Eight Billion! BASF Signs Contract with Li Auto, Launches Recycled Nylon Project!
Image source: BASF Automotive Coatings OEM Paint
Another highlight of the collaboration is digitization, as both parties will jointly promote data sharing and system openness to achieve intelligent and automated business connectivity. It is worth noting that since 2016, BASF Coatings has been providing a full range of coating products to Ideal Auto to meet its cutting-edge technology requirements and consumer needs.
On March 24, BASF announced that its Coatings division successfully expanded the production capacity of polyester and polyurethane resins at its factory in Caojing, Shanghai. The factory was originally established in 2015 with an annual production capacity of 8,000 tons of polyester and polyurethane resins, and the capacity has now been increased to 18,800 tons per year, achieving a doubling of production capacity.
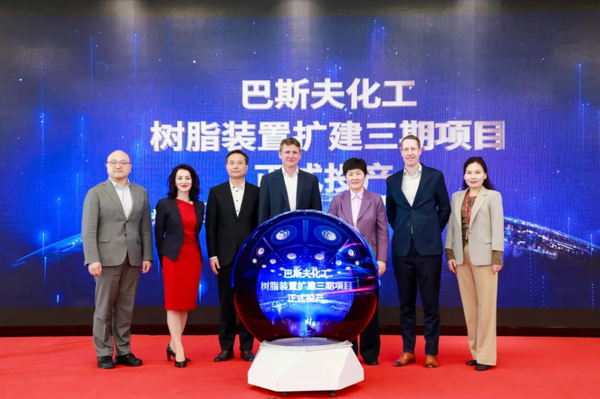
In addition to this resin capacity upgrade, BASF Coatings also plans to further expand its cathodic electrodeposition (ELEC) emulsion and grinding resin capacities at the Chemical Park site by optimizing processes in early 2026. This strategic move will strengthen its supply capabilities in the Asia-Pacific automotive coatings sector, providing stable support for the entire coating process for vehicle manufacturers (OEMs) and component manufacturers in the region over the next decade.
However, recent涂料业务的合作,这充分体现了巴斯夫对亚太地区涂料市场的看好。 However, recently, BASF has signed multiple agreements for its coatings business in China, which also fully demonstrates BASF's confidence in the coatings market in the Asia-Pacific region.
-
On March 10, 2025, the Coatings division of BASF signed an agreement with NIO, aiming to strengthen cooperation in the field of automotive coatings, with a focus on exterior coatings for NIO's electric vehicles. -
On November 9, 2024, Nippon Paint signed a cooperation agreement with BASF. In April 2024, BASF signed a partnership with Oriental Yuhong, focusing on products such as waterproofing materials, architectural coatings, and insulation. -
On August 23, 2024, the new Asia-Pacific Application Center of BASF Coatings (Guangdong) Co., Ltd., a division of BASF's coatings business located in Jiangmen City, Guangdong Province, China, was officially inaugurated, marking another important milestone in BASF's global refinish technology network.
The BASF Resins plant in Caojing, Shanghai, serves the automotive coatings industry in China and the Asia-Pacific region. The plant produces a range of coating raw materials, including acrylic resins, polyester resins, polyurethane resins, electrophoretic emulsions, and grinding resins. Notably, the plant is highly automated and operates entirely on renewable energy. This year marks the 10th anniversary of the successful operation of this resin plant.
BASF's coatings division covers automotive coatings solutions, surface treatment technologies and system solutions, and decorative coatings. Among them, automotive coatings solutions include automotive OEM coatings, automotive repair coatings, and decorative paints. In 2024, BASF's coatings business sales amounted to 4.28 billion euros, a year-on-year decrease of 2.4%.
BASF is the world's largest automotive coatings supplier and one of the three major manufacturers in the original equipment manufacturer (OEM) paint industry. It is also a leader in waterborne coating technology. Its representative brands include the "Lanxess" waterborne primer and "Immobility" self-healing coatings. In addition, BASF has launched the bio-based "BioBased" series of coatings made from renewable castor oil.
However, it is worth mentioning that BASF sold its decorative coatings business in Brazil for $1.15 billion to the globally renowned coatings manufacturer Sherwin-Williams in February this year and is exploring strategic options for its remaining coatings business.
It is reported that Dr. Martin Brudermüller, the new CEO of BASF, announced during a global conference call in early February that the group will consider strategic options for its coatings business, which may include forming joint ventures or changing owners.
Paint market
Automotive coatings can be mainly divided into three categories: original equipment manufacturer (OEM) coatings, automotive refinish paints, and coatings for automotive interior and exterior parts. They can also be classified into water-based coatings and solvent-based coatings.
Currently, the industry is moving towards more functional coatings (such as more weather-resistant, more corrosion-resistant), powder coatings, and more environmentally friendly coatings (water-based coatings, UV/LED coatings, and bio-based coatings).
Key global paint companies include BASF, PPG Industries, AkzoNobel, Nippon Paint, Kansai Paint, DuPont, Mitsubishi Chemical, Hempel, Axalta, and KCC. The industry has high entry barriers and a high market concentration, especially in automotive body coatings, which are almost entirely dominated by these giants.
Relevant data shows that the global coatings market value is estimated at 196 billion US dollars in 2024, and it is expected that the coatings market size will reach 227.5 billion US dollars by 2029, with a compound annual growth rate of 3.2%.
The Asia-Pacific region is one of the major paint consumption areas in the world. Currently, the demand for paints in industries such as automotive, packaging, construction, and electronics continues to grow. The automotive paint market alone is expected to exceed 80 billion yuan in 2024.
China's growth in the new energy vehicle sector has been rapid. For the past 10 consecutive years, China has ranked first in the world, with production and sales reaching 12.888 million and 12.866 million vehicles, respectively, representing year-on-year increases of 34.4% and 35.5%. This will also drive a surge in demand for automotive coatings.
BASF's "expansion + cooperation" strategy for its coatings business in China essentially represents a precise grasp of regional opportunities against the backdrop of global strategic contraction. By strengthening local layout and technical collaboration, BASF has secured its current market share. The growth potential and technological advantages of the Chinese market make it a crucial piece in maximizing the value of BASF's coatings business.
loopamid® is a regenerated polyamide 6 completely based on industrial and post-consumer waste textiles. The raw materials include production waste such as clothing scraps from the textile industry, and even discarded old clothes made from polyamide 6 and other materials. loopamid® products have all been certified by the Global Recycled Standard (GRS), and the first batch of yarn manufacturers has successfully used them. (In 2024, BASF partnered with Inditex to launch the first jacket made entirely from 100% textile waste.)
Regarding recycled polyamide 6, as early as November last year, BASF's Monomers division announced that its polyamide 6 production facility in Shanghai had obtained the International Sustainability and Carbon Certification (ISCC+), enabling the supply of biomass-based Ultramid® BMB Cert™ polyamide 6, Ccycled® polyamide 6, and polyamide 6/6.6 copolymer products. Among these, Ultramid® Ccycled® polyamide 6 is produced using pyrolysis oil extracted from end-of-life tires and mixed plastic waste through chemical recycling as raw materials.
Research on recycled polyamide 6 is indeed necessary, especially considering that in China alone, the production capacity will reach 7.25 million tons per year by 2024, and the industry is still expanding, potentially reaching 9.28 million tons per year by 2028. BASF has introduced two types of recycled polyamide 6, both through chemical recycling, but with different raw materials and processes. The loopamid® product is particularly significant, as fiber represents its largest application and source of waste.
The loopamid® production process includes collection and sorting, shredding, depolymerization into monomers, purification, polymerization, spinning, and finished products. A major challenge is that the raw materials are often made from different fibers, materials, dyes, and additives, and buttons, zippers, and other accessories must be removed in advance. BASF has successfully made closed-loop recycling of polyamide 6 textiles possible, including fabrics with various material blends, such as those containing spandex.
Source: BASF official website
Depolymerization is the core, and common methods include hydrolysis, ammonolysis, alcoholysis, ionic liquids, and enzymatic hydrolysis. BASF previously reported using acids (such as phosphoric acid, phosphorous acid, etc.) or bases (such as alkali metal hydroxides, alkali metal oxides, etc.) for the depolymerization of waste PA6, achieving the recycling of used PA6 carpets. In 2023, BASF and Inditex jointly launched the first nylon 6 jacket made entirely from 100% textile waste.
DuPont mainly recycles mixed waste of PA6 and PA66 using ammonia hydrolysis. Toray reported in September 2023 that it collaborated with Honda to verify supercritical hydrolysis polymer technology to chemically recycle glass fiber reinforced nylon 6 components from scrapped vehicles, claiming that it only takes a few tens of minutes to depolymerize waste nylon 6 into caprolactam monomer.
Additionally, on December 9 last year, Australian company Samsara Eco, which has received investments from Temasek, Lululemon, Hitachi, and Coca-Cola, announced the development of an enzyme capable of recycling nylon 6 using machine learning algorithms. This enzyme can break down nylon 6 from clothing, textiles, and automotive materials back into its original building blocks, maintaining quality even after repeated use, effectively enabling near-infinite recycling. On February 20 this year, Lululemon partnered with Samsara Eco to launch the world's first enzymatically recycled nylon 6,6 product.
In addition to PA6, BASF will also showcase a series of polyurethane solutions incorporating recycled materials under the “Loop” brand, tailored for the footwear, automotive, and synthetic leather industries. The technological breakthrough stems from the application of a series of precise and advanced liquefaction techniques during the sorting and shredding stages, which recycle polyurethane products and transform them into high-performance recycled materials that meet market standards and are commercially viable.
In addition to recycling and regenerating products, BASF is also actively developing biomass-balanced products (using renewable energy and renewable raw materials, non-food bio-based). It has now launched products including polyamide, polyoxymethylene, polyurethane (including TPU and PU), polyether polyols, automotive coatings, as well as specific applications such as electrical safety components and synthetic leather.
Recently, BASF has also launched biomass-based melamine foam, polyethersulfone (PESU), and the world's first high water-absorbent polymer (SAP) HySorb B6610, which is based on polyacrylate and has a product carbon footprint (PCF) of zero.
No matter how international policies change, BASF's sustainable strategy remains unwavering.
【Copyright and Disclaimer】The above information is collected and organized by PlastMatch. The copyright belongs to the original author. This article is reprinted for the purpose of providing more information, and it does not imply that PlastMatch endorses the views expressed in the article or guarantees its accuracy. If there are any errors in the source attribution or if your legitimate rights have been infringed, please contact us, and we will promptly correct or remove the content. If other media, websites, or individuals use the aforementioned content, they must clearly indicate the original source and origin of the work and assume legal responsibility on their own.
Most Popular
-
Covestro faces force majeure!
-
Breaking News! Mitsui Chemicals TDI Unit in Japan Experiences Chlorine Gas Leak Accident!
-
Mitsubishi Chemical Exits! Sumitomo Acquires!
-
DuPont plans to sell Nomex and Kevlar brands for $2 billion! Covestro Declares Force Majeure on TDI / oTDA-based / Polyether Polyol; GAC Group Enters UK Market
-
Borealis suspends polyolefin recycling plant in Austria, Hyundai achieves record Q2 revenue, Volkswagen lowers performance expectations