Energy saving and carbon reduction! Covestro successfully completes the modernization of the TDI plant in Dormagen, Germany.
On March 24th, Covestro announced the successful modernization of its TDI (toluene diisocyanate) plant in Dormagen, Germany. The plant was officially inaugurated in an event attended by approximately 60 guests from politics, business, and employees, including North Rhine-Westphalia Minister Oliver Krischer. Covestro also announced new goals to improve energy efficiency in production.
Dr. Philipp Bahke, Site Manager of Covestro's North Rhine-Westphalia plant, stated: "The successful completion of this project demonstrates that climate protection and competitiveness can go hand in hand. The modernized plant sets new standards for energy efficiency and highlights our path towards climate-neutral production. Given the persistently high energy costs in Europe, this project significantly enhances the competitiveness of TDI production in Europe. I would particularly like to thank the entire project team for their professional implementation of this complex modernization while maintaining continuous operation."
The modernized factory consumes 80% less energy than the traditional process and reduces carbon dioxide emissions by 22,000 tons annually. This is achieved through a new reactor weighing 150 tons (330,700 pounds) and standing nearly 20 meters (65.6 feet) tall, which utilizes the energy generated from reactions to produce steam. Covestro began the modernization of the factory in the summer of 2023. Overall, the project installed over 3.5 kilometers of new piping, approximately 14 kilometers of cables, and hundreds of new devices, valves, and monitoring instruments within the factory.
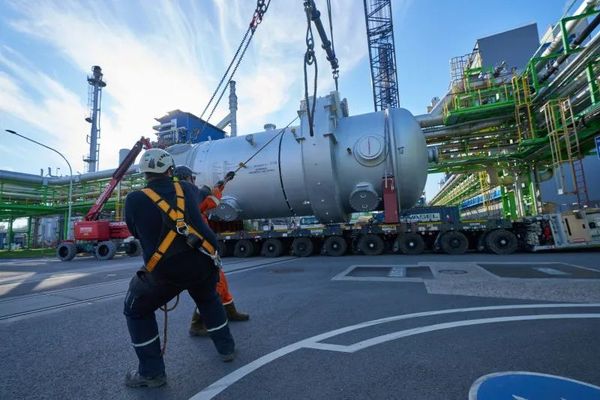
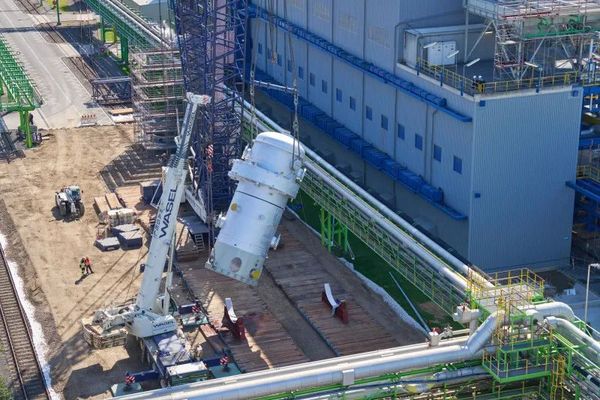
Dr. Christine Mendoza-Frohn, Regional Sales Director for Functional Materials for EMEA and Latin America at Covestro, explained: "In Mommenheim, Germany, we operate the largest TDI production facility in Europe. Through a successful modernization, we can now offer our customers TDI products with a smaller carbon footprint. This helps our customers achieve their sustainability goals and reinforces our position as a reliable partner for climate-neutral and circular solutions."
Propose New Global Energy Efficiency Targets
During the event, Covestro also announced its new and ambitious global energy efficiency targets for production. The company's goal is to reduce the carbon dioxide emissions generated by energy use per ton of product by 20% by 2030 compared to 2020, further emphasizing the importance of energy efficiency as a key factor in achieving operational climate neutrality by 2035. Covestro's TDI plant in Dormagen, Germany, with an annual production capacity of 300,000 tons, serves as a model for successfully transforming existing production facilities to enhance energy efficiency.
The German Federal Ministry for Economic Affairs and Climate Action (BMWK) supported this modernization through its Federal Energy and Resource Efficiency funding program.
TDI (Twin Disc) factory uses gas chromatography.
Cossen was established in the TDI factory in Dortmund, Germany, using the company's gas technology, which, even before modernization, saved up to 60% of energy consumption compared to traditional processes.
Gas-phase technology represents a milestone in the production of isocyanates. This technology is used to manufacture toluene diisocyanate (TDI), which is needed for the production of flexible polyurethane foams. The key breakthrough was the reaction between toluene diamine (TDA) and phosgene in the gaseous phase, rather than in the final liquid-phase process step.
TDI's Practices of Sustainable Production
On August 18, 2024, the pilot plant for the world's first non-phosgene TDI green synthesis technology, independently developed by Shaanxi Coal and Chemical Technology Development Center Co., Ltd. (Shaanxi Coal Technology Center), passed the 72-hour performance test and evaluation organized by the Shaanxi Petroleum and Chemical Industry Federation in Huazhou District, Weinan City, Shaanxi Province.
The main processes of this technology include synthesis, separation, washing, and pyrolysis, four stages in total. Specifically, it involves replacing the highly toxic phosgene with the environmentally friendly chemical carbon dioxide oxide to form an intermediate product, tribenzamidoethanedicarboxylic acid methyl ester (TDC), in conjunction with benzphenamine, utilizing a proprietary catalyst to generate the intermediate product benzodiamine adipate methyl ester (TDC), which, after separation and washing, is further pyrolyzed using a proprietary catalyst to prepare methylene diphenyl diisocyanate (TDI).
The Shaanxi Coal Technology Research and Development Center initiated the non-steam gas synthesis method for green production process research in 2014, which was tested and verified in a laboratory for three years. In August 2017, a technology report was submitted to the Shaanxi Coal Technology Center in Weishi, Shaanxi Province. The center tested the apparatus in a pilot plant on the Shaanxi Coal Technology Center's construction site in August 2020, and the apparatus was tested and calibrated successfully in three iterations. Later on, a second test run of the apparatus was conducted in December and March 2021, and full-scale production of TDI was achieved in August 2021. An expert group of the Northwest Institute of Chemical Engineering, led by Professor Li Shunheng, inspected the data and conducted thorough review of the control, analysis, and sampling on site. The results showed that the apparatus ran smoothly, achieving the expected targets, and exceeded the traditional gas synthesis process by a significant margin, greatly improving the environmental safety and reducing the disposal waste.
Currently, TDI production both domestically and internationally relies on the phosgene method. This involves producing phosgene from carbon monoxide and chlorine, followed by reaction with toluene diamine to produce TDI. Although the production technology is mature, both phosgene and chlorine are highly toxic gases, with phosgene posing a greater danger. This method presents issues such as environmental pollution, equipment corrosion, and the impact of residual chlorine on product quality. Non-phosgene TDI green synthesis processes can replace the traditional phosgene route, achieving both low-carbon green production and reducing safety risks.
【Copyright and Disclaimer】The above information is collected and organized by PlastMatch. The copyright belongs to the original author. This article is reprinted for the purpose of providing more information, and it does not imply that PlastMatch endorses the views expressed in the article or guarantees its accuracy. If there are any errors in the source attribution or if your legitimate rights have been infringed, please contact us, and we will promptly correct or remove the content. If other media, websites, or individuals use the aforementioned content, they must clearly indicate the original source and origin of the work and assume legal responsibility on their own.
Most Popular
-
Covestro faces force majeure!
-
DuPont to Spin Off Nomex and Kevlar Brands for $14.4 Billion: Is Aramid Fiber Still Attractive?
-
Metal Stamping Supplier Autokiniton to Close Detroit Plant and Lay Off Workers
-
Napan Unveils Thermoplastic Composite Three-in-One Power System Solution, Battery Cover Weight Reduced by 67%
-
Massive Retreat of Japanese and Korean Battery Manufacturers