Subsequently, Herambiente collaborated with the Department of Industrial Chemistry of the University of Bologna and its technical partner Curti Costruzioni Meccaniche (Ravenna, Italy), a company specialized in the production of automated machinery for industrial applications, which provided its expertise and testing equipment to simulate the formulations being studied.
Hera Group, through its expertise in engineering and waste management, developed this project and built the FIB 3R factory.
FIB 3R heat gasification process
According to HERA Group, the "rebirth" of carbon fiber takes place within a 60-meter-long tunnel. In the first stage of thermolysis – pyrolysis – the carbon fibers are released from the resin. The second stage is gasification, which ultimately forms the regenerated fiber.
The resin decomposed in a gaseous form is reused, generating part of the energy required for the process, thus maximizing energy recovery. The dust remaining in the fibers is vacuumed and sent to the dust removal system. The Hera Group claims that the resulting product after treatment is high-purity carbon fiber, "with all mechanical properties intact."
Due to the high temperatures required and the use of fossil fuels, the typical production of virgin fibers is very energy-intensive. However, life cycle analysis shows that the energy demand for producing rCF is reduced by 75% and avoids 74% of greenhouse gas emissions.
FIB3R also relies on comprehensive traceability of processed materials. In fact, when carbon fiber waste enters the factory, it is contained in bins marked with QR codes, which include the identity of the carbon fiber waste along with information such as technical characteristics, weight, and origin. After processing, these tracked materials will be returned to their owners in the form of rCF, thus creating a closed loop that maximizes sustainability, transparency, and quality.
【Copyright and Disclaimer】The above information is collected and organized by PlastMatch. The copyright belongs to the original author. This article is reprinted for the purpose of providing more information, and it does not imply that PlastMatch endorses the views expressed in the article or guarantees its accuracy. If there are any errors in the source attribution or if your legitimate rights have been infringed, please contact us, and we will promptly correct or remove the content. If other media, websites, or individuals use the aforementioned content, they must clearly indicate the original source and origin of the work and assume legal responsibility on their own.
Most Popular
-
Covestro faces force majeure!
-
Breaking News! Mitsui Chemicals TDI Unit in Japan Experiences Chlorine Gas Leak Accident!
-
Mitsubishi Chemical Exits! Sumitomo Acquires!
-
DuPont plans to sell Nomex and Kevlar brands for $2 billion! Covestro Declares Force Majeure on TDI / oTDA-based / Polyether Polyol; GAC Group Enters UK Market
-
Borealis suspends polyolefin recycling plant in Austria, Hyundai achieves record Q2 revenue, Volkswagen lowers performance expectations