Abstract: Polyetherimide (PEI) microspheres were prepared using the solution reprecipitation method, and the effects of centrifugation speed, centrifugation time, surfactant dosage, and stirring speed on the size and morphology of PEI microspheres were investigated using scanning electron microscopy. Subsequently, tannic acid (TA)-assisted ball milling was employed to prepare TA-modified boron nitride nanosheets (TA-BNNS), which were then assembled with PEI microspheres to fabricate PEI/TA-BNNS hybrid microspheres. Finally, the influence of PEI/TA-BNNS hybrid microspheres on the thermal conductivity of epoxy resin was studied using a laser thermal conductivity meter. The results showed that PEI microspheres with uniform particle size distribution and smooth morphology were obtained when the centrifugation speed was 5,000 r/min, centrifugation time was 30 min, and stirring speed was 500 r/min. Additionally, polyvinyl alcohol (PVAL) surfactant effectively prevented the agglomeration of PEI microspheres, and the largest PEI microspheres were obtained when the mass of PVAL added was twice that of PEI. TA-BNNS prepared by TA-assisted ball milling exhibited excellent water dispersibility, and the PEI/TA-BNNS hybrid microspheres assembled with PEI microspheres could form effective thermal pathways in the epoxy matrix, significantly enhancing the thermal conductivity of the epoxy composite. When 20 wt% hybrid microspheres were added, the thermal conductivity of the epoxy composite reached 0.62 W/(m·K), and the tensile strength of the composite reached a maximum of 69.4 MPa. Both the thermal conductivity and tensile performance were higher than those of epoxy composites with randomly distributed fillers of the same amount.
With the rapid development of semiconductor technology and 5G communication technology, the miniaturization, precision, and functionalization of electronic devices continue to advance, making efficient thermal management of electronic equipment increasingly crucial [1-3]. To enhance the performance, lifespan, and operational reliability of electronic devices, the development of high thermal conductivity electronic packaging materials holds significant theoretical and practical importance [4-5].
Epoxy (EP) resins are lightweight, inexpensive, electrically insulating materials with high mechanical strength and good chemical stability, and they are widely used in the field of electronic encapsulation [6-7]. However, ordinary EP resins have very low intrinsic thermal conductivity and typically require the addition of large amounts of thermally conductive fillers (such as graphene, carbon nanotubes, boron nitride, aluminum oxide, aluminum nitride, etc.) [8-10]. Among these, hexagonal boron nitride (h-BN) is a two-dimensional layered material formed by alternating boron and nitrogen atoms, possessing a honeycomb structure similar to graphene [11-12]. Compared to carbon nanomaterials like graphene, h-BN has a larger bandgap width (5.2 to 5.9 eV), providing excellent electrical insulation, which makes it promising for use in polymer-based thermally conductive insulating composites [13-14]. However, h-BN exhibits extremely high chemical inertness, resulting in poor interfacial compatibility with the polymer matrix. This makes it difficult to uniformly disperse h-BN within the polymer matrix and form effective thermal conduction pathways, leading to higher interfacial thermal resistance and limiting significant improvements in thermal conductivity [15-16]. Additionally, adding a high content of h-BN increases the density of the encapsulation material and significantly affects the mechanical properties of the EP composite material.
In recent years, composite materials based on isolation structures have attracted widespread attention from researchers in various fields such as thermal conductivity, electrical conductivity, and electromagnetic shielding. Among them, in the field of thermal conductive composites, researchers have prepared a series of high thermal conductivity polymer-based composites with isolation structures by attaching high thermal conductivity fillers such as boron nitride, graphene, and carbon nanotubes to the surface of polymer microspheres, followed by further thermal pressing. Studies have found that compared to composites obtained through direct blending, this isolation structure allows the thermal conductive fillers to be densely distributed at the interface between the polymer microspheres, enabling effective regulation of the filler network at low filler content, thus forming a uniform and continuous thermal conduction pathway, significantly improving the thermal conductivity of the polymer materials. For example, Xu et al. prepared polyimide/reduced graphene oxide (PI/r-GO) core-shell hybrid microspheres through in-situ reduction of graphene oxide (GO), and the isolation structure PI/r-GO nanocomposite material exhibited excellent thermal conductivity after thermal pressing, with a thermal conductivity of up to 0.26 W/(m·K) when the mass fraction of r-GO was 2%. Subsequently, Cao et al. combined boron nitride nanosheets (BNNS) on the surface of PI microspheres and prepared a thermally conductive PI/BNNS composite material with a highly ordered BNNS network through thermal pressing, achieving a maximum in-plane thermal conductivity of 4.25 W/(m·K). Although the polymer matrix of the aforementioned isolation structure composites is mainly thermoplastic polymers, the method of attaching thermal conductive fillers to the surface of polymer microspheres to construct an efficient thermal conductive network provides insights for regulating the high thermal conductivity of EP resins: if boron nitride can be combined on the surface of polymer microspheres, the hybrid microspheres added to EP resins are expected to solve the agglomeration problem of boron nitride in EP resins, promote the formation of thermal conduction pathways, and thus achieve significant improvement in the thermal conductivity of EP composites. Currently, there are few reports on using such core-shell hybrid microspheres to regulate the thermal conductivity of EP composites.
To this end, the author prepared polyetherimide (PEI) microspheres using a solution precipitation method, and assembled them with tannic acid (TA) modified boron nitride nanosheets (TA-BNNS) to create PEI/TA-BNNS hybrid microspheres. The structure and morphology of PEI and its hybrid microspheres were studied, and the influence of the hybrid microspheres on the thermal conductivity of EP composites was investigated.
EP resin: industrial grade, Sinopec Baling Petrochemical Co., Ltd.
Curing Agent (C13H14N2): Industrial Grade, Shanghai Macklin Biochemical Technology Co., Ltd.
PEI: 1010, Dongguan Jing Tian Plastic Raw Materials Co., Ltd.
Polyvinyl alcohol (PVAL): 1788, analytical grade, Shanghai Macklin Biochemical Technology Co., Ltd.
h-BN: Industrial grade, Jian'anpu Materials Technology Co., Ltd.
TA: Analytical Grade, Macklin Biochemical Technology Co., Ltd., Shanghai;
Acetone: Analytical reagent, Guangdong Guangshi Reagent Technology Co., Ltd.
N,N-Dimethylacetamide (DMAc): Analytical grade, Tianjin Yongda Chemical Reagent Co., Ltd.
1.2 Main Instruments and Equipment
High power CNC ultrasonic cleaner: KQ-400KDE, Kunshan Ultrasonic Instruments Co., Ltd.
High-speed desktop centrifuge: TG16-WS, Hunan Xiangyi Laboratory Instrument Development Co., Ltd.
Electric Hot Air Oven: WGL-65B, Tianjin Test Instrument Co., Ltd.
Half-round planetary ball mill: BQM-0.4L, Changsha Miqi Instrument Equipment Co., Ltd.
Freeze dryer: SCIENTZ-18N, Ningbo Scientz Biotechnology Co., Ltd.
Field Emission Scanning Electron Microscope (FESEM): SU8010, Hitachi, Japan;
Laser Flash Apparatus: LFA467, NETZSCH GmbH, Germany.
Universal Material Testing Machine: INSTRON-5582, Instron Corporation, USA.
Add 2 g of h-BN, 1.2 g of TA, and 30 g of deionized water into a beaker, and sonicate for 15 minutes. Then, pour the mixture into a ball mill jar and perform ball milling at 400 r/min for 20 hours. Centrifuge the dispersion at 3,000 r/min to remove unexfoliated h-BN. Subsequently, centrifuge the supernatant and wash it 4 times until neutral to remove excess TA. Finally, freeze-dry to obtain TA-modified BNNS (TA-BNNS).
1.3.2 Preparation of PEI/TA-BNNS hybrid microspheres
Add 8 g of PEI to a three-neck flask containing 320 mL of DMAc, and stir at 60 ºC until dissolved. Then, add 16 g of PVAL and continue stirring to dissolve, obtaining a PEI/PVAL/DMAc solution. Meanwhile, add 16 g of PVAL to 320 mL of deionized water, and stir at 60 ºC to dissolve, obtaining a PVAL/H2O precipitate solution. Subsequently, at 60 ºC, slowly add the PVAL/H2O precipitate solution dropwise to the PEI/PVAL/DMAc solution being stirred at 500 r/min. As the precipitate solution is added, the color of the solution gradually turns white, resulting in a PEI microsphere suspension emulsion. After all the precipitate solution has been added, continue stirring at 60 ºC for 2 hours to obtain a milky white dispersion. Finally, centrifuge at 5,000 r/min for 30 minutes, wash with deionized water 4 times, and freeze-dry to obtain PEI microspheres. Disperse the prepared PEI microspheres in deionized water, sonicate evenly, then add TA-BNNS to the PEI microsphere dispersion in proportion. After sonication for uniformity, let it stand to settle, and the product is freeze-dried to obtain PEI/TA-BNNS hybrid microspheres.
The PEI/TA-BNNS hybrid microspheres were ultrasonically dispersed in acetone, while the EP resin was heated in an oven at 80 ºC to make it more fluid. The PEI/TA-BNNS hybrid microspheres were used as fillers and added to the EP resin at mass fractions of 0%, 3%, 5%, 7%, 10%, and 20%. After mechanical stirring for 15 minutes in an oil bath, the curing agent was added and stirred for another 10 minutes. The product was then placed in a vacuum oven for degassing under conditions of 70 ºC for 15 minutes. Finally, it was cured through a stepwise process at 80 ºC/2 h, 120 ºC/2 h, and 150 ºC/2 h.
1.4 Testing and Characterization
The micro morphology of the PEI microspheres, TA-BNNS, and PEI/TA-BNNS hybrid microspheres was analyzed by FESEM at an acceleration voltage of 5 kV.
The thermal conductivity of EP resin composite materials was tested using a laser flash apparatus.
Use a universal material testing machine to test the tensile properties of EP composite materials according to GB/T 1040-2006, with a tensile rate of 5 mm/min.
2.1 Preparation and characterization of PEI microspheres
Figure 1 shows the SEM morphology of PEI microspheres prepared at different centrifugation speeds. The experiment found that when the centrifugation speeds were 8,000 r/min (Figure 1a) and 6,000 r/min (Figure 1b), the sizes of the PEI microspheres were varied. Only at a centrifugation speed of 5,000 r/min (Figure 1c) did the microspheres exhibit the most uniform morphology, with a particle size of up to 3.84 μm. Figure 1d shows the supernatant after centrifugation; it can be seen that there are still some small microspheres with very low dimensions in the supernatant, and some of these small microspheres are embedded by the surrounding PVAL. Therefore, when constructing thermal conduction pathways, only the microspheres with uniform particle size from the precipitate are taken.
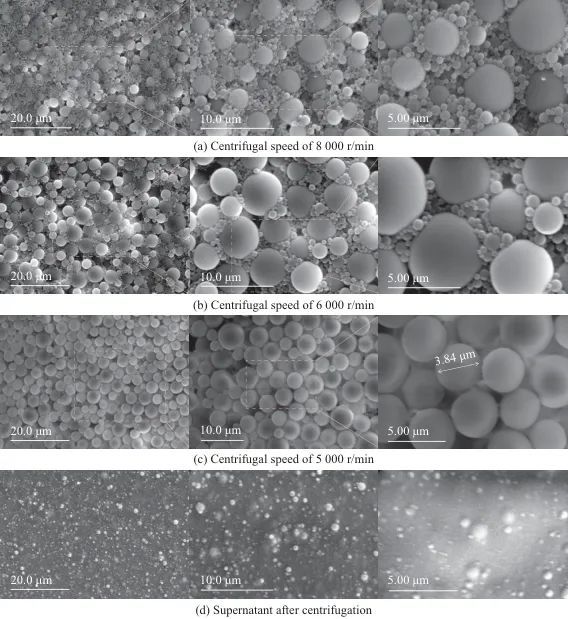
Fig. 1 SEM photos of PEI microspheres under different centrifugation speeds
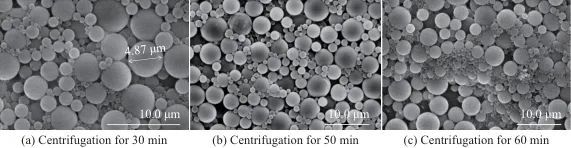
Figure 2 SEM images of PEI microspheres at different centrifugation times
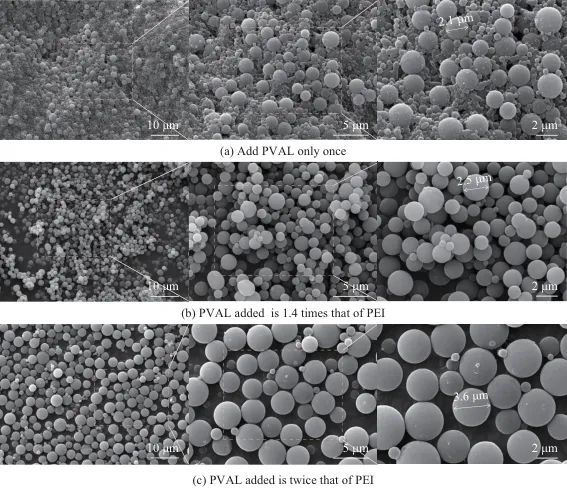
Fig. 3 SEM images of PEI microspheres prepared with different amounts of PVAL
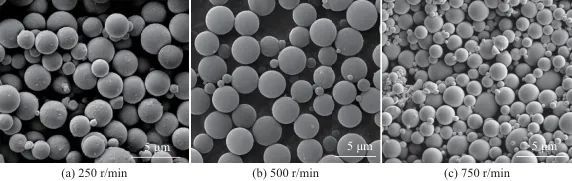
Fig. 4 SEM images of PEI microspheres at different stirring speeds
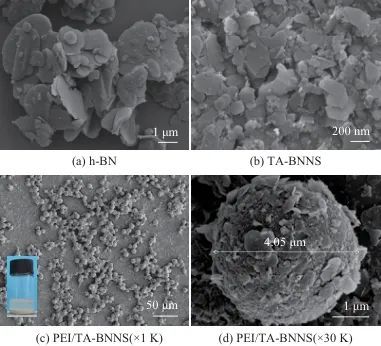
Fig. 5 SEM photos of h-BN, TA-BNNS, and PEI/TA-BNNS hybrid microspheres
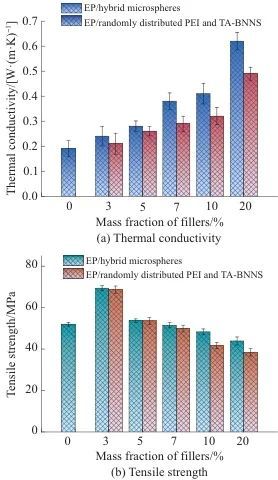
Figure 6 Thermal conductivity and tensile strength of EP composites
At a centrifugal speed of 5,000 r/min, when the centrifugation time was gradually increased from 30 min (Fig. 2a) to 50 min (Fig. 2b) and 60 min (Fig. 2c), numerous microspheres of varying sizes appeared. This was because the prolonged centrifugation time caused even the smaller microspheres to be centrifuged out. Additionally, the study found that controlling the amount of PVAL could regulate the size of the microspheres.
As shown in Figure 3a, when PVAL is added only during the preparation of the PEI solution, the size of the resulting PEI microspheres is about 2.1 μm, and the sizes of the microspheres are inconsistent. When the amount of PVAL added is 1.4 times that of PEI, the size of the obtained microspheres is around 2.5 μm (Figure 3b); when the amount of PVAL is increased to 2 times that of PEI, the size of the prepared microspheres can reach 3.6 μm (Figure 3c), effectively increasing the microsphere diameter and making the microsphere morphology more uniform.
Figure 4 shows SEM images of PEI microspheres prepared at different stirring speeds. If the stirring speed is too low, the distribution concentration of H2O molecules in the DMAc solvent is low, and they cannot diffuse quickly and uniformly. If the stirring speed is too high, the fluid state of PEI/PVAL/DMAc becomes unstable, and PEI may undergo stretching deformation. When the stirring speed is moderate, the diffusion rate of H2O molecules is also moderate, resulting in more regular PEI microsphere morphology. Experiments show that when other conditions remain unchanged, the microspheres obtained at a stirring speed of 250 r/min (Figure 4a) have less uniform morphology compared to those prepared at 500 r/min (Figure 4b). Further increasing the speed leads to a reduction in microsphere size and a broader particle size distribution (Figure 4c).
2.2 Preparation and characterization of TA-BNNS and PEI hybrid microspheres
Using TA-assisted ball milling, h-BN was exfoliated to produce TA-BNNS with good water dispersibility. Figure 5 shows SEM images of h-BN, TA-BNNS, and PEI/TA-BNNS hybrid microspheres. As seen in Figure 5a, the unexfoliated h-BN has a large in-plane size, while the exfoliated TA-BNNS exhibits a significantly reduced in-plane size, presenting a two-dimensional nanosheet structure (Figure 5b). PEI microspheres were ultrasonically dispersed in water, and after adding the TA-BNNS dispersion, TA-BNNS adsorbed onto the surface of the PEI microspheres via hydrogen bonding and π-π interactions, forming a precipitate at the bottom of the bottle, which are the PEI/TA-BNNS hybrid microspheres. Figure 5c displays SEM images of the hybrid microspheres at different magnifications, revealing that TA-BNNS can stably assemble on the surface of PEI microspheres, with the hybrid microspheres reaching a particle size of 4.05 μm.
2.3 The Influence of Hybrid Microspheres on the Properties of EP Composites
PEI/TA-BNNS hybrid microspheres were added to EP resin at mass fractions of 0%, 3%, 5%, 7%, 10%, and 20%, respectively, to study the influence of hybrid microspheres on the thermal conductivity and mechanical properties of EP composites. As shown in Figure 6a, compared to composites filled with randomly distributed fillers (i.e., directly adding PEI microspheres and TA-BNNS), the EP composites containing PEI/TA-BNNS hybrid microspheres exhibited superior thermal conductivity. Moreover, as the amount of PEI/TA-BNNS hybrid microspheres increased, the thermal conductivity of the EP composites showed a significant improvement. When 20% mass fraction of hybrid microspheres was added, the thermal conductivity of the EP composite reached 0.62 W/(m·K), whereas the thermal conductivity of the EP composite modified with an equivalent amount of randomly distributed fillers was only 0.49 W/(m·K). Additionally, mechanical property results indicated that low filler content was beneficial for enhancing the tensile strength of EP composites, but as the filler content increased, the mechanical properties of the composites decreased. Notably, the tensile strength of EP composites containing PEI/TA-BNNS hybrid microspheres was significantly higher than that of composites with randomly distributed fillers (Figure 6b). As shown in Figure 7, this is mainly because the BNNS on the surface of PEI/TA-BNNS hybrid microspheres can interconnect, forming efficient thermal pathways within the EP resin matrix, whereas randomly distributed BNNS tends to aggregate severely, not only disrupting the thermal network but also creating stress concentration points, leading to a reduction in mechanical properties.
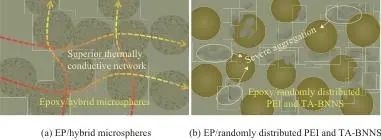
Figure 7 Schematic diagram of the thermal conductivity network of EP composites
(1) PEI microspheres were prepared using the solution precipitation method, and the effects of centrifugation speed, centrifugation time, PVAL content, and stirring speed on the particle size and distribution of PEI were studied. When the centrifugation speed was 5,000 r/min, the centrifugation time was 30 minutes, the stirring speed was 500 r/min, and the mass of PVAL added was twice that of PEI, the particle size distribution of the PEI microspheres was relatively uniform and the morphology was regular.
(2) By utilizing BNNS to assist in the ball milling of h-BN, TA-BNNS with good water dispersibility was prepared. The size of TA-BNNS was significantly reduced, and it was further hybridized with PEI microspheres to construct PEI/TA-BNNS microspheres.
(3) The PEI/TA-BNNS hybrid microspheres can form effective thermal conductive pathways in the EP resin matrix, significantly enhancing the thermal conductivity of the EP composites. With the addition of 20 wt% hybrid microspheres, the thermal conductivity of the EP composites can reach 0.62 W/(m·K), and the tensile strength can reach up to 69.4 MPa. Both the thermal and mechanical properties are notably superior to those of EP composites with the same amount of randomly distributed fillers.
【Copyright and Disclaimer】The above information is collected and organized by PlastMatch. The copyright belongs to the original author. This article is reprinted for the purpose of providing more information, and it does not imply that PlastMatch endorses the views expressed in the article or guarantees its accuracy. If there are any errors in the source attribution or if your legitimate rights have been infringed, please contact us, and we will promptly correct or remove the content. If other media, websites, or individuals use the aforementioned content, they must clearly indicate the original source and origin of the work and assume legal responsibility on their own.