A Look Back at Five New Types of Transparent Plastics + Five Innovative Applications (From Packaging to Electronics)
The average light transmittance of transparent plastics is 88-92%, and the haze is 0.5-4%. For example, general-purpose polymethyl methacrylate (PMMA or acrylic) is considered the gold standard for transparent plastics. It has a light transmittance of 93% and a haze of 0.5%, and all other plastics are judged against this standard.
➤Light Transmittance - defines the percentage of light that passes through a given plastic material, or the transparency of the plastic. It is expressed as a number between 0% and 100%.
➤Haze - a measure of turbidity or cloudiness, referring to the amount of light scattered when passing through a transparent material. It is expressed in percentages (%), with values closest to 0% indicating complete transparency and those greater than 30% indicating translucency.
Typical transparent plastics include: Polystyrene (PS), Polyethylene terephthalate (PET), Polymethyl methacrylate (PMMA, or acrylic), Polycarbonate (PC) and its related copolymers, Amorphous nylon, Bioplastics [polyethylene furanoate (PEF), cellulose, and lignin variants], Styrenic block copolymers (SBC), Thermoplastic elastomers (TPE), Recycled olefin clear variants, Rare europium-based polytitanates (Eu-POT), Ultraviolet (UV) coated polymers, etc.
Let's review five recent transparent material technologies, and then take a detailed look at five application innovations.
One, Ineos Bio-Based SMMA
With water-like clarity
Ineos Styrolution’s NAS® ECO is a rigid amorphous styrene methyl methacrylate (SMMA) copolymer. It has a light transmittance of 91% and a haze of 2%, made from styrene derived from recycled or bio-based feedstocks. Their raw material sourcing, supply chain, and production processes have been qualified under the International Sustainability & Carbon Certification Plus (ISCC+) standard. This means they meet the highest sustainability certification standards. ISCC+ is a voluntary certification scheme to verify the sustainability characteristics of alternative feedstocks.
Its applications include: water filter pitcher housings, water tanks, displays, and food containers or boxes.
NAS® ECO's optical properties
The average light transmittance of transparent plastics is 88-92%, with a haze of 0.5-4%. For example, general-purpose polymethyl methacrylate (PMMA or acrylic) is considered the gold standard for transparent plastics. It has a light transmittance of 93% and a haze of 0.5%, against which all other plastics are judged.
The average light transmittance of transparent plastics is 88-92%, with a haze of 0.5-4%. For example, general-purpose polymethyl methacrylate (PMMA or acrylic) is considered the gold standard for transparent plastics. It has a light transmittance of 93% and a haze of 0.5%, against which all other plastics are judged.
The average light transmittance of transparent plastics is 88-92%, with a haze of 0.5-4%. For example, general-purpose polymethyl methacrylate (PMMA or acrylic) is considered the gold standard for transparent plastics. It has a light transmittance of 93% and a haze of 0.5%, against which all other plastics are judged.
The average light transmittance of transparent plastics is 88-92%, with a haze of 0.5-4%. For example, general-purpose polymethyl methacrylate (PMMA or acrylic) is considered the gold standard for transparent plastics. It has a light transmittance of 93% and a haze of 0.5%, against which all other plastics are judged.
The average light transmittance of transparent plastics is 88-92%, with a haze of 0.5-4%. For example, general-purpose polymethyl methacrylate (PMMA or acrylic) is considered the gold standard for transparent plastics. It has a light transmittance of 93% and a haze of 0.5%, against which all other plastics are judged.➤Light Transmittance - Defines the percentage of light that passes through a given plastic material, or the transparency of the plastic. It is expressed as a number between 0% and 100%.
➤Haze - A measure of turbidity or cloudiness, referring to the amount of light scattered when passing through a transparent material. It is expressed in percentages (%), with values closest to 0% indicating complete transparency and those greater than 30% indicating translucency.
Typical transparent plastics include: polystyrene (PS), polyethylene terephthalate (PET), polymethyl methacrylate (PMMA, or acrylic), polycarbonate (PC) and its related copolymers, amorphous nylon, bioplastics [polyethylene furanoate (PEF), cellulose and lignin variants], styrenic block copolymers (SBC), thermoplastic elastomers (TPE), recycled olefin transparent variants, rare europium-based polytitanates (Eu-POT), ultraviolet (UV) coated polymers, etc.
Let's review five recent transparent material technologies, and then take an in-depth look at five application innovations.
One, INEOS bio-based SMMA
➤Light Transmittance - Defines the percentage of light that passes through a given plastic material, or the transparency of the plastic. It is expressed as a number between 0% and 100%.
➤Light Transmittance - Defines the percentage of light that passes through a given plastic material, or the transparency of the plastic. It is expressed as a number between 0% and 100%.➤Haze - a measure of turbidity or cloudiness, refers to the amount of light scattered when passing through a transparent material. It is expressed as a percentage (%), with values closest to 0% indicating complete transparency and those above 30% indicating translucency.
Typical transparent plastics include: Polystyrene (PS), Polyethylene Terephthalate (PET), Polymethyl Methacrylate (PMMA, or acrylic), Polycarbonate (PC) and its related copolymers, amorphous nylon, bioplastics [Polyethylene Furanoate (PEF), cellulose, and lignin variants], Styrene Block Copolymers (SBC), Thermoplastic Elastomers (TPE), recycled olefin transparent variants, rare europium-based polytitanates (Eu-POT), Ultraviolet (UV) coated polymers, etc.
Typical transparent plastics include: Polystyrene (PS), Polyethylene Terephthalate (PET), Polymethyl Methacrylate (PMMA, or acrylic), Polycarbonate (PC) and its related copolymers, amorphous nylon, bioplastics [Polyethylene Furanoate (PEF), cellulose, and lignin variants], Styrene Block Copolymers (SBC), Thermoplastic Elastomers (TPE), recycled olefin transparent variants, rare europium-based polytitanates (Eu-POT), Ultraviolet (UV) coated polymers, etc.
Let's review five recent transparent material technologies and then take a detailed look at five application innovations.
Let's review five recent transparent material technologies and then take a detailed look at five application innovations.1. INEOS Bio-based SMMA
1. INEOS Bio-based SMMAWith water-like clarity in transparency
With water-like clarity in transparency
With water-like clarity in transparency
With water-like clarity in transparency
With water-like clarity in transparency
With water-like clarity in transparencyIneos Styrolution's NAS® ECO is a hard, amorphous styrene methyl methacrylate (SMMA) copolymer. It has a light transmittance of 91% and a haze of 2%, made from styrene derived from recycled or bio-based feedstocks. Their raw material sources, supply chains, and production processes have been qualified under the International Sustainability & Carbon Certification Plus (ISCC+) standard. This means they meet the highest standards for sustainability certification. ISCC+ is a voluntary certification scheme that verifies the sustainability characteristics of alternative feedstocks.
Ineos Styrolution's NAS® ECO is a hard, amorphous styrene methyl methacrylate (SMMA) copolymer. It has a light transmittance of 91% and a haze of 2%, made from styrene derived from recycled or bio-based feedstocks. Their raw material sources, supply chains, and production processes have been qualified under the International Sustainability & Carbon Certification Plus (ISCC+) standard. This means they meet the highest standards for sustainability certification. ISCC+ is a voluntary certification scheme that verifies the sustainability characteristics of alternative feedstocks.
Ineos Styrolution's NAS® ECO is a hard, amorphous styrene methyl methacrylate (SMMA) copolymer. It has a light transmittance of 91% and a haze of 2%, made from styrene derived from recycled or bio-based feedstocks. Their raw material sources, supply chains, and production processes have been qualified under the International Sustainability & Carbon Certification Plus (ISCC+) standard. This means they meet the highest standards for sustainability certification. ISCC+ is a voluntary certification scheme that verifies the sustainability characteristics of alternative feedstocks.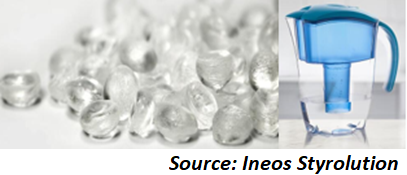
Its application scenarios include: water filter jug shells, water tanks, displays, and food containers or boxes.
The optical properties of NAS® ECO are similar to those of polymethyl methacrylate (PMMA, also known as acrylic). However, compared to acrylic, NAS® ECO has advantages such as lower density, better processability, and a lower product carbon footprint.
II. Trinseo Sustainable PMMA Resins
Its application scenarios include: water filter jug shells, water tanks, displays, and food containers or boxes.
Its application scenarios include: water filter jug shells, water tanks, displays, and food containers or boxes.The optical properties of NAS® ECO are similar to those of polymethyl methacrylate (PMMA, also known as acrylic). However, compared to acrylic, NAS® ECO has advantages such as lower density, better processability, and a lower product carbon footprint.
The optical properties of NAS® ECO are similar to those of polymethyl methacrylate (PMMA, also known as acrylic). However, compared to acrylic, NAS® ECO has advantages such as lower density, better processability, and a lower product carbon footprint.II. Trinseo Sustainable PMMA Resins
II. Trinseo Sustainable PMMA ResinsIt features high light transmittance
It features high light transmittance
It features high light transmittance
It features high light transmittance
It features high light transmittance
It features high light transmittance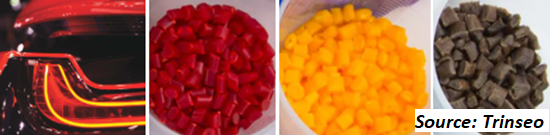
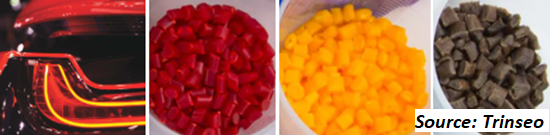
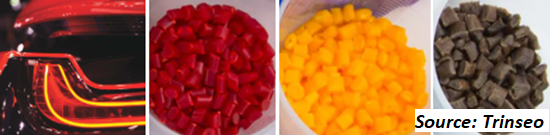
Trinseo's PLEXIGLAS® R-Life V825T is a dual product series of sustainable advantage injection molding grade polymethyl methacrylate (PMMA, also known as acrylic) resins. It has a light transmittance of 93% and a haze of 0.5%. It is a versatile transparent material with broad applicability in the automotive industry.
PLEXIGLAS® R-Life V825T MR35 contains 35% pre-consumer recycled acrylic or PMMA, and PLEXIGLAS® R-Life V825T CR50 is made from 50% recycled methyl methacrylate (MMA) monomer, which is obtained by depolymerizing pre- and post-consumer waste streams. Both grades are certified by the International Organization for Standardization (ISO) 14021. ISO 14021 defines recycled content as materials that include only pre-consumer and post-consumer materials.
The main characteristics of PLEXIGLAS® R-Life include: high light transmittance, high clarity for thick-wall applications, capability to be coated, high weather resistance and UV resistance, 50% lighter than glass, and can be recycled multiple times.
The primary applications in the automotive field are tail light housings, dashboard covers, and interior and exterior decorations.
III. NYCOA Amorphous Nylon
Trinseo's PLEXIGLAS® R-Life V825T is a dual product series of sustainable advantage injection molding grade polymethyl meth基丙烯酸甲酯 (PMMA,即丙烯酸) 树脂的双产品系列。其透光率为93%,雾度为0.5%。它是一种通用的透明材料,在汽车行业具有广泛的适用性。
Trinseo's PLEXIGLAS® R-Life V825T is a dual product series of sustainable advantage injection molding grade polymethyl methacrylate (PMMA, also known as acrylic) resins. It has a light transmittance of 93% and a haze of 0.5%. It is a versatile transparent material with broad applicability in the automotive industry.PLEXIGLAS® R-Life V825T MR35 contains 35% pre-consumer recycled acrylic or PMMA, and PLEXIGLAS® R-Life V825T CR50 is made from 50% recycled methyl methacrylate (MMA) monomer, which is obtained by depolymerizing pre- and post-consumer waste streams. Both grades are certified by the International Organization for Standardization (ISO) 14021. ISO 14021 defines recycled content as materials that include only pre-consumer and post-consumer materials.
PLEXIGLAS® R-Life V825T MR35 contains 35% pre-consumer recycled acrylic or PMMA, and PLEXIGLAS® R-Life V825T CR50 is made from 50% recycled methyl methacrylate (MMA) monomer, which is obtained by depolymerizing pre- and post-consumer waste streams. Both grades are certified by the International Organization for Standardization (ISO) 14021. ISO 14021 defines recycled content as materials that include only pre-consumer and post-consumer materials.The main characteristics of PLEXIGLAS®R-Life include: high light transmittance, high clarity for thick-walled applications, can be coated, has high weather resistance and UV resistance, is 50% lighter than glass, and can be recycled multiple times.
The main characteristics of PLEXIGLAS®R-Life include: high light transmittance, high clarity for thick-walled applications, can be coated, has high weather resistance and UV resistance, is 50% lighter than glass, and can be recycled multiple times.The primary applications in the automotive sector are tail light housings, dashboard covers, and interior and exterior decorations.
The primary applications in the automotive sector are tail light housings, dashboard covers, and interior and exterior decorations.
III. NYCOA Amorphous Nylon
III. NYCOA Amorphous NylonHigh transparency and hydrolysis resistance
High transparency and hydrolysis resistance
High transparency and hydrolysis resistance
High transparency and hydrolysis resistance
High transparency and hydrolysis resistance
High transparency and hydrolysis resistanceNYCOA's NY-Clear 6I/6T nylon is a transparent, high-performance, amorphous nylon copolymer. It has a light transmittance of 85% and a haze value of 5%. Compared to nylon 6 and nylon 66, it has higher heat resistance, lower moisture absorption, and better durability.
NYCOA's NY-Clear 6I/6T nylon is a transparent, high-performance, amorphous nylon copolymer. It has a light transmittance of 85% and a haze value of 5%. Compared to nylon 6 and nylon 66, it has higher heat resistance, lower moisture absorption, and better durability.
NYCOA's NY-Clear 6I/6T nylon is a transparent, high-performance, amorphous nylon copolymer. It has a light transmittance of 85% and a haze value of 5%. Compared to nylon 6 and nylon 66, it has higher heat resistance, lower moisture absorption, and better durability.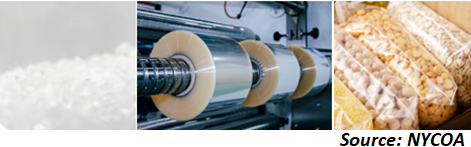
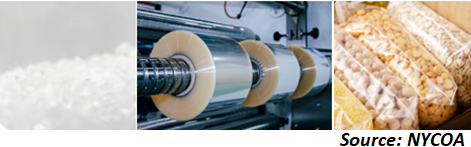
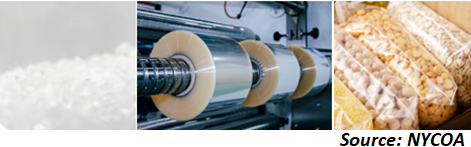
It is used in various flexible food packaging and coated beverage carton material applications that require: high clarity, stiffness, hydrolysis resistance, and strong permeability to oxygen, carbon dioxide, and water vapor.
In addition, the NY-Clear grade is optimized for precision injection molding parts, featuring high dimensional stability and gloss. It is specifically designed for blown film and extrusion applications. They are widely used in high-temperature packaging applications, such as oven bags. Compared to many high-performance engineering plastics, amorphous nylon also has a high glass transition temperature (Tg), high heat deflection temperature (HDT), low creep at high temperatures, and good chemical resistance.
Four, Avantium's PEF bioplastics
In addition, the NY-Clear grade is optimized for precision injection molding parts, featuring high dimensional stability and gloss. It is specifically designed for blown film and extrusion applications. They are widely used in high-temperature packaging applications, such as oven bags. Compared to many high-performance engineering plastics, amorphous nylon also has a high glass transition temperature (Tg), high heat deflection temperature (HDT), low creep at high temperatures, and good chemical resistance.
Four, Avantium's PEF bioplastics
Can extend the shelf life of packaged foods and beverages
Can extend the shelf life of packaged foods and beverages
Can extend the shelf life of packaged foods and beverages
Can extend the shelf life of packaged foods and beverages
Can extend the shelf life of packaged foods and beverages
Can extend the shelf life of packaged foods and beveragesAvantium's Releaf® brand polyethylene furanoate (PEF) bioplastic is a 100% plant-based recyclable polymer. It has a light transmittance of 88% and a haze of 3%.
Avantium's Releaf® brand polyethylene furanoate (PEF) bioplastic is a 100% plant-based recyclable polymer. It has a light transmittance of 88% and a haze of 3%.
Avantium's Releaf® brand polyethylene furanoate (PEF) bioplastic is a 100% plant-based recyclable polymer. It has a light transmittance of 88% and a haze of 3%.
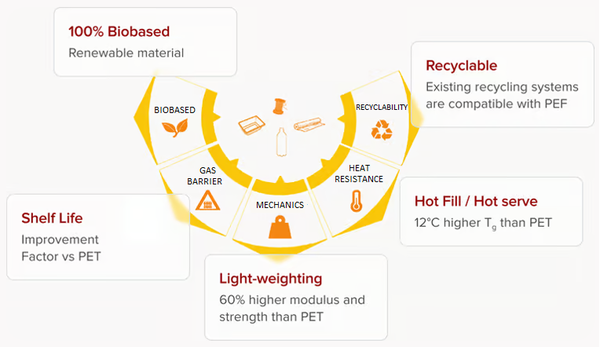
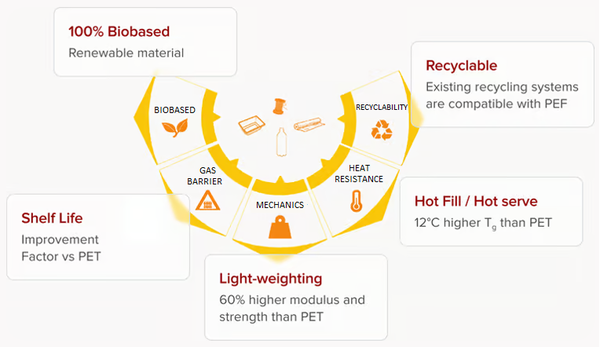
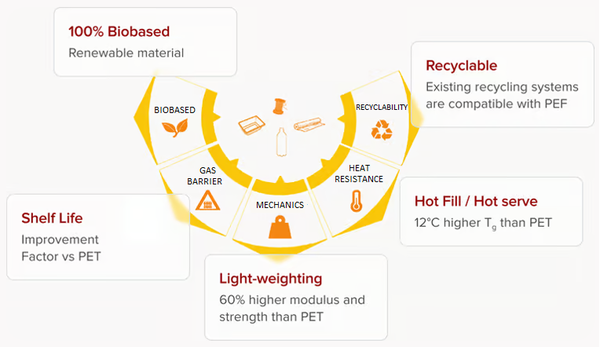
Characteristics and Advantages of the Releaf® Brand PEF (Source: Avantium)
The main advantages of PEF are as follows:
It can be regenerated using monomer raw materials of furan dicarboxylic acid (FDCA) made from wheat or corn starch, glucose, or fructose;
It is fully compatible with existing polyethylene terephthalate (PET) recycling systems and material streams. The global PEF bottle market is estimated at 100 million tons/year. The potential for the global PEF film/sheet to thermoformed tray market exceeds 5 million tons/year;
Compared to PET and traditional glass or aluminum packaging, it has a significantly lower carbon footprint;
Its oxygen barrier is 10 times higher than that of PET, its carbon dioxide barrier is 6 times higher, and its water barrier is 2 times higher. It has overall excellent barrier properties, thus extending the shelf life of packaged foods and beverages;
It has ideal heat resistance, suitable for hot filling and hot service packaging applications, with a Tg of 86°C and a melting point (Tm) of 235°C;
It has high mechanical strength, allowing for a reduction in the amount of plastic material used in food or beverage packaging.
Characteristics and Advantages of the Releaf® Brand PEF (Source: Avantium)
Characteristics and Advantages of the Releaf® Brand PEF (Source: Avantium)The main advantages of PEF are as follows:
The main advantages of PEF are as follows:It can be regenerated using monomer raw materials of furan dicarboxylic acid (FDCA) made from wheat or corn starch, glucose, or fructose;
It can be regenerated using monomer raw materials of furan dicarboxylic acid (FDCA) made from wheat or corn starch, glucose, or fructose;It is fully compatible with existing polyethylene terephthalate (PET) recycling systems and material streams. The global PEF bottle market is estimated at 100 million tons/year. The potential for the global PEF film/sheet to thermoformed tray market exceeds 5 million tons/year;
It is fully compatible with existing polyethylene terephthalate (PET) recycling systems and material streams. The global PEF bottle market is estimated at 100 million tons/year. The potential for the global PEF film/sheet to thermoformed tray market exceeds 5 million tons/year;Compared to PET and traditional glass or aluminum packaging, it has a significantly lower carbon footprint;
Compared to PET and traditional glass or aluminum packaging, it has a significantly lower carbon footprint;Its oxygen barrier is 10 times higher than that of PET, its carbon dioxide barrier is 6 times higher, and its water barrier is 2 times higher. It has overall excellent barrier properties, thus extending the shelf life of packaged foods and beverages;
Its oxygen barrier is 10 times higher than PET, carbon dioxide barrier is 6 times higher, and water barrier is 2 times higher. It has an overall excellent barrier performance, thus extending the shelf life of packaged foods and beverages;It has ideal heat resistance, suitable for hot filling and hot service packaging applications, with a Tg of 86°C and a melting point (Tm) of 235°C;
It has ideal heat resistance, suitable for hot filling and hot service packaging applications, with a Tg of 86°C and a melting point (Tm) of 235°C;It has high mechanical strength, which can reduce the amount of plastic material used in food or beverage packaging.
It has high mechanical strength, which can reduce the amount of plastic material used in food or beverage packaging.
Five, Teknor Apex transparent TPE
Reduce material surface shedding
Five, Teknor Apex transparent TPE
Five, Teknor Apex transparent TPE
Five, Teknor Apex transparent TPE
Five, Teknor Apex transparent TPE
Five, Teknor Apex transparent TPE
Five, Teknor Apex Transparent TPE
Five, Teknor Apex Transparent TPE
Five, Teknor Apex Transparent TPE
Five, Teknor Apex Transparent TPEReduce material surface shedding
Reduce material surface shedding
Reduce material surface shedding
Reduce material surface shedding
Reduce material surface shedding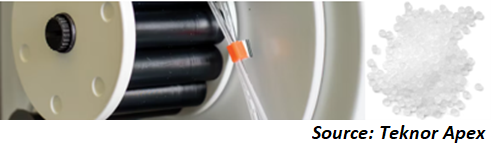
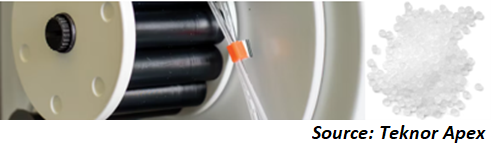
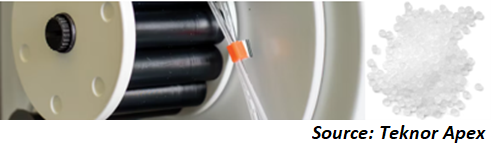
Teknor Apex's Medalist® thermoplastic elastomers (TPEs) (such as MD-9000 olefin compounds) are advancing the progress of biopharmaceutical tubing. It has a light transmittance of 86% and a haze of 4%. These TPEs are suitable for applications requiring flexibility or rubber-like elasticity.
Medalist® TPE grades offer a variety of performance advantages. They improve transparency and reduce material surface shedding during use. This makes them ideal for more reliable fluid flow and extended service life, such as: biopharmaceutical liquid transfer lines, pump components, bioreactors, and filtration systems in critical medical processes.
In addition, the MD-9000 series TPEs are made from FDA-compliant biocompatible ingredients. These materials are free of phthalates, bisphenol A, latex, and animal-derived materials. They can be sterilized with ethylene oxide, gamma rays, electron beams, X-rays, and autoclaving.
These TPEs have broad chemical resistance. For example, they resist isopropanol, acids, bases, and disinfectants (such as chlorine and bleach). Compliance with regulatory requirements for good manufacturing practices in ISO 13485 certified facilities, and adherence to relevant medical product standards (such as USP Class VI and ISO 10993-5), are also among their strengths.
Next, let's turn our attention to innovations in transparent plastic applications.
Teknor Apex's Medalist® thermoplastic elastomers (TPEs) (such as MD-9000 olefin compounds) are advancing the progress of biopharmaceutical tubing. It has a light transmittance of 86% and a haze of 4%. These TPEs are suitable for applications requiring flexibility or rubber-like elasticity.
Teknor Apex's Medalist® thermoplastic elastomers (TPEs) (such as MD-9000 olefin compounds) are advancing the progress of biopharmaceutical tubing. It has a light transmittance of 86% and a haze of 4%. These TPEs are suitable for applications requiring flexibility or rubber-like elasticity.Medalist® TPE grades offer a variety of performance advantages. They improve transparency and reduce material surface shedding during use. This makes them ideal for more reliable fluid flow and extended service life, such as: biopharmaceutical liquid transfer lines, pump components, bioreactors, and filtration systems in critical medical processes.
Medalist® TPE grades offer a variety of performance advantages. They improve transparency and reduce material surface shedding during use. This makes them ideal for more reliable fluid flow and extended service life, such as: biopharmaceutical liquid transfer lines, pump components, bioreactors, and filtration systems in critical medical processes.In addition, the MD-9000 series TPEs are made from FDA-compliant biocompatible ingredients. These materials are free of phthalates, bisphenol A, latex, and animal-derived materials. They can be sterilized with ethylene oxide, gamma rays, electron beams, X-rays, and autoclaving.
In addition, the MD-9000 series TPEs are made from FDA-compliant biocompatible ingredients. These materials are free of phthalates, bisphenol A, latex, and animal-derived materials. They can be sterilized with ethylene oxide, gamma rays, electron beams, X-rays, and autoclaving.These TPEs have a broad chemical resistance. For example, they are resistant to isopropyl alcohol, acids, bases, and disinfectants (such as chlorine and bleach). Compliance with regulatory requirements for good manufacturing practices in ISO 13485 certified factories, and adherence to relevant medical product standards (such as USP Class VI and ISO 10993-5), are also among their advantages.
These TPEs have a broad chemical resistance. For example, they are resistant to isopropyl alcohol, acids, bases, and disinfectants (such as chlorine and bleach). Compliance with regulatory requirements for good manufacturing practices in ISO 13485 certified factories, and adherence to relevant medical product standards (such as USP Class VI and ISO 10993-5), are also among their advantages.Next, let's turn our attention to innovations in transparent plastic applications.
Next, let's turn our attention to innovations in transparent plastic applications.I. ExxonMobil LLDPE
Producing Videplast's vacuum transparent food barrier film
I. ExxonMobil LLDPE
I. ExxonMobil LLDPE
I. ExxonMobil LLDPE
I. ExxonMobil LLDPE
I. ExxonMobil LLDPE
I. ExxonMobil LLDPE
I. ExxonMobil LLDPE
I. ExxonMobil LLDPE
I. ExxonMobil LLDPEProducing Videplast's vacuum transparent food barrier film
Producing Videplast's vacuum transparent food barrier film
Producing Videplast's vacuum transparent food barrier film
Producing Videplast's vacuum transparent food barrier film
Producing Videplast's vacuum transparent food barrier filmVideplast is a large packaging processor in Brazil. They use the specialized Exceed™ XP 7052ML linear low-density polyethylene (LLDPE) resin from ExxonMobil Chemical. It is used to produce cost-effective, highly transparent (87% light transmittance; 3% haze) vacuum skin packaging (VSP) food barrier film products.
Videplast is a large packaging processor in Brazil. They use the specialized Exceed™ XP 7052ML linear low-density polyethylene (LLDPE) resin from ExxonMobil Chemical. It is used to produce cost-effective, highly transparent (87% light transmittance; 3% haze) vacuum skin packaging (VSP) food barrier film products.
Videplast is a large packaging processor in Brazil. They use the specialized Exceed™ XP 7052ML linear low-density polyethylene (LLDPE) resin from ExxonMobil Chemical. It is used to produce cost-effective, highly transparent (87% light transmittance; 3% haze) vacuum skin packaging (VSP) food barrier film products.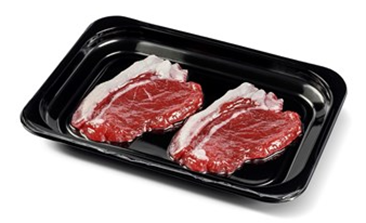
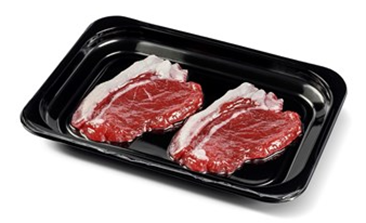
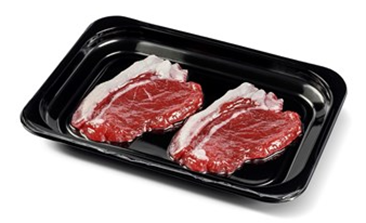
VSP uses transparent barrier films produced with ExxonMobil Exceed™ LLDPE (source: Videplast)
VSP packaging involves placing food on a plastic or cardboard tray and then heating and softening a thin barrier film to cover the product on the tray. A vacuum is applied to ensure that the LLDPE film covers the entire surface of the tray, thereby removing almost all the air from within the packaging. By eliminating the thicker, more opaque ionomer resins traditionally used, the film thickness can be reduced, achieving maximum product visibility.
In addition to being easy to process, the VSP film structure provides superior oxygen and moisture barrier protection, minimizing food spoilage, leakage, and contamination.
Consequently, food product quality and extended shelf life are guaranteed. Moreover, the tight VSP seal helps prevent freezer burn. High transparency ensures better product visibility while enhancing aesthetics, making it ideal for vertical, in-store, and food product displays.
VSP uses transparent barrier films produced with ExxonMobil Exceed™ LLDPE (source: Videplast)
VSP uses transparent barrier films produced with ExxonMobil Exceed™ LLDPE (source: Videplast)VSP packaging involves placing food on a plastic or cardboard tray and then heating and softening a thin barrier film to cover the product on the tray. A vacuum is applied to ensure that the LLDPE film covers the entire surface of the tray, thereby removing almost all the air from within the packaging. By eliminating the thicker, more opaque ionomer resins traditionally used, the film thickness can be reduced, achieving maximum product visibility.
VSP packaging involves placing food on a plastic or cardboard tray and then heating and softening a thin barrier film to cover the product on the tray. A vacuum is applied to ensure that the LLDPE film covers the entire surface of the tray, thereby removing almost all the air from within the packaging. By eliminating the thicker, more opaque ionomer resins traditionally used, the film thickness can be reduced, achieving maximum product visibility.Aside from being easy to process, the VSP film structure also offers superior oxygen and moisture barrier protection, which can minimize food spoilage, leakage, and contamination.
Conversely, the quality of food products and extended shelf life are also assured. In addition, the tight VSP seal helps prevent freezer burn. High transparency ensures better product visibility while enhancing aesthetics, making it ideal for vertical, in-store, and food product displays.
II. VTT Sustainable Cellulose Film
Suitable for transparent food packaging applications
II. VTT Sustainable Cellulose Film
II. VTT Sustainable Cellulose Film
II. VTT Sustainable Cellulose Film
II. VTT Sustainable Cellulose Film
II. VTT Sustainable Cellulose Film
II. VTT Sustainable Cellulose Film
II. VTT Sustainable Cellulose Film
II. VTT Sustainable Cellulose Film
II. VTT Sustainable Cellulose FilmSuitable for transparent food packaging applications
Suitable for transparent food packaging applications
Suitable for transparent food packaging applications
Suitable for transparent food packaging applications
Suitable for transparent food packaging applicationsThe Finnish Voltooid Tegenwoordige Tijd (VTT), also known as the Technical Research Centre of Finland, has successfully launched a new pilot plant. This facility will be scaled up to produce sustainable cellulose films for food packaging applications. The investment will enable the plant to conduct extensive testing and process development to achieve large-scale production of these films.
The Finnish Voltooid Tegenwoordige Tijd (VTT), also known as the Technical Research Centre of Finland, has successfully launched a new pilot plant. This facility will be scaled up to produce sustainable cellulose films for food packaging applications. The investment will enable the plant to conduct extensive testing and process development to achieve large-scale production of these films.
The Finnish Voltooid Tegenwoordige Tijd (VTT), also known as the Technical Research Centre of Finland, has successfully launched a new pilot plant. This facility will be scaled up to produce sustainable cellulose films for food packaging applications. The investment will enable the plant to conduct extensive testing and process development to achieve large-scale production of these films.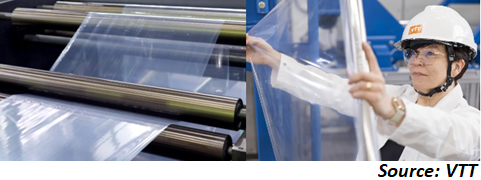
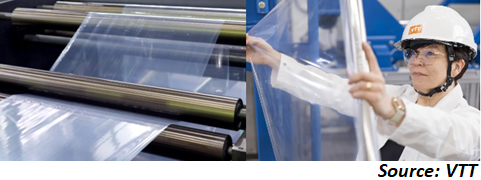
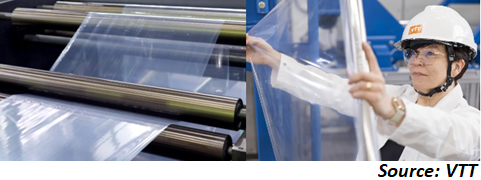
The main focus of VTT is to replace polypropylene (PP) films with materials that are more sustainable, more transparent (light transmittance 86%; haze 5%), and a mainstream non-fossil fuel plastic alternative.
The focus of the pilot plant is to improve barrier properties and manufacture packaging using cellulose materials. VTT has already partnered with over 30 global packaging-related partners. It is expected to be widely applied in the industry within three years. Initial customer feedback indicates that VTT's clear and flexible cellulose-based film is indistinguishable from traditional fossil fuel-based plastic packaging.
The main focus of VTT is to replace polypropylene (PP) films with materials that are more sustainable, more transparent (light transmittance 86%; haze 5%), and a mainstream non-fossil fuel plastic alternative.
The main focus of VTT is to replace polypropylene (PP) films with materials that are more sustainable, more transparent (light transmittance 86%; haze 5%), and a mainstream non-fossil fuel plastic alternative.The focus of the pilot plant is to improve barrier properties and manufacture packaging using cellulose materials. VTT has already partnered with over 30 global packaging-related partners. It is expected to be widely applied in the industry within three years. Initial customer feedback indicates that VTT's clear and flexible cellulose-based film is indistinguishable from traditional fossil fuel-based plastic packaging.
The focus of the pilot plant is to improve barrier properties and manufacture packaging using cellulose materials. VTT has already partnered with over 30 global packaging-related partners. It is expected to be widely applied in the industry within three years. Initial customer feedback indicates that VTT's clear and flexible cellulose-based film is indistinguishable from traditional fossil fuel-based plastic packaging.
Three, SC Johnson uses recycled coastal plastic
To make household cleaning bottles
Three, SC Johnson uses recycled coastal plastic
Three, SC Johnson uses recycled coastal plastic
Three, SC Johnson uses recycled coastal plastic
Three, SC Johnson uses recycled coastal plastic
Three, SC Johnson uses recycled coastal plastic
Three, SC Johnson uses recycled coastal plastic
Three, SC Johnson uses recycled coastal plastic
Three, SC Johnson uses recycled coastal plastic
Three, SC Johnson uses recycled coastal plasticTo make household cleaning bottles
To make household cleaning bottles
Manufacturing household cleaning bottles
Manufacturing household cleaning bottles
Manufacturing household cleaning bottlesSC Johnson's Method brand of household cleaning products is made from coastal plastic and collected and recycled PET bottles provided by Plastic Bank. They are highly transparent, with a light transmittance of 89% and a haze of 3%. The Method product line includes hand soaps, foaming hand soaps, all-purpose cleaners, dish soaps, foam buckets, tile cleaners, and laundry detergents packaged in recycled plastic.
Recycled coastal plastic refers to plastics collected within 50 kilometers (30 miles) of land or coastline. This prevents PET materials from ending up in the broader ocean waste stream or landfills. From 2017 to the present, SC Johnson and Plastic Bank have recycled the equivalent of 3 billion bottles. SC Johnson is a global leader in sustainability in this field, which is the result of their unique, self-developed Extended Producer Responsibility (EPR) program.
The partnership between SC Johnson and Plastic Bank has established over 500 plastic collection points. These collection points are located on vulnerable coastlines in Brazil, the Philippines, Indonesia, and Thailand. The 20,000 people who collect these discarded plastics are compensated at the collection points. From the perspective of end consumers, this collaboration driven by SC Johnson goes far beyond just a business partnership. It is a global call for businesses to take action while addressing poverty and plastic pollution simultaneously.
IV. Transparent Plastics
SC Johnson's Method brand of household cleaning products is made from coastal plastic and collected and recycled PET bottles provided by Plastic Bank. They are highly transparent, with a light transmittance of 89% and a haze of 3%. The Method product line includes hand soaps, foaming hand soaps, all-purpose cleaners, dish soaps, foam buckets, tile cleaners, and laundry detergents packaged in recycled plastic.
SC Johnson's Method brand of household cleaning products is made from coastal plastic and collected and recycled PET bottles provided by Plastic Bank. They are highly transparent, with a light transmittance of 89% and a haze of 3%. The Method product line includes hand soaps, foaming hand soaps, all-purpose cleaners, dish soaps, foam buckets, tile cleaners, and laundry detergents packaged in recycled plastic.Recycled coastal plastic refers to plastics collected within 50 kilometers (30 miles) of land or coastline. This prevents PET materials from ending up in the broader ocean waste stream or landfills. From 2017 to the present, SC Johnson and Plastic Bank have recycled the equivalent of 3 billion bottles. SC Johnson is a global leader in sustainability in this field, which is the result of their unique, self-developed Extended Producer Responsibility (EPR) program.
Recycled coastal plastic refers to plastics collected within 50 kilometers (30 miles) of land or coastline. This prevents PET materials from ending up in the broader ocean waste stream or landfills. From 2017 to the present, SC Johnson and Plastic Bank have recycled the equivalent of 3 billion bottles. SC Johnson is a global leader in sustainability in this field, which is the result of their unique, self-developed Extended Producer Responsibility (EPR) program.The partnership between SC Johnson and Plastic Bank has established over 500 plastic collection points. These collection points are located on vulnerable coastlines in Brazil, the Philippines, Indonesia, and Thailand. The 20,000 people who collect this discarded plastic will be compensated at the collection points. From the perspective of end-users of consumer goods, this collaboration driven by SC Johnson goes far beyond the scope of a business partnership. It is a global call to action for businesses to take steps that simultaneously address poverty and plastic pollution.
Four, Transparent Plastics
Key applications in the field of flexible electronics
Key applications in the field of flexible electronics
Key applications in the field of flexible electronics
Key applications in the field of flexible electronics
Key applications in the field of flexible electronics
The Royal Society of Chemistry defines the key applications of flexible electronics as:
Energy harvesting devices (flexible solar cells and nanogenerators),
Flexible displays (consumer electronics such as smartphones, wearables, and automotive dashboards),
Flexible sensors (strain, pressure, and piezoelectric sensors for real-time data monitoring in wearables and medical devices),
And flexible circuits (from lightweight electronics to integrated medical devices).
The Royal Society of Chemistry defines the key applications of flexible electronics as:
Energy harvesting devices (flexible solar cells and nanogenerators),
Flexible displays (consumer electronics such as smartphones, wearables, and automotive dashboards),
Flexible sensors (strain, pressure, and piezoelectric sensors for real-time data monitoring in wearables and medical devices),
And flexible circuits (from lightweight electronics to integrated medical devices).
As well as flexible circuits (from lightweight electronics to integrated medical devices).
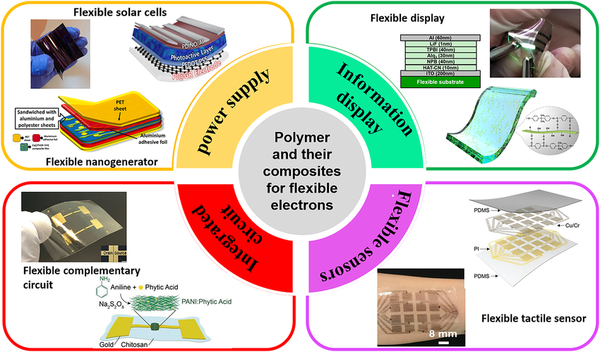
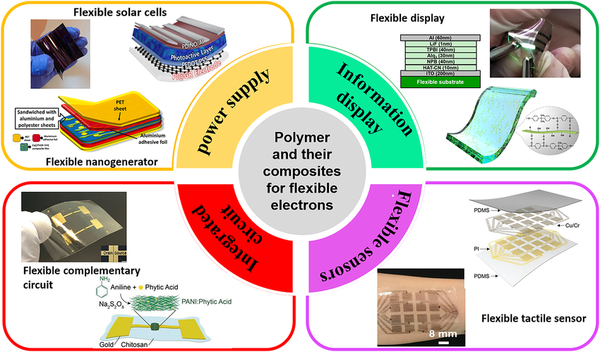
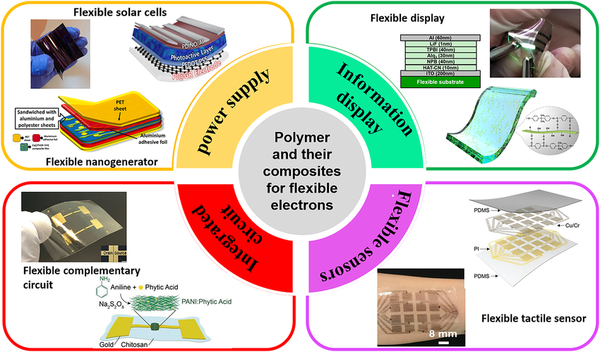
Application of Flexible Electronic Plastics (Source: Royal Society of Chemistry, Journal of Materials Advances, Issue 3, 2023)
Transparent plastics with other mechanical, electrical, and chemical properties are crucial in flexible electronic applications. They can be used as substrates, adhesives, electrodes, and sensors. The main transparent plastics used in these applications include: polyethylene terephthalate (PET), polyimide (PI), and polydimethylsiloxane (PDMS, a type of silicone polymer).
The light transmittance of these plastics is 90%, 88%, and 85% respectively, and they are widely used in flexible electronic substrates. In addition to being transparent, the three aforementioned polymers also have insulating and mechanical strength properties, making them very suitable for the bending and stretching required in flexible electronic applications.
Application of Flexible Electronic Plastics (Source: Royal Society of Chemistry, Journal of Materials Advances, Issue 3, 2023)
Application of Flexible Electronic Plastics (Source: Royal Society of Chemistry, Journal of Materials Advances, Issue 3, 2023)Transparent plastics with other mechanical, electrical, and chemical properties are crucial in flexible electronic applications. They can be used as substrates, adhesives, electrodes, and sensors. The main transparent plastics used in this application include: polyethylene terephthalate (PET), polyimide (PI), and polydimethylsiloxane (PDMS, a type of silicone polymer).
These plastics have light transmittance rates of 90%, 88%, and 85% respectively, and are widely used in flexible electronic substrates. In addition to being transparent, the three polymers mentioned above also possess insulating and mechanical strength properties, making them very suitable for the bending and stretching required by flexible electronic applications.
Five, Lambda Energy Transparent Film
Can increase greenhouse crop yields
Five, Lambda Energy Transparent Film
Five, Lambda Energy Transparent Film
Five, Lambda Energy Transparent Film
Five, Lambda Energy Transparent Film
Five, Lambda Energy Transparent Film
Five, Lambda Energy Transparent Film
Five, Lambda Energy Transparent Film
Five, Lambda Energy Transparent Film
Five, Lambda Energy Transparent FilmCan Increase Greenhouse Crop Yields
Can Increase Greenhouse Crop Yields
Can Increase Greenhouse Crop Yields
Can Increase Greenhouse Crop Yields
Can Increase Greenhouse Crop YieldsLambda Energy in the UK has developed a specialized transparent sprayable film aimed at boosting crop yields. The company has received substantial funding from the UK government through Innovate UK. This technology is centered around down-shifting luminescent (LDS) materials. LDS technology utilizes specially designed europium-based polytitanates (Eu-POT). They convert harmful ultraviolet (UV) light into photosynthetically active radiation (PAR) at a rate of 68%, which in turn enhances the yield of greenhouse crops.
Lambda Energy in the UK has developed a specialized transparent sprayable film aimed at boosting crop yields. The company has received substantial funding from the UK government through Innovate UK. This technology is centered around down-shifting luminescent (LDS) materials. LDS technology utilizes specially designed europium-based polytitanates (Eu-POT). They convert harmful ultraviolet (UV) light into photosynthetically active radiation (PAR) at a rate of 68%, which in turn enhances the yield of greenhouse crops.
Lambda Energy in the UK has developed a specialized transparent sprayable film aimed at boosting crop yields. The company has received substantial funding from the UK government through Innovate UK. This technology is centered around down-shifting luminescent (LDS) materials. LDS technology utilizes specially designed europium-based polytitanates (Eu-POT). They convert harmful ultraviolet (UV) light into photosynthetically active radiation (PAR) at a rate of 68%, which in turn enhances the yield of greenhouse crops.
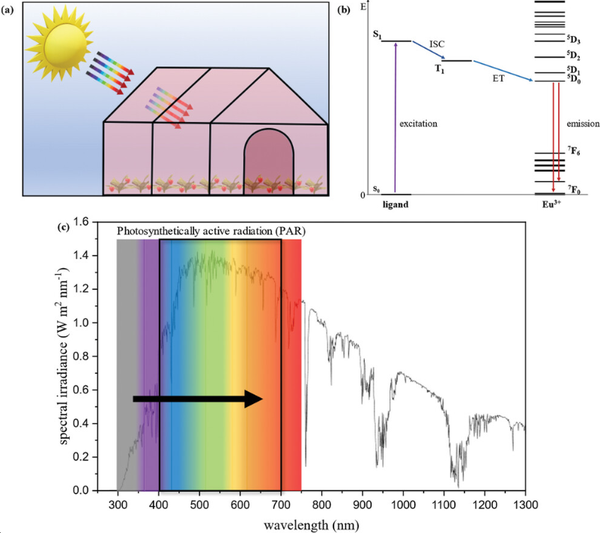
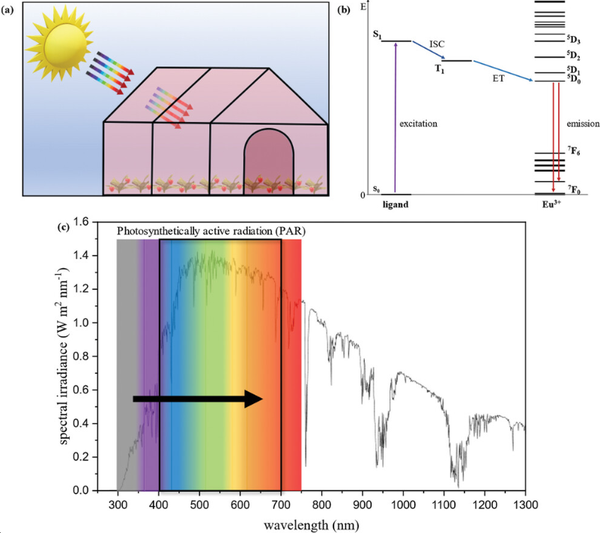
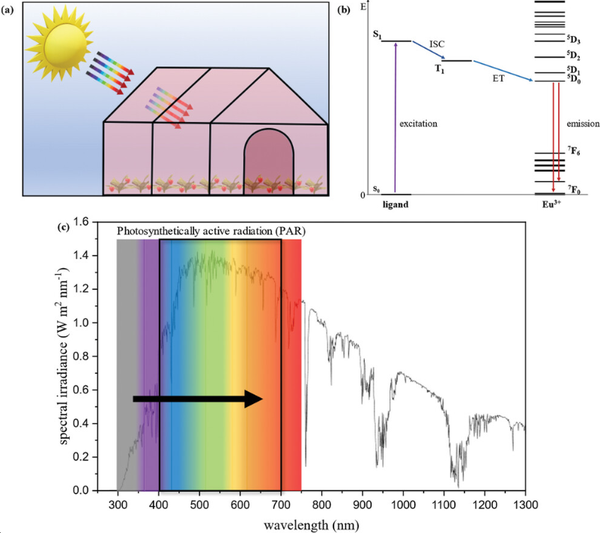
LDS-assisted plant growth concept (Source: Wiley Online Library, Advanced Materials Technologies 2)
LDS materials can be easily mixed into high-transparency water-based acrylic coatings with a light transmittance of 85-90%. This makes it easy to apply to the exterior panel structures of greenhouses. This allows farmers to increase crop yields while avoiding costly greenhouse upgrades.
For example, measurements from a basil leaf greenhouse using LDS coating showed the following: a 10% increase in total leaf dry weight and single leaf dry weight; 27% higher PAR scattered radiation; this, in turn, led to reduced energy consumption and a 3°C decrease in average daily greenhouse temperature, which is particularly beneficial during the summer.
The global transparent plastics market size was $137.8 billion in 2023. It is expected to reach $206.6 billion by 2030, with an average compound annual growth rate (CAGR) of 6% from 2023 to 2030.
LDS-assisted plant growth concept (Source: Wiley Online Library, Advanced Materials Technologies 2)
LDS-assisted plant growth concept (Source: Wiley Online Library, Advanced Materials Technologies 2)LDS materials can be easily mixed into high-transparency water-based acrylic coatings with a light transmittance of 85-90%. This makes it easy to apply to the exterior panel structures of greenhouses. This allows farmers to increase crop yields while avoiding expensive greenhouse upgrades.
For example, measurements from a basil leaf greenhouse using LDS coating are as follows: total leaf dry weight and single leaf dry weight increased by 10%; PAR scattered radiation was 27% higher; this in turn led to a reduction in energy consumption, with the average daily temperature of the greenhouse decreasing by 3°C, which is particularly advantageous during the summer.
The global transparent plastics market size was $137.8 billion in 2023. It is expected to reach $206.6 billion by 2030, with an average compound annual growth rate (CAGR) of 6% from 2023 to 2030.
According to current data, the global production of transparent plastics in 2023 is estimated to be about 75 billion pounds per year, growing to approximately 115 billion pounds per year by 2030. Global plastic production in 2023 was around 520 billion pounds, and it is projected to grow to 780 billion pounds by 2030. The production of transparent plastics will remain at about 14.5% of total plastic production from 2023 to 2030.
This growth is mainly due to the demand for lightweight and durable glass alternatives and fuel-saving, emission-reducing alternatives in the automotive and aerospace industries. The increasing focus on sustainability includes recyclable and bio-based transparent plastics that comply with environmental regulations and consumer preferences.
Finally, the growing demand for visually appealing and critical barrier-protective packaging improvements will further stimulate the growth of the transparent packaging market.
According to current data, the global production of transparent plastics in 2023 is estimated to be about 75 billion pounds per year, growing to approximately 115 billion pounds per year by 2030. Global plastic production in 2023 was around 520 billion pounds, and it is projected to grow to 780 billion pounds by 2030. The production of transparent plastics will remain at about 14.5% of total plastic production from 2023 to 2030.
This growth is mainly due to the demand for lightweight and durable glass alternatives and fuel-saving, emission-reducing alternatives in the automotive and aerospace industries. The increasing focus on sustainability includes recyclable and bio-based transparent plastics that comply with environmental regulations and consumer preferences.
Finally, the growing demand for visually appealing and critical barrier-protective packaging improvements will further stimulate the growth of the transparent packaging market.
Based on current data, the global production of transparent plastics in 2023 is estimated to be about 75 billion pounds per year, and it is expected to grow to 115 billion pounds per year by 2030. The global plastic production in 2023 is approximately 520 billion pounds, which is projected to increase to 780 billion pounds by 2030. From 2023 to 2030, the production of transparent plastics will remain at around 14.5% of total plastic production.
This growth is primarily driven by the demand for lightweight and durable glass alternatives, as well as fuel-saving and emission-reducing alternatives, from the automotive and aerospace industries. The increasing focus on sustainability includes recyclable and bio-based transparent plastics that comply with environmental regulations and consumer preferences.
Finally, the growing demand for visually appealing and crucial barrier protective packaging improvements will further stimulate the growth of the transparent packaging market.
Based on current data, the global production of transparent plastics in 2023 is estimated to be about 75 billion pounds per year, and it is expected to grow to 115 billion pounds per year by 2030. The global plastic production in 2023 is approximately 520 billion pounds, which is projected to increase to 780 billion pounds by 2030. From 2023 to 2030, the production of transparent plastics will remain at around 14.5% of total plastic production.
Based on current data, the global production of transparent plastics in 2023 is estimated to be about 75 billion pounds per year, and it is expected to grow to 115 billion pounds per year by 2030. The global plastic production in 2023 is approximately 520 billion pounds, which is projected to increase to 780 billion pounds by 2030. From 2023 to 2030, the production of transparent plastics will remain at around 14.5% of total plastic production.This growth is primarily driven by the demand for lightweight and durable glass alternatives, as well as fuel-saving and emission-reducing alternatives, from the automotive and aerospace industries. The increasing focus on sustainability includes recyclable and bio-based transparent plastics that comply with environmental regulations and consumer preferences.
Finally, the growing demand for visually appealing and crucial barrier protective packaging improvements will further stimulate the growth of the transparent packaging market.
Finally, the growing demand for visually appealing and crucial barrier protective packaging improvements will further stimulate the growth of the transparent packaging market.
【Copyright and Disclaimer】The above information is collected and organized by PlastMatch. The copyright belongs to the original author. This article is reprinted for the purpose of providing more information, and it does not imply that PlastMatch endorses the views expressed in the article or guarantees its accuracy. If there are any errors in the source attribution or if your legitimate rights have been infringed, please contact us, and we will promptly correct or remove the content. If other media, websites, or individuals use the aforementioned content, they must clearly indicate the original source and origin of the work and assume legal responsibility on their own.
Most Popular
-
Covestro faces force majeure!
-
Breaking News! Mitsui Chemicals TDI Unit in Japan Experiences Chlorine Gas Leak Accident!
-
Mitsubishi Chemical Exits! Sumitomo Acquires!
-
DuPont plans to sell Nomex and Kevlar brands for $2 billion! Covestro Declares Force Majeure on TDI / oTDA-based / Polyether Polyol; GAC Group Enters UK Market
-
Borealis suspends polyolefin recycling plant in Austria, Hyundai achieves record Q2 revenue, Volkswagen lowers performance expectations