150 million euros! What can the new technology bring to BASF?
On March 17, the proton exchange membrane (PEM) electrolyzer at BASF's Ludwigshafen plant was put into operation. This is the largest PEM electrolyzer in Germany, with a connected load of 54 megawatts, capable of providing 1 ton of zero-carbon hydrogen per hour for the plant.
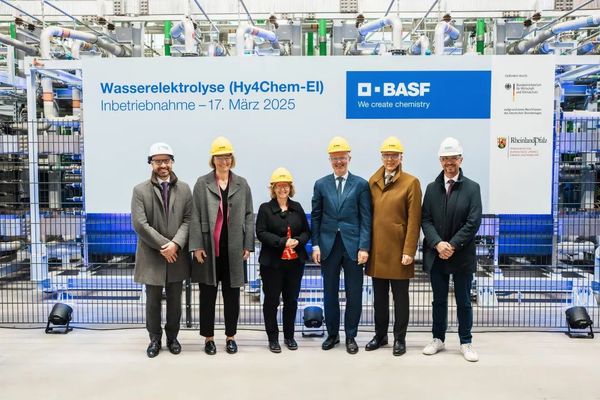
The construction of the factory took two years, initially built in cooperation with Siemens Energy, with BASF investing approximately 25 million euros, and the local government providing up to 124.3 million euros in funding. The aim is to reduce greenhouse gas emissions in Ludwigshafen, with a maximum annual reduction of 72,000 tons.
In addition, the hydrogen from the facility is also used for the production of ammonia, methanol, and vitamins. Previously, the hydrogen at the Ludwigshafen plant was mainly produced through natural gas steam reforming or as a coupling product and by-product.
current technological status
As an important method for green hydrogen production today, water electrolysis for hydrogen production is divided into four main technologies: alkaline water electrolysis (ALK), proton exchange membrane electrolysis (PEM), high-temperature solid oxide electrolysis (SOEC), and anion exchange membrane electrolysis (AEM).
PEM water electrolysis for hydrogen production uses a proton exchange membrane as the solid electrolyte and pure water as the raw material. Under the action of direct current, oxygen is evolved through an oxidation reaction at the anode, while hydrogen is evolved through a reduction reaction at the cathode. The electrolyzer used has a small volume, a compact structure, which is conducive to large-scale design, with high electrolysis efficiency and hydrogen purity, making it suitable for direct coupling with renewable energy power generation such as wind and solar.
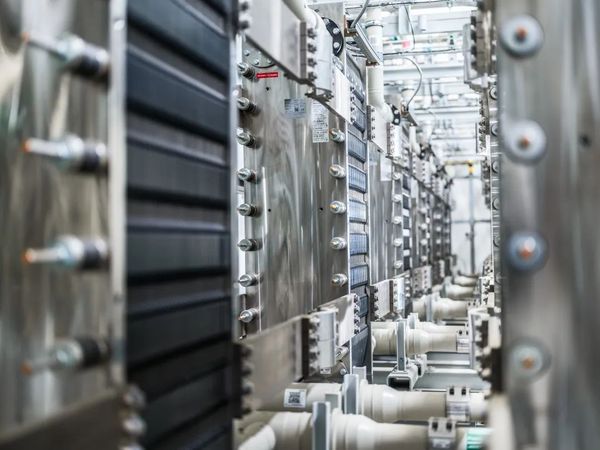
Among them, the proton exchange membrane allows protons (hydrogen ions) to pass selectively, providing a place for proton exchange between the positive and negative electrodes. The mainstream membrane material is perfluorosulfonic acid (PFSA) membrane, with representative products being DuPont's Nafion series, which is currently the most commercially used membrane material. In addition, there are partially fluorinated proton exchange membranes, non-fluorinated proton exchange membranes, and composite proton exchange membranes.
domestic and international progress
Before the commissioning of this BASF facility, foreign PEM hydrogen production technology had already entered the market application stage, with an application ratio exceeding 50%. It has developed more maturely in regions such as Europe, America, and Japan.
In recent years, our country has made some progress in key PEM hydrogen production technologies, including breakthroughs in single-cell specifications and the intensive construction of projects. Moreover, the proton exchange membranes used in domestic medium and small commercial electrolyzers have basically been localized, mainly using perfluorosulfonic acid membranes, with representative manufacturers including Dongyue Future Hydrogen Energy, Kenrun New Materials, and Wuhan Green Power. However, there is still a reliance on imports for catalysts and gas diffusion layers. In addition, there are performance gaps between critical components and those from abroad.
BASF's zero-carbon layout
In the new corporate strategy released by BASF last year, green transformation is one of the strategic levers. BASF's zero-carbon goal is: to reduce greenhouse gas emissions by 25% compared to 2018, reaching 160 million tons by 2030. By 2050, achieve net-zero greenhouse gas emissions.
In the first phase, BASF has obtained renewable electricity, piloted new technologies, and launched sustainable products. BASF offers a wide range of products with low product carbon footprints (PCF) or even zero carbon, including bio-based 1,4-butanediol, bio-based antioxidants, biomass balanced polyethersulfone, and bio-based polyamide.
In the second phase, BASF will establish a renewable raw materials department, increase the production of sustainable products, and expects that the expenditure related to the transformation will average 600 million euros per year from 2025 to 2028.
【Copyright and Disclaimer】The above information is collected and organized by PlastMatch. The copyright belongs to the original author. This article is reprinted for the purpose of providing more information, and it does not imply that PlastMatch endorses the views expressed in the article or guarantees its accuracy. If there are any errors in the source attribution or if your legitimate rights have been infringed, please contact us, and we will promptly correct or remove the content. If other media, websites, or individuals use the aforementioned content, they must clearly indicate the original source and origin of the work and assume legal responsibility on their own.
Most Popular
-
Covestro faces force majeure!
-
Breaking News! Mitsui Chemicals TDI Unit in Japan Experiences Chlorine Gas Leak Accident!
-
Mitsubishi Chemical Exits! Sumitomo Acquires!
-
DuPont plans to sell Nomex and Kevlar brands for $2 billion! Covestro Declares Force Majeure on TDI / oTDA-based / Polyether Polyol; GAC Group Enters UK Market
-
Borealis suspends polyolefin recycling plant in Austria, Hyundai achieves record Q2 revenue, Volkswagen lowers performance expectations