A New Breakthrough in Plastic Recycling! Discarded Polyethylene Transformed into Recyclable High-Performance Materials
[Introduction]
The Garret Miyake team at Colorado State University published their latest research in Angewandte Chemie, converting post-consumer polyethylene (PE) into reprocessable, chemically recyclable crosslinked polyethylene (XLPE) through a three-step catalytic strategy, providing an innovative solution for the circular economy of plastics.
Research Background
Polyethylene (PE), as the world's most produced plastic (with an annual production exceeding 100 million tons), is difficult to degrade due to its chemical inertness. Traditional crosslinked polyethylene (XLPE) cannot be recycled because of its permanent crosslinked structure. Current upcycling technologies mostly focus on depolymerizing PE into small molecules or simple regeneration, making it hard to balance material performance and recycling characteristics.
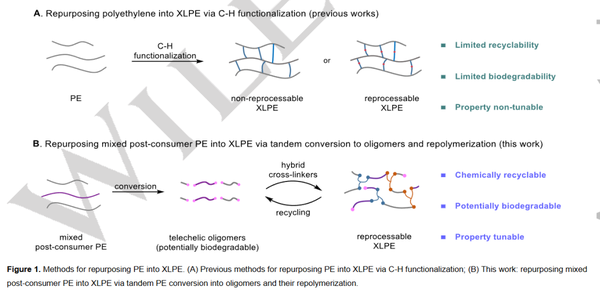
Research Highlights
1️⃣ Three-step catalytic conversion: Converting mixed PE waste into end-hydroxylated oligomers (Mn≈2.7-2.9 kDa) through dehydrogenation-metathesis-hydrogenation
2️⃣ Hybrid crosslinking system: Dynamic crosslinker TETA (triazine derivative) provides reprocessability, while non-dynamic crosslinker Tri-HDI (isocyanate) maintains use stability
3️⃣ Tunable properties: Co-polymerization with commercial Krasol® diol achieves a wide range of elastic modulus from 5-382 MPa and tensile strength from 1.5-17.3 MPa
4️⃣ Closed-loop recycling: Selective depolymerization and recovery of raw materials under basic conditions, achieving high purity monomer recovery (recovery rate >85%) even when mixed with cable insulation

[Introduction]
The Garret Miyake team from Colorado State University published their latest research in Angewandte Chemie, using a three-step catalytic strategy to convert post-consumer polyethylene (PE) into reprocessable, chemically recyclable cross-linked polyethylene (XLPE), providing an innovative solution for the circular economy of plastics.
[Introduction]
[Introduction][Introduction]The Garret Miyake team from Colorado State University published their latest research in Angewandte Chemie, using a three-step catalytic strategy to convert post-consumer polyethylene (PE) into reprocessable, chemically recyclable cross-linked polyethylene (XLPE), providing an innovative solution for the circular economy of plastics.
The Garret Miyake team from Colorado State University published their latest research in Angewandte Chemie, using a three-step catalytic strategy to convert post-consumer polyethylene (PE) into reprocessable, chemically recyclable cross-linked polyethylene (XLPE), providing an innovative solution for the circular economy of plastics.
Research Background
Polyethylene (PE), as the most widely produced plastic globally (with an annual production exceeding 100 million tons), is difficult to degrade due to its chemical inertness. Traditional cross-linked polyethylene (XLPE) cannot be recycled because of its permanent cross-linked structure. Current upcycling technologies mostly focus on depolymerizing PE into small molecules or simple regeneration, making it hard to balance material performance and circularity.
Research Background
Research Background Research BackgroundPolyethylene (PE), as the most widely produced plastic globally (with an annual production exceeding 100 million tons), is difficult to degrade due to its chemical inertness. Traditional cross-linked polyethylene (XLPE) cannot be recycled because of its permanent cross-linked structure. Current upcycling technologies mostly focus on depolymerizing PE into small molecules or simple regeneration, making it hard to balance material performance and circularity.
Polyethylene (PE), as the most widely produced plastic globally (with an annual production exceeding 100 million tons), is difficult to degrade due to its chemical inertness. Traditional cross-linked polyethylene (XLPE) cannot be recycled because of its permanent cross-linked structure. Current upcycling technologies mostly focus on depolymerizing PE into small molecules or simple regeneration, making it hard to balance material performance and circularity.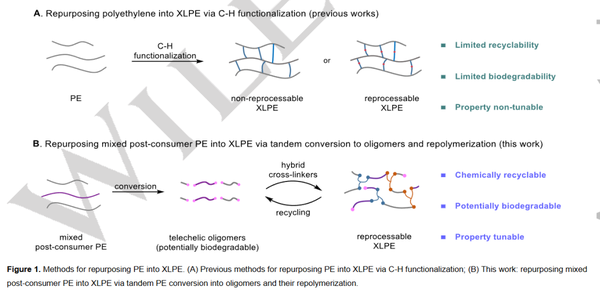
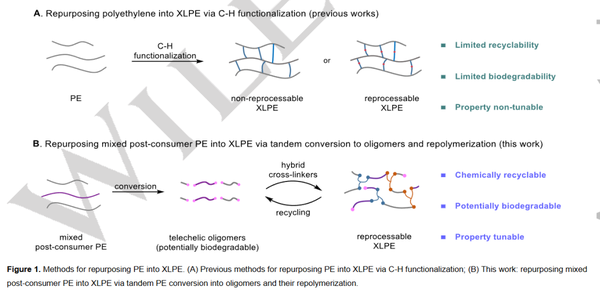
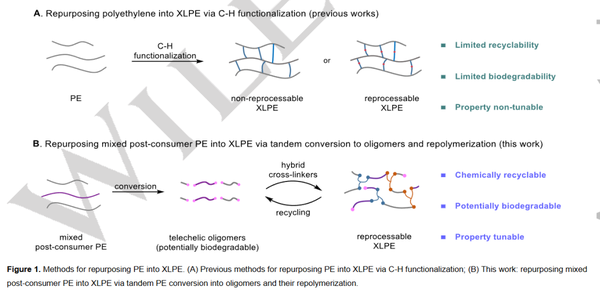
Research Highlights
1️⃣ Three-step catalytic conversion: Converting mixed PE waste into end-hydroxylated oligomers (Mn≈2.7-2.9 kDa) through dehydrogenation-metathesis-hydrogenation
2️⃣ Hybrid crosslinking system: Dynamic crosslinker TETA (triazine derivative) imparts reprocessability, while non-dynamic crosslinker Tri-HDI (isocyanate) maintains use stability
3️⃣ Tunable properties: Co-polymerization with commercial Krasol® diol achieves a wide range of elastic modulus from 5 to 382 MPa and tensile strength from 1.5 to 17.3 MPa
4️⃣ Closed-loop recycling: Selective depolymerization for material recovery under alkaline conditions, still achieving pure monomer recovery (recovery rate > 85%) even when mixed with cable insulation
Research Highlights
Research Highlights Research Highlights1️⃣ Three-step catalytic conversion: Converting mixed PE waste into end-hydroxylated oligomers (Mn≈2.7-2.9 kDa) through dehydrogenation-metathesis-hydrogenation
1️⃣ Three-step catalytic conversion: Converting mixed PE waste into end-hydroxylated oligomers (Mn≈2.7-2.9 kDa) through dehydrogenation-metathesis-hydrogenation2️⃣ Hybrid crosslinking system: Dynamic crosslinker TETA (triazine derivative) imparts reprocessability, while non-dynamic crosslinker Tri-HDI (isocyanate) maintains use stability
2️⃣ Hybrid crosslinking system: Dynamic crosslinker TETA (triazine derivative) imparts reprocessability, while non-dynamic crosslinker Tri-HDI (isocyanate) maintains use stability3️⃣ Tunable properties: Co-polymerization with commercial Krasol® diol achieves a wide range of elastic modulus from 5 to 382 MPa and tensile strength from 1.5 to 17.3 MPa
3️⃣ Tunable Performance: Co-polymerization with commercial Krasol® diols achieves a wide range of modulations in elastic modulus from 5-382 MPa and tensile strength from 1.5-17.3 MPa4️⃣ Closed-loop Recycling: Selective depolymerization for material recovery under alkaline conditions, allowing for the pure monomer to be recovered at a rate greater than 85% even when mixed with cable insulation layers
4️⃣ Closed-loop Recycling: Selective depolymerization for material recovery under alkaline conditions, allowing for the pure monomer to be recovered at a rate >85% even when mixed with cable insulation layers


Key Technical Breakthroughs
Key Technical BreakthroughsKey Technical Breakthroughs1. Dynamic Network Design
By retaining 10% hydroxyl groups to trigger triazine group SNAr exchange reactions, XLPE-1 can be reprocessed up to 3 times at 150°C while maintaining over 90% of its mechanical properties. The dynamic cross-linking reduces the creep rate of the material by 80% compared to the original PE at 110°C.
1. Dynamic Network Design
1. Dynamic Network DesignThrough the SNAr exchange reaction by retaining 10% of hydroxy-initiated triazine groups, XLPE-1 can be reprocessed three times at 150°C while maintaining over 90% of its mechanical properties. Dynamic crosslinking reduces the creep rate of the material at 110°C by 80% compared to the original PE.
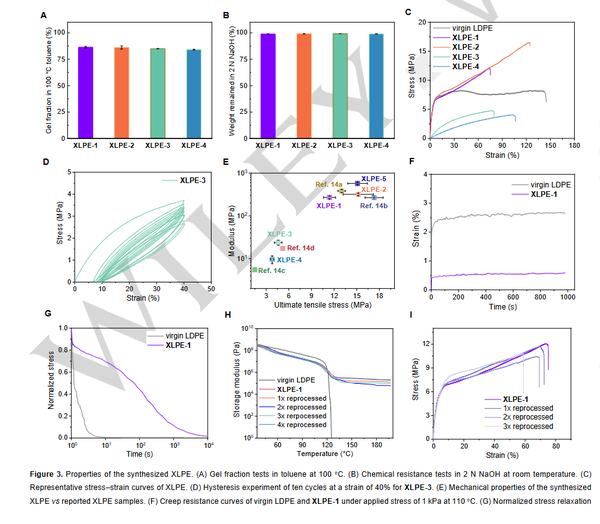
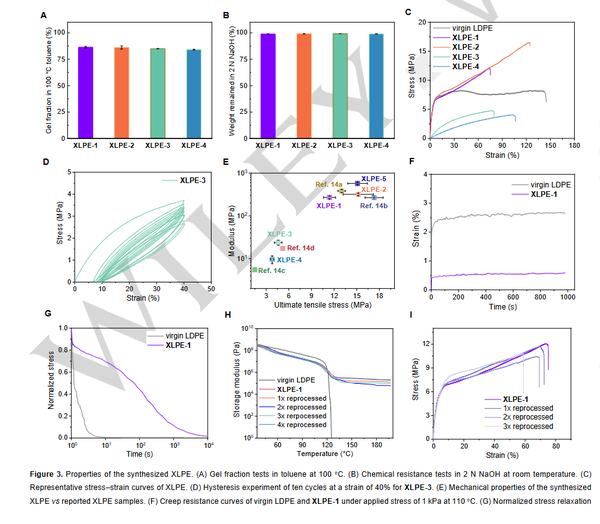
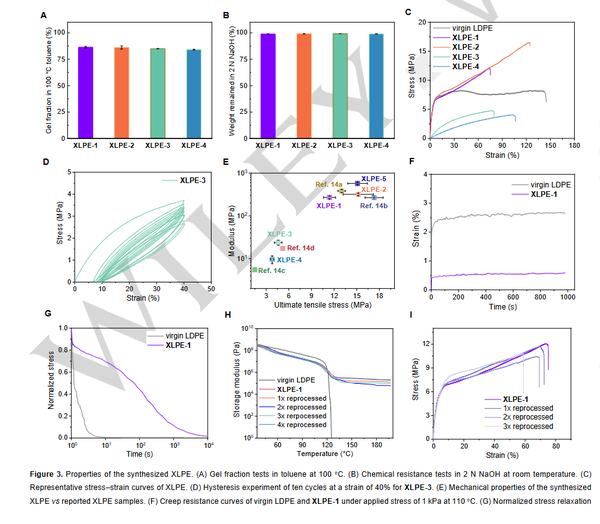
2. Composite System Construction
The XLPE-3 obtained by copolymerizing PE oligomers with Krasol® HLBH-P 3000 diol (50:50) exhibits rubber-like elasticity, with a strain recovery rate of 72% after 10 cycles at 40% strain.
3. Validation with Actual Waste Materials
The XLPE-5 prepared from a mixture of milk bottles (HDPE) and plastic bags (LDPE) achieves a tensile strength of 15.1 MPa, an 84% improvement over the raw materials. After selective depolymerization when mixed with cables, the insulation layer remains intact.
2. Composite System Construction
2. Composite System ConstructionThe XLPE-3 obtained by copolymerizing PE oligomers with Krasol® HLBH-P 3000 diol (50:50) exhibits rubber-like elasticity, with a strain recovery rate of 72% after 10 cycles at 40% strain.
The XLPE-3 obtained by copolymerizing PE oligomers with Krasol® HLBH-P 3000 diol (50:50) exhibits rubber-like elasticity, with a strain recovery rate of 72% after 10 cycles at 40% strain.3. Actual Waste Validation
3. Actual Waste ValidationThe XLPE-5 prepared from a mixture of milk jugs (HDPE) and plastic bags (LDPE) has a tensile strength of 15.1 MPa, an 84% increase over the raw materials. After selective depolymerization when mixed with cables, the insulation layer remains intact.
The XLPE-5 prepared from a mixture of milk jugs (HDPE) and plastic bags (LDPE) has a tensile strength of 15.1 MPa, an 84% increase over the raw materials. After selective depolymerization when mixed with cables, the insulation layer remains intact.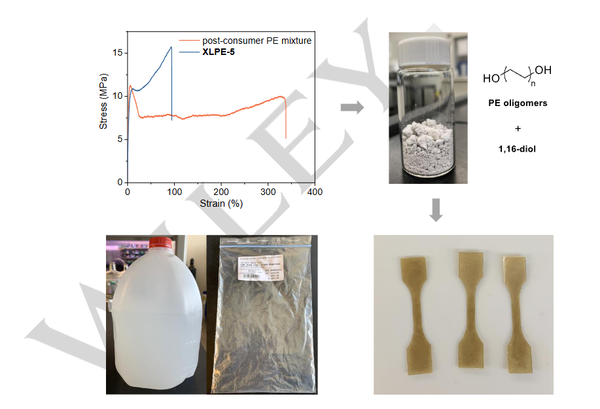
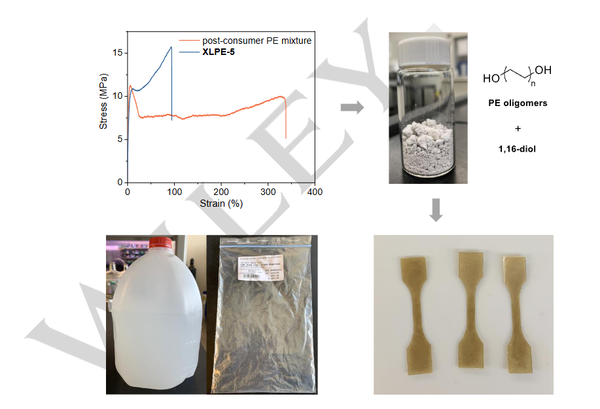
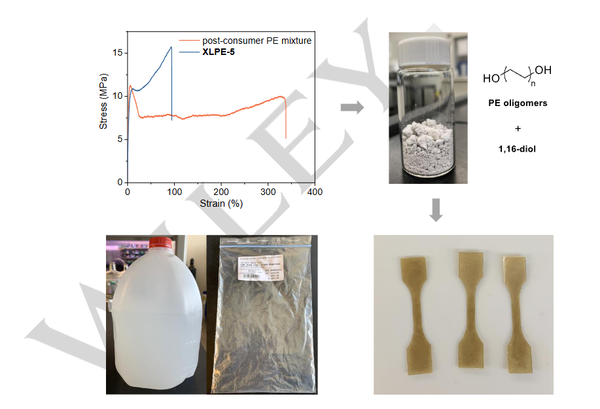
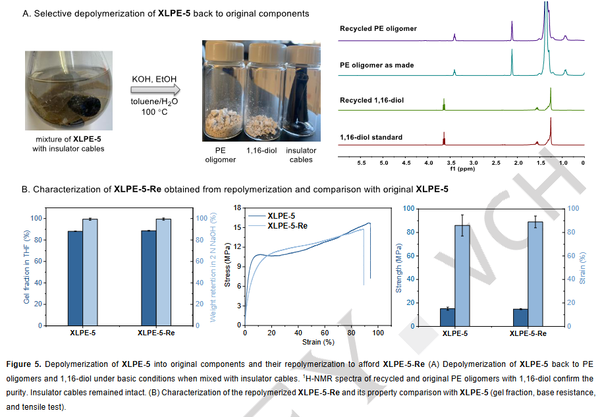
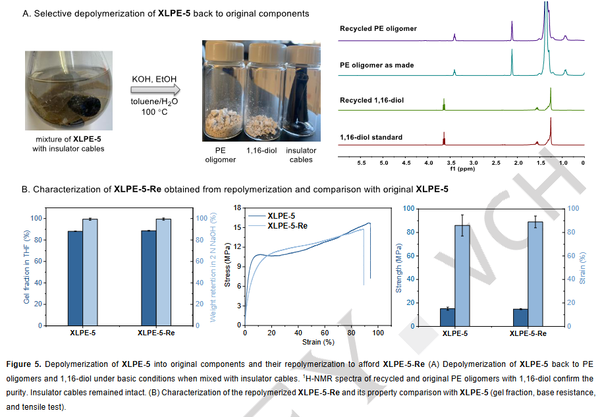
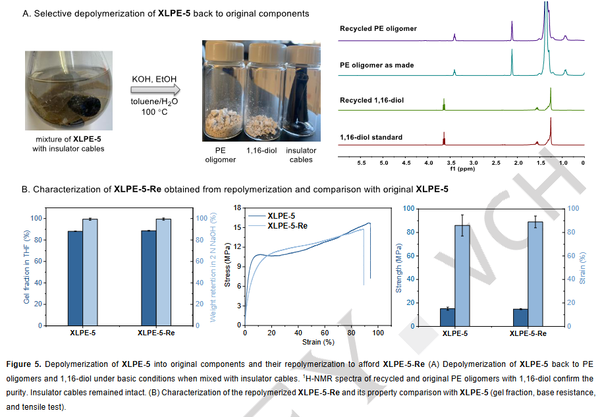
【Copyright and Disclaimer】The above information is collected and organized by PlastMatch. The copyright belongs to the original author. This article is reprinted for the purpose of providing more information, and it does not imply that PlastMatch endorses the views expressed in the article or guarantees its accuracy. If there are any errors in the source attribution or if your legitimate rights have been infringed, please contact us, and we will promptly correct or remove the content. If other media, websites, or individuals use the aforementioned content, they must clearly indicate the original source and origin of the work and assume legal responsibility on their own.
Most Popular
-
Covestro faces force majeure!
-
Breaking News! Mitsui Chemicals TDI Unit in Japan Experiences Chlorine Gas Leak Accident!
-
DuPont plans to sell Nomex and Kevlar brands for $2 billion! Covestro Declares Force Majeure on TDI / oTDA-based / Polyether Polyol; GAC Group Enters UK Market
-
Mitsubishi Chemical Exits! Sumitomo Acquires!
-
Borealis suspends polyolefin recycling plant in Austria, Hyundai achieves record Q2 revenue, Volkswagen lowers performance expectations